Precision lost wax casting, often referred to as investment casting, is a sophisticated process that melds artistry with science to produce intricate metal parts with unparalleled accuracy. This technique has been honed over centuries and stands as one of the most esteemed methods in the metalworking industry, especially prized for its ability to create components that meet stringent specifications with minimal machining.
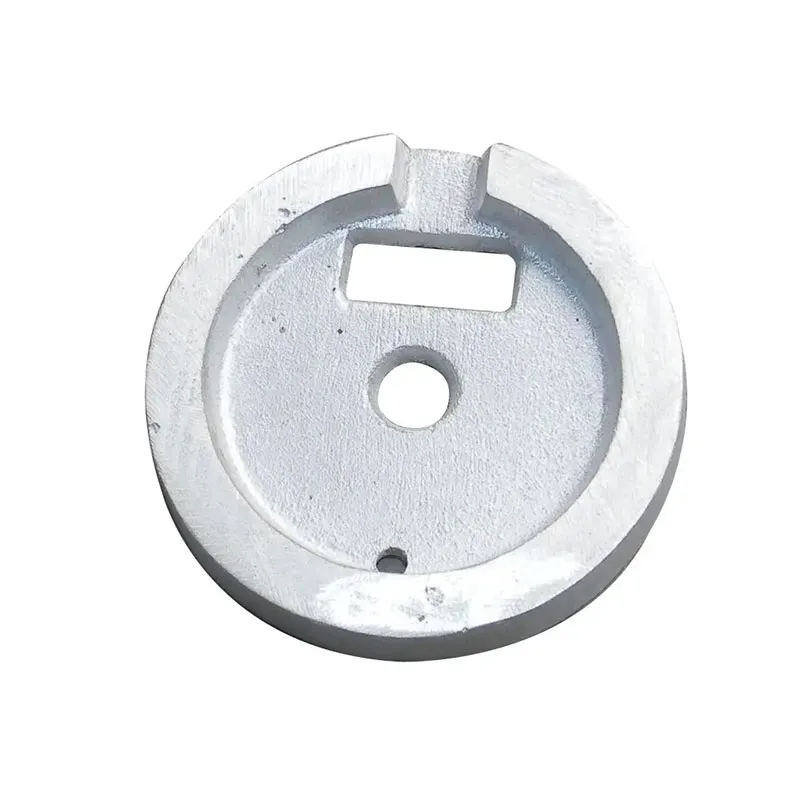
For industries that demand high precision, such as aerospace, automotive, and medical sectors, the role of precision lost wax casting factories is critical. These facilities are not mere production hubs; they are centers of innovation and expertise, shaping the future with every mold.
A key advantage of precision lost wax casting is its ability to replicate fine details. This capability is due to the casting process beginning with a wax model that captures every nuance of the desired part. Once coated with ceramic and heated, it leaves behind a perfect mold for molten metal. The expertise required to oversee this process demands a combination of technical acumen and artistic insight, ensuring that each casting is flawless.
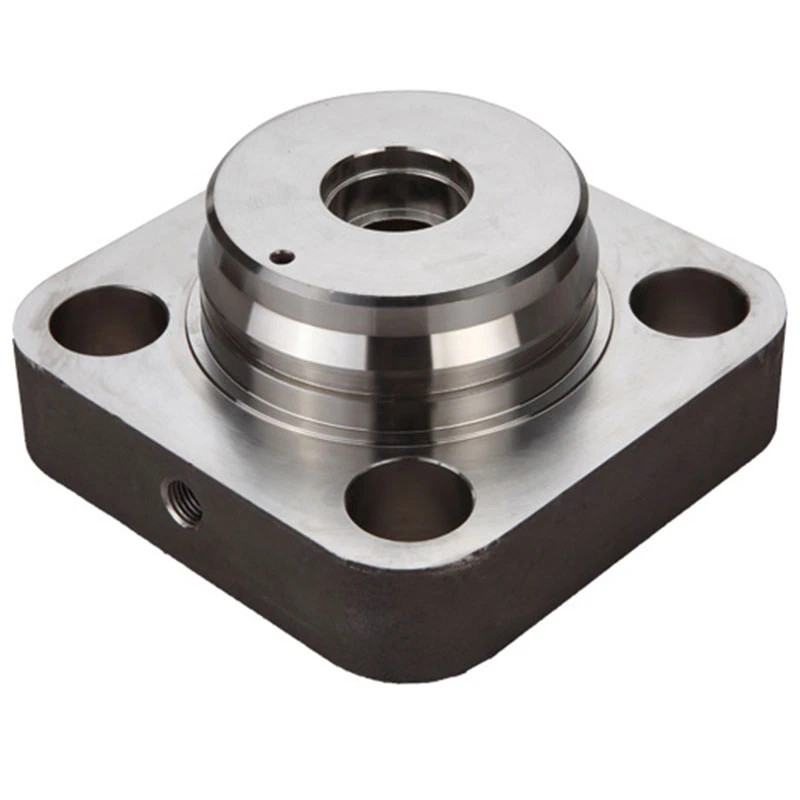
In terms of expertise, these factories are staffed by skilled engineers and craftspeople who understand the subtleties of both design and metallurgy. Their deep knowledge extends beyond mere production; they comprehend how diverse metals behave under various conditions and can adapt techniques to circumvent potential pitfalls such as shrinkage or defects. This knowledge is crucial when working with metals like titanium or stainless steel, which are favored for their strength and corrosion resistance but present casting challenges.
precision lost wax casting factories
The authority of precision lost wax casting factories comes from years of dedication to quality and innovation. Many of these facilities operate under strict quality control systems, adhering to international standards like ISO 9001, which ensures that every step of the casting process is subject to rigorous scrutiny. This authoritative approach underpins their ability to produce reliable components for safety-critical applications.
Trust is another cornerstone of these factories' operations. Clients worldwide hinge on these facilities to deliver parts that will endure under pressure, whether in the fuselage of an airplane or the engine of a high-performance vehicle. This trust is built through a transparent process where clients can often consult with engineers throughout development, ensuring that their specific needs are met with precision and care.
Moreover, the innovation within such factories continually pushes the boundaries of what's possible. Many are investing in advanced technologies such as 3D printing of wax models, which not only speeds up the process but also enhances the accuracy of complex geometries. This forward-thinking approach positions them as leaders in the industry, ready to tackle the most demanding projects.
To conclude, precision lost wax casting factories are pivotal in modern manufacturing, providing both expertise and innovative solutions that meet the rigorous demands of today's industries. Their commitment to quality, depth of knowledge, and ability to forge strong partnerships with clients cement their status as authoritative and trustworthy leaders in the field. As industries evolve and the demand for intricate, high-quality metal parts grows, these factories stand ready, as ever, to meet the challenge.