Stamping aluminum parts is a critical process in various industries, offering a blend of precision, speed, and cost-effectiveness that is hard to match. With the increasing demand for lightweight and durable products, aluminum stamping has become integral in sectors ranging from automotive to consumer electronics. This article explores the intricacies of this process, drawing on expert insights and real-world applications to provide a comprehensive understanding.
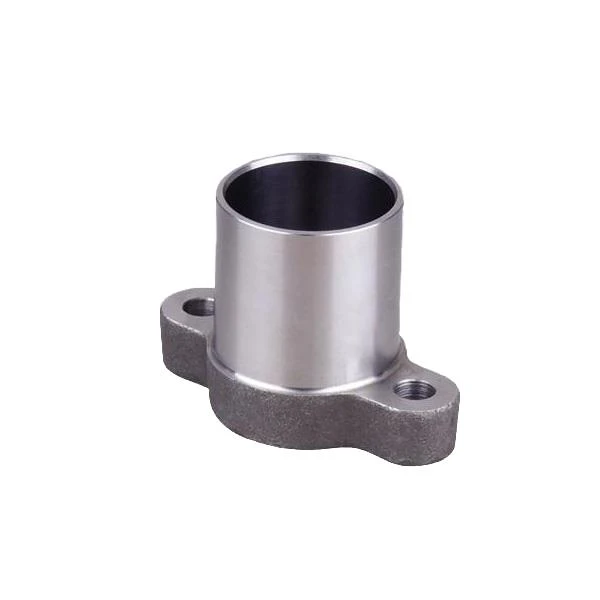
Aluminum stamping involves the use of a stamping press under conditions where aluminum sheets or strips are placed into a press and formed into specific shapes. The versatility of aluminum makes it an ideal candidate for stamping, as it combines strength with light weight, a key requirement in industries like aerospace and automotive. This weight reduction is not just beneficial for performance and efficiency but also helps in reducing emissions, aligning with global sustainability goals.
In terms of expertise, the process requires a profound understanding of both the material characteristics and the stamping technology. Aluminum's unique properties, such as high ductility and thermal conductivity, necessitate specialized equipment and tools. High-quality dies made from robust materials must be used to withstand the pressures involved, ensuring precision and consistency across batches. The correct choice of lubricant is also crucial to minimize friction and wear, thus prolonging the life of the dies and ensuring high-quality finishes.
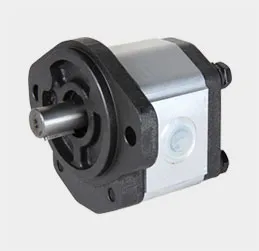
From an authoritative standpoint, manufacturers and technicians can leverage various advanced technologies to enhance aluminum stamping. The integration of computer-aided design (CAD) and manufacturing (CAM) software allows for precise modeling and simulation before the actual stamping process takes place. This technological integration not only enhances accuracy but also optimizes the material usage, thereby reducing waste and increasing overall efficiency.
Real-world experience also highlights the importance of proper die maintenance and regular calibration of equipment. Regular inspections and maintenance play a vital role in preventing breakdowns and ensuring the longevity of machinery. In addition, understanding the specific demands of each application, whether in crafting parts for high-stress environments or delicate consumer products, allows for the customization of processes to meet rigorous industry standards.
stamping aluminum parts
In terms of trustworthiness, stamping facilities aiming for excellence should be certified in accordance with international standards such as ISO or IATF. These certifications reflect a commitment to quality and continuous improvement, reassuring clients of the reliability and performance of the stamped parts. An emphasis on quality control, including detailed inspections at every production stage, further enhances trust, ensuring that every piece meets the required specifications and delivers on performance.
Moreover, continuous advancements in stamping technology, such as servo-driven presses and automated systems, have paved the way for greater precision and flexibility. These innovations not only reduce production time but also facilitate complex designs that were once thought to be difficult or impossible with traditional methods.
Building a reputation for reliability, efficiency, and high standards ultimately contributes to a stamping facility's authority in the field. By focusing on quality, leveraging cutting-edge technology, and maintaining rigorous standards, businesses provide clients with a trusted partnership, ensuring the production of top-tier aluminum parts that meet the most demanding requirements.
In conclusion, stamping aluminum parts is a sophisticated process that calls for a balance of expertise, the latest technologies, and a commitment to quality. Industries looking to incorporate aluminum stamping need to understand its nuances and invest in the right resources and technologies to achieve optimal results. As demands continue to evolve, so too will the methodologies and innovations in aluminum stamping, further establishing it as a cornerstone of modern manufacturing solutions.