Sand and die casting are two foundational methods in modern manufacturing, each presenting unique advantages tailored to specific industrial needs. Sand casting, a longstanding technique, leverages the malleable nature of sand. This method involves creating a mold from sand, into which molten metal is poured, forming the desired shape once cooled. The use of sand casting is particularly beneficial for producing large and complex parts owing to its cost-effectiveness and scalability. On the other hand, die casting uses high-pressure to force molten metal into a mold cavity, delivering precise shapes with smooth surfaces.
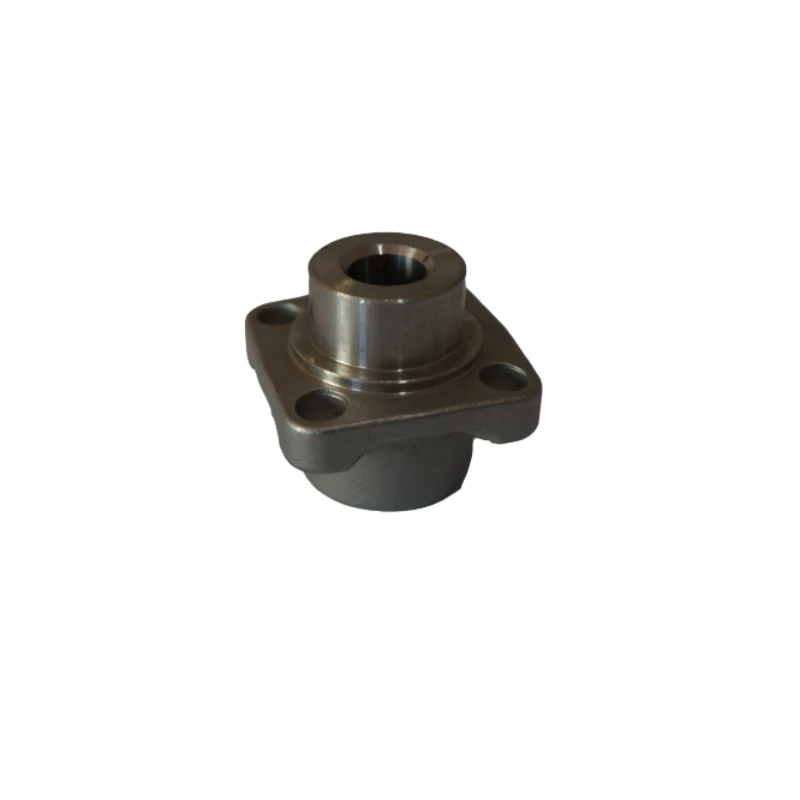
In terms of expertise, understanding the nuanced differences between these casting methods is crucial for manufacturers aiming to optimize production processes. Sand casting's expert appeal lies in its versatility; it allows for casting in a variety of metals including iron, bronze, and aluminum. Its ability to accommodate both low and high production runs makes it a go-to option for industries such as automotive and aerospace. Moreover, the technique's adaptability to produce intricate designs without the need for complex tooling underscores its long-standing application in historical metalwork and large-scale productions alike.
Comparatively,
die casting stands as a hallmark of precision and consistency. This process is synonymous with the high-speed production of non-ferrous metal parts—aluminum, magnesium, and zinc alloys are commonly used. Die casting is the preferred choice for creating components that demand tight tolerances and uniformity, which are critical in industries such as electronics, transportation, and consumer goods. Its ability to produce thousands of identical parts rapidly is unmatched, making it invaluable in mass production settings.
