Plastic die casting has emerged as a pivotal process in modern manufacturing, offering unparalleled advantages for producing complex and lightweight components. Its growing popularity can be attributed to its ability to create high-quality products with precise specifications, making it a staple in industries ranging from automotive to consumer electronics. For businesses looking to stay competitive, understanding the nuances of plastic die casting and its applications is crucial.
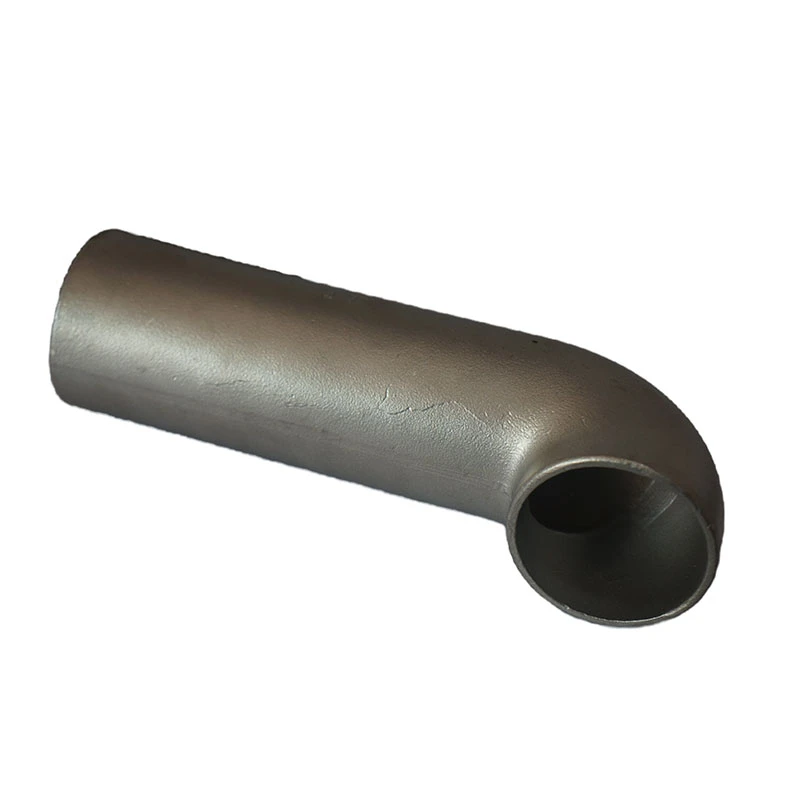
Unlike traditional metal die casting, plastic die casting uses thermoplastic polymers, which can be repeatedly melted and molded. This offers significant advantages, including reduced material waste and energy consumption. The recyclability of thermoplastics aligns with current sustainability trends, making plastic die casting an environmentally friendly choice. Companies investing in sustainable manufacturing processes can thus benefit from enhanced brand reputation and compliance with regulatory standards.
For instance, in the automotive industry, plastic die casting is utilized to manufacture lightweight yet durable components, such as dashboards and fuel systems. The reduction in vehicle weight leads directly to improved fuel efficiency and lower emissions, which are critical factors in automobile production and marketing. Similarly, in the consumer electronics sector, plastic die casting is essential for creating intricate and precise components, ensuring that devices are both functional and aesthetically pleasing.
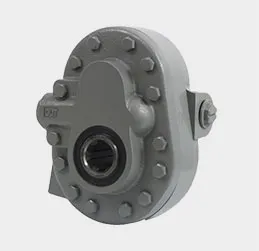
The expertise required for plastic die casting is substantial. It demands a thorough understanding of the mechanical properties of various thermoplastic polymers and their behavior during the cooling and solidification phases of the casting process. Professionals in the field must be adept in selecting the appropriate materials and designing molds that can withstand the thermal and mechanical stresses involved. This expertise ensures that the final products meet the stringent quality standards expected by modern consumers.
Authoritative industry players often collaborate with research institutions to advance plastic die casting technologies. These partnerships foster innovation, allowing for the development of new materials and processes that enhance product performance and reduce costs. Companies at the forefront of these developments are perceived as leaders in the field, which bolsters their market position.
plastic die casting
Trustworthiness in plastic die casting is fundamentally linked to consistency and quality control. Manufacturers must implement rigorous testing protocols to ensure that each batch of products meets design specifications and safety standards. This involves thorough inspections using advanced techniques such as computer-aided design (CAD) simulations and real-time monitoring of casting parameters. By prioritizing quality assurance, manufacturers not only comply with industry regulations but also build trust with consumers and clients.
Investing in advanced plastic die casting machinery enhances production capacity and product quality. Modern machines offer increased automation and precision, reducing human error and production times. This technological edge provides competitive advantages in responding to market demands swiftly and efficiently.
Moreover, as the demand for custom and small batch production grows, plastic die casting offers the flexibility needed to cater to specific client requirements without incurring significant additional costs. This ability to produce tailored solutions without sacrificing efficiency makes plastic die casting an attractive proposition for small and medium-sized enterprises seeking to differentiate their offerings.
In conclusion, plastic die casting stands as a testament to the advancements in manufacturing technologies. Its ability to produce environmentally sustainable, high-quality, and complex components efficiently positions it as a valuable process across multiple industries. Companies that harness the full potential of plastic die casting reap benefits through improved product performance, market leadership, and consumer trust. As the industry continues to innovate, those with the foresight to integrate these advancements into their operations will undoubtedly secure a formidable position in the future landscape of manufacturing.