Perfect die casting stands at the frontier of manufacturing technology, offering unparalleled precision and quality in metalwork. This method, which involves injecting molten metal into a mold under high pressure, is essential for producing complex and detailed metal parts with an exceptional finish. With decades of accumulated expertise, we shall delve into the unique aspects that make perfect die casting a critical component in numerous industries today.

At its core, die casting promises accuracy. Utilizing a mold crafted from intricate designs, this process ensures consistent results with every production cycle. Industries ranging from automotive to electronics rely heavily on perfect die casting for components that demand exact specifications. A seamless finish not only meets aesthetic values but also enhances the functionality of the products, exemplifying the pinnacle of manufacturing quality.
The mastermind behind every successful die casting operation is the engineer. These experts painstakingly develop the designs and blueprints that form the basis of the dies. Their profound understanding of metallurgy, combined with years of hands-on experience, makes the production of reliable components possible. It is a testament to their expertise that automotive safety features, intricate electronic casings, and state-of-the-art hardware components are developed to meet the high standards set by various industries.
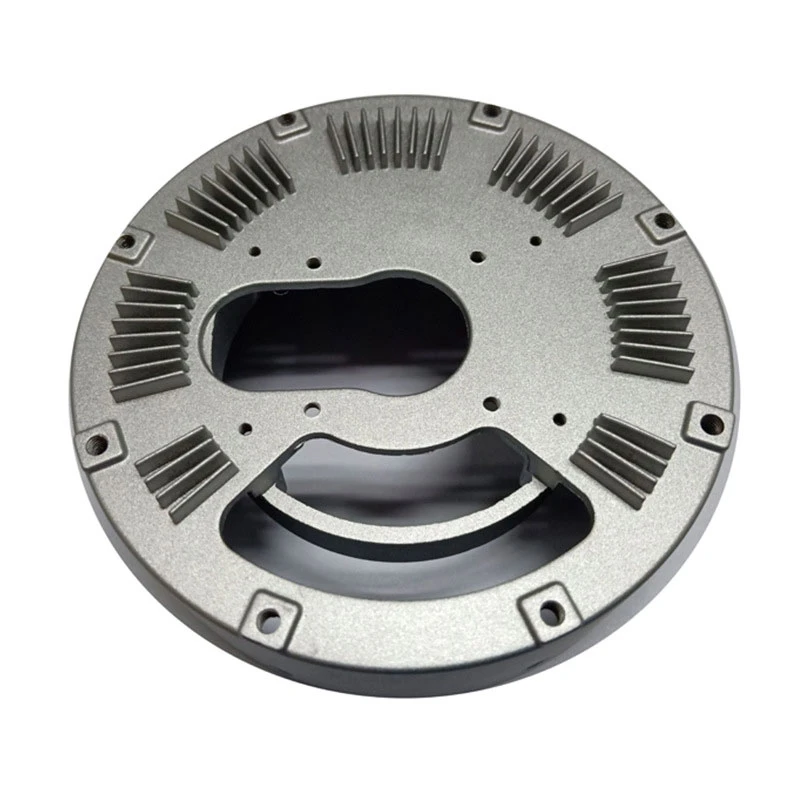
Material selection is another critical facet of die casting. The choice of metal, whether it’s aluminum, zinc, or magnesium, directly influences the quality of the final product. Each material has its unique properties aluminum is prized for its lightweight yet durable nature, while zinc offers excellent fluidity and thin-walled casting capabilities. Magnesium, on the other hand, is the lightest structural metal, used extensively in industries where weight is a crucial factor. Expert die casters are well-versed in selecting the right material to balance performance, cost, and manufacturing efficiencies.
perfect die casting
Perfect die casting doesn’t just stop at the production phase. It extends into post-casting processes that bolster the reliability and durability of the parts produced. Heat treatments, surface coatings, and thorough inspections all ensure that the product not only looks good but performs under demanding conditions. These steps are carried out with precision, employing advanced techniques and equipment to ensure the ultimate in quality assurance.
Trust forms the bedrock of perfect die casting. With high-pressure environments and the potential for rapid wear and tear, only well-established companies with a track record of impeccable service and product reliability stand at the forefront. These enterprises not only meet industry standards but often exceed them, setting the bar higher for competitors. Through transparent processes, stringent quality checks, and adherence to environmental norms, they foster an atmosphere of trustworthiness with their clientele.
Customers who choose die casting services are not just looking for a supplier; they are searching for a partner who comprehends their specific needs. Companies immersed in perfect die casting often forge strong relationships with their clients, tailoring services to fit particular requirements, and offering guidance and solutions to complex manufacturing challenges. Through expert consultations and bespoke production options, they reinforce the reputation of die casting as a service that transcends mere fabrication.
In conclusion, perfect die casting is not merely a function of machinery and materials, but a harmonious integration of experience, expertise, and trustworthiness. It represents the zenith of manufacturing excellence, serving as a testament to what can be achieved when cutting-edge technology meets time-honored craftsmanship. As industries continue to evolve, the demand for precision, quality, and reliability in metal casting is only set to rise—ushering in an era defined by the pinnacle of perfect die casting.