Die casting ejector pins play a pivotal role in the manufacturing industry, serving as essential components in the die casting process. These seemingly simple tools are integral to ensuring the smooth removal of cast parts from molds, preventing damage and maintaining the integrity of the final product. As a seasoned expert in die casting with decades of hands-on experience, I can attest to the paramount importance of selecting high-quality ejector pins and understanding their application.
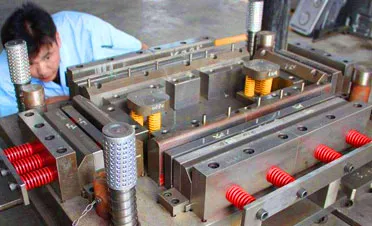
When it comes to die casting,
the precision of ejector pins cannot be overstated. These pins are responsible for pushing the cast part out of the mold once it has solidified. It’s crucial they function flawlessly to avoid defects in the final product. One common issue manufacturers face is the bending or breaking of these pins, which is often a result of using substandard materials. High-grade steel, like H13 or SKD61, is typically recommended for its durability and resistance to heat, ensuring the pins can withstand the rigorous conditions of die casting.
Furthermore, the design and placement of ejector pins are vital components that influence the quality of the die cast parts. Strategic positioning can minimize stress on the part and reduce warping or other deformation as it is ejected. This design expertise requires a deep understanding of both the die casting process and the mechanical properties of metals being cast. Professionals must consider factors such as part geometry and gating system design to optimize ejector pin placement.

Real-world application of ejector pins showcases their critical function. In an automotive manufacturing setup, for instance, ejector pins are used to produce complex components like engine blocks and transmission cases. These components must meet stringent tolerances and specifications to function correctly in a vehicle. Any deviation in dimensions resulting from inadequate ejection can lead to significant operational failures, emphasizing the need for precision and reliability in ejector pin performance.
die casting ejector pins
Moreover, consistency in the manufacturing process is a testament to the expertise required to maintain high standards. Regular maintenance and inspection of die casting equipment, including ejector pins, are necessary practices. The most reliable manufacturers implement rigorous quality assurance protocols, including real-time monitoring and post-production inspections. By doing so, they ensure each batch of products meets or exceeds industry standards, thereby bolstering their reputation for quality and reliability.
In terms of trustworthiness, sourcing ejector pins from reputable manufacturers cannot be overlooked. Trusted suppliers often provide comprehensive data sheets and certifications verifying the quality and origin of their materials. This transparency is crucial for manufacturers in assessing the suitability of ejector pins for their specific applications.
Overall, the effectiveness of die casting ejector pins stems from a blend of high-quality materials, precise engineering, and consistent performance monitoring. By choosing the right pins and maintaining rigorous standards, manufacturers can significantly enhance product quality and production efficiency. This expert insight underscores the indispensable role of ejector pins in the realm of die casting, cementing their importance in achieving durable and high-quality metal cast products.