In the expansive realm of industrial manufacturing, the nuanced distinctions between sand casting and die casting are pivotal for decision-making in product development. These two methods, each with unique characteristics and applications, hold significant importance in manufacturing high-quality metal components.
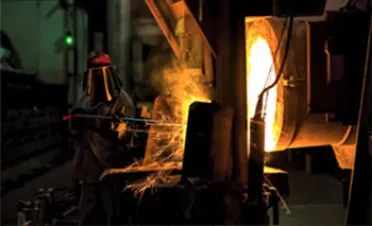
Understanding Sand Casting
Sand casting is one of the oldest casting techniques, but its versatility and effectiveness in producing complex geometries remain unmatched. This process begins by creating a mold from a sand mixture, where the cavity is formed into the desired shape of the final product. The sand's moldability allows manufacturers to consider intricate designs and reinforcements.
The Experience of Using Sand Casting
Manufacturers often cite sand casting as exceptional in creating large and heavy components. Its ability to utilize various metal alloys, including iron, aluminum, and copper, showcases its adaptability. Companies specializing in heavy machinery, automotive parts, and architecture have relied heavily on sand casting, given its capabilities in accommodating large designs without losing structural integrity.
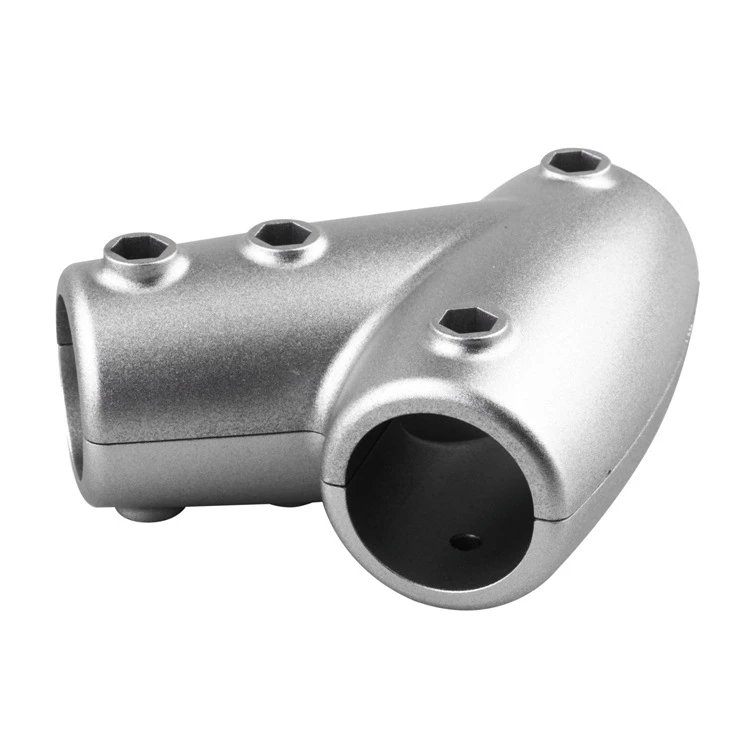
Professional Insights
Experts in the field often highlight that sand casting offers cost-effectiveness when dealing with low-volume production runs or custom orders. The primary reason is the lower tooling cost compared to other casting methods. Furthermore, experienced foundry workers can swiftly modify sand mold designs on-site, allowing for enhanced customization without extending lead times.
Authority and Reliability
Sand casting's proven traction across centuries is a testament to its reliability. The process has undergone significant enhancements with modern technology, improving precision and minimizing defects. Regulatory bodies involved in manufacturing standards continually endorse sand casting as a highly adaptable and dependable method for diverse industrial applications.
Exploring Die Casting
Contrastingly, die casting is a more modern technique known for producing high volumes of small to medium-sized precision parts. It uses a permanent mold format, typically made from steel, into which molten metal is injected under high pressure.
sand casting and die casting
Hands-On Experience with Die Casting
Manufacturers appreciate die casting for its ability to achieve fine details and smooth surface finishes. The process is highly efficient in producing components with tight tolerances and minimal machining required post-casting. Industries such as electronics, automotive, and consumer goods frequently employ die casting for parts like housings, brackets, and gears.
Expertise in Die Casting
Professionals recognize that the upfront investment in die casting molds is higher. However, this expenditure is justified by the long-term benefits for extensive production runs. Advanced die casting operations now leverage computer-aided design (CAD) and automation to increase precision and reduce cycle times, solidifying its place as a top choice for precision manufacturing.
Authoritative and Trustworthy Method
The stringent quality controls and materials testing protocols governing die casting ensure its products meet the stringent requirements of various industries. It is widely trusted due to its consistent output and capability to maintain quality across mass production. The method aligns with standards such as ISO 9001 and other international certifications, reinforcing its authoritative status in manufacturing.
Making an Informed Choice
When deciding between sand casting and die casting, several factors must be weighed production volume, budget, complexity of design, and desired material properties. Sand casting is ideal for larger, more complex items in smaller quantities, while die casting suits high-volume runs of intricate, lighter components.
Conclusion
Both sand casting and die casting hold esteemed positions in the metal casting industry. Their enduring presence is attributed to their respective ability to meet varied manufacturing demands efficiently and reliably. For industry professionals, understanding each method's nuances can optimize production strategies, ensuring quality and cost-effectiveness in metal component manufacturing. This informed approach reflects true expertise, gaining trust and authority in any competitive manufacturing landscape.