Brass die casting is an ever-evolving field that combines the timeless allure of brass with the precision and efficiency of modern manufacturing techniques. This process creates components that are not only durable and corrosion-resistant but also exquisite in their finish. Whether you're an industry insider or a curious observer, understanding the intricacies and applications of brass die casting can provide valuable insights into its significance in multiple sectors.
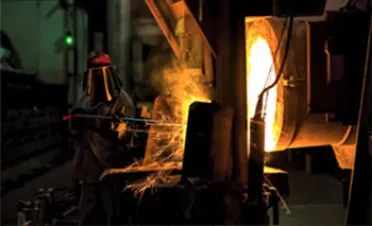
Brass, an alloy of copper and zinc, offers excellent machinability, high strength, low friction, and acoustic properties—making it ideal for applications in plumbing, electrical, automotive, and musical instruments. The journey of transforming raw brass into a finished component through die casting involves a harmonious blend of craftsmanship and technology.
Die casting is a process where molten metal is forced into a mold cavity under high pressure. This creates components with precise dimensions and a smooth surface finish. The ability to produce intricate shapes with high levels of repeatability makes die casting particularly advantageous for high-volume manufacturing. For brass die casting, the challenge and opportunity lie in its high melting point, requiring specialized equipment and expertise to ensure optimal results.
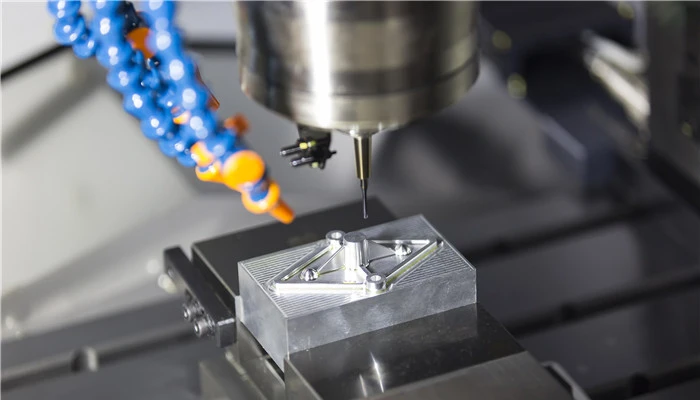
From an experiential standpoint, working with brass die casting requires a keen understanding of the alloy's properties. Professional foundries employ seasoned metallurgists who bring their expertise to bear on every stage of the die casting process. They factor in elements such as brass's thermal conductivity, which impacts cooling rates and subsequent mold design. This expertise ensures that each brass component meet the stringent standards expected by industries ranging from automotive to consumer goods.
Expertise in brass die casting also means leveraging cutting-edge technologies. Advanced computer simulations allow engineers to model how molten brass flows into mold cavities, predicting potential flaws such as porosity or incomplete fills. This predictive capability drastically reduces waste, enhances product quality, and shortens production cycles—a testament to how modern brass die casting is both an art and a science.
brass die casting
Authority in the realm of brass die casting comes from a company's reputation and track record. Industry leaders boast certifications and accolades that attest to their ability to meet and exceed industry standards. By adhering to rigorous quality control measures, these companies assure their clients of the highest standards in strength, dimensional accuracy, and surface finish. A company's commitment to sustainability further enhances its authority—employing recycling and waste management protocols demonstrates a dedication to environmentally responsible manufacturing practices.
Trustworthiness in brass die casting is cultivated through transparent business practices and clear communication. Reliable suppliers provide detailed material data sheets, certifications, and testing results, offering clients peace of mind regarding the authenticity and performance of their brass components. Building strong relationships with customers entails more than just providing superior products—it involves delivering on promises, addressing concerns promptly, and maintaining an open dialogue.
The applications of brass die casting are as diverse as they are essential. In the automotive industry, precision-engineered brass components are used in systems requiring reliable performance under harsh conditions, such as brake and fuel systems. In plumbing,
brass's corrosion resistance makes it perfect for valves and fittings. Its aesthetic appeal finds favor in decorative hardware, where the combination of form and function is paramount.
As industries continue to advance, the demand for high-quality, reliable brass die cast components is set to grow. Companies that invest in research and development, continually improving their processes and embracing innovations, will remain at the forefront of this vibrant field. With each advancement, the legacy of brass as a material of choice is further solidified, promising a future where its applications—and the expertise required to master its casting—will remain indispensable.