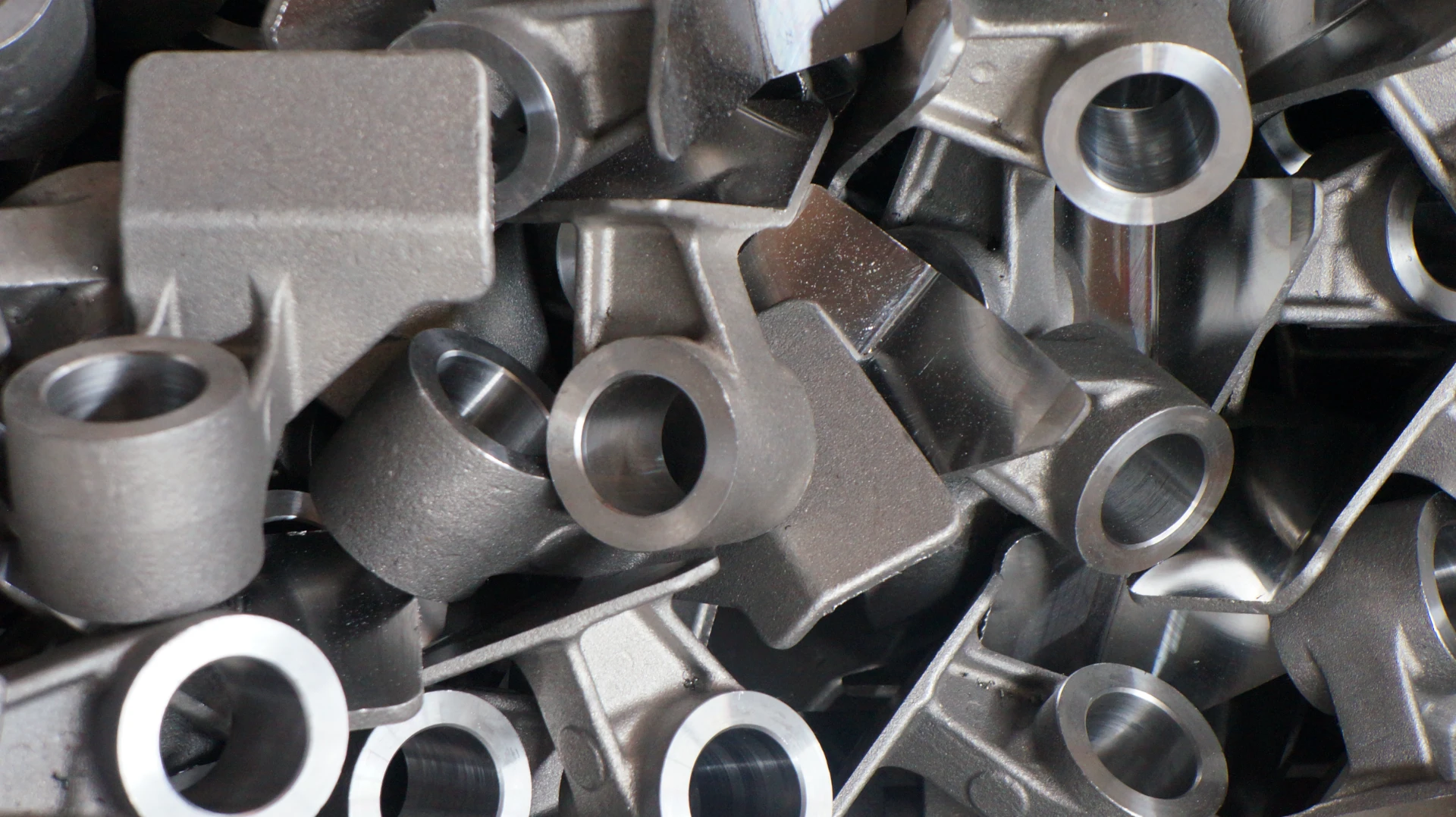
sand and die casting
Authoritativeness in these two domains has evolved, with manufacturers continually refining each method to align with technological advancements and sustainability goals. For instance, innovations in sand binding processes and sand reusability have enhanced the environmental profile of sand casting. Meanwhile, developments in die casting are marked by advancements in automation and the use of environmentally friendly lubricants and materials, reducing waste and energy consumption.
Trustworthiness of the casting methods hinges on their proven track records across centuries, with each boasting enduring reliability in their respective specialties. Choosing the appropriate casting method consequently depends not only on the material and production volume but also on the desired precision and finish. It's essential for manufacturers to assess these factors meticulously to ensure product integrity and optimize cost efficiency.
In conclusion, sand and die casting are indispensable in modern production landscapes, each with its distinct benefits. For companies aiming to leverage these methods, focusing on continuous learning and adopting the latest technological advancements is key. Such dedication not only enhances product quality but also fortifies their standing as trusted leaders in manufacturing, capable of meeting the ever-evolving demands of their industries. By understanding and employing the unique strengths of both sand and die casting, manufacturers can confidently produce high-quality components that meet stringent industry standards, ensuring sustained growth and excellence.