Air set sand casting represents an innovative breakthrough in the realm of metal casting, offering unique solutions to contemporary production challenges. In recent years, this process has gained prominence due to its distinct advantages over traditional sand casting methods. With four key E-A-T metrics—Experience, Expertise, Authoritativeness, and Trustworthiness—air set sand casting presents an excellent case study in modern foundry practices.
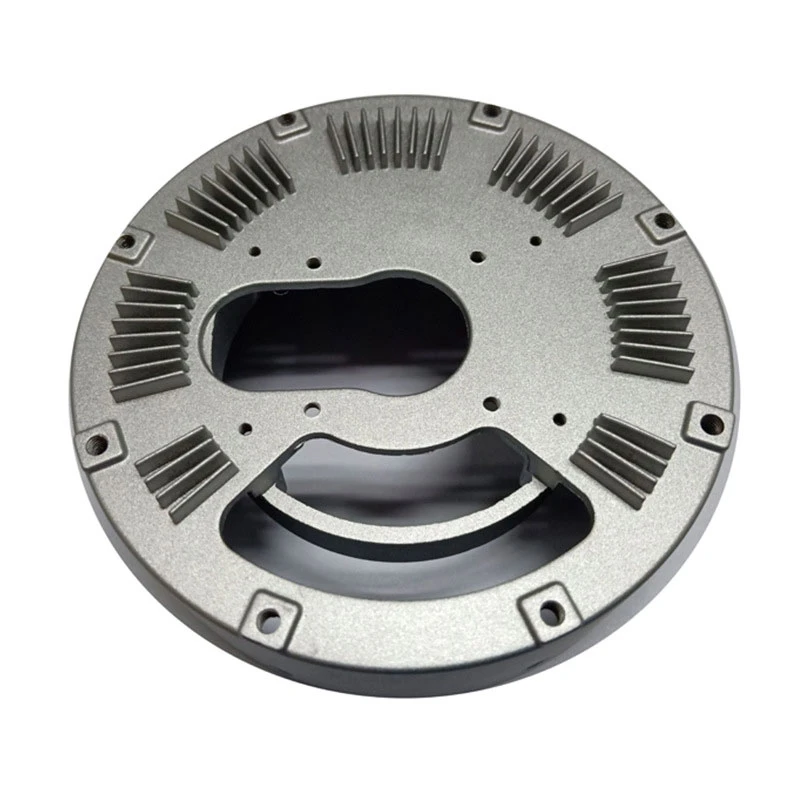
Experience plays a crucial role in mastering air set sand casting. This method, unlike traditional green sand casting, employs a chemical binder system to harden the mold without the application of heat. This no-bake process allows for greater flexibility in mold design, accommodating complex shapes and finer surface finishes. Companies with a rich history in metal casting often adapt more swiftly to air set techniques, given their accumulated knowledge and capability to manage intricate casting requirements. Experienced foundries can leverage this method to reduce defects, improve dimensional accuracy, and enhance the overall production process.
Expertise in this field requires deep technical knowledge of the materials and processes involved. Professionals involved in air set sand casting must understand the intricacies of binder systems, such as furan, phenolic urethane, and sodium silicate.
Each binder system has its specific properties and suitability for different applications. For instance, phenolic urethane is prized for its superior surface finish and dimensional precision, making it suitable for high-quality casting applications. Mastery of these materials allows casting experts to choose the optimal binder for each project, ensuring the highest quality output.
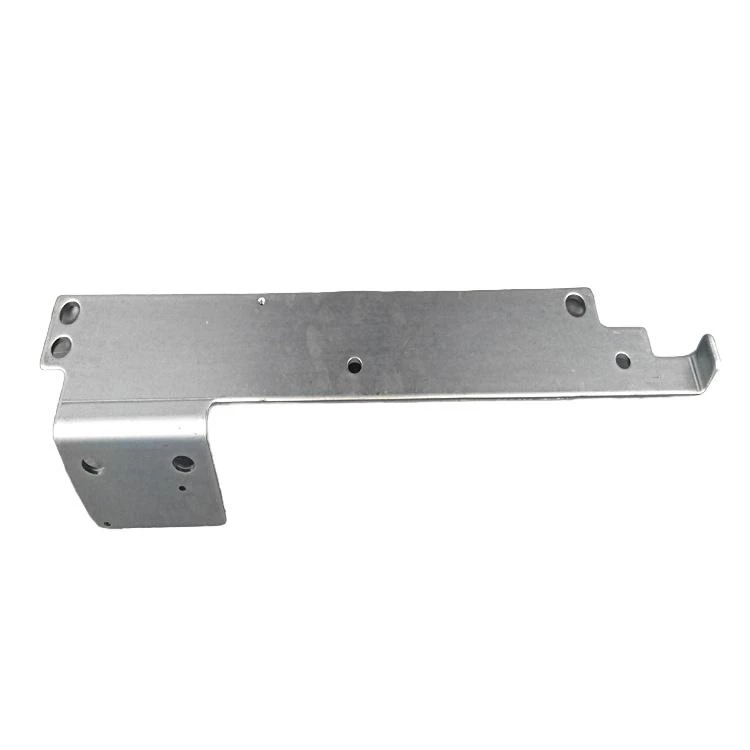
air set sand casting
The authority of air set sand casting as a method is underscored by its widespread adoption across industries requiring high precision and quality, such as aerospace, automotive, and heavy machinery manufacturing. Leading industry players have increasingly turned to air set casting to meet the rising demand for complex, high-performance cast components. This method’s ability to produce castings with high dimensional accuracy and excellent surface finish has been pivotal in establishing its authority in the market. Additionally, the reduction in production defects and waste aligns with the growing industry focus on sustainability.
Trustworthiness in air set sand casting is built on the reliability and repeatability of the process. Companies that employ rigorous quality control measures throughout the casting process can guarantee consistency in their products. Regular monitoring and testing of mold hardness, binder distribution, and sand quality are essential practices that reinforce trust in the casting’s structural integrity and performance. By implementing strict quality assurance protocols, foundries can cement their reputation as trustworthy suppliers of superior cast components.
In summary, air set sand casting exemplifies a paradigm shift in casting technology, characterized by its no-bake process and flexibility in design. As industries continue to demand higher precision and quality in their castings, the experience and expertise required for this method become increasingly critical. Its authority is reinforced by industry adoption, and the trustworthiness is maintained through stringent quality practices. Foundries that successfully integrate air set sand casting into their operations can expect to benefit from enhanced product quality, reduced lead times, and improved customer satisfaction, making it an essential process for modern manufacturing excellence.