Creating green sand for casting involves a fascinating blend of art and science, offering a dynamic entry point into the casting industry for both amateur enthusiasts and seasoned professionals. The process combines the time-honored traditions of metal casting with modern advancements, providing thorough insights into metal work’s malleability and ingenuity.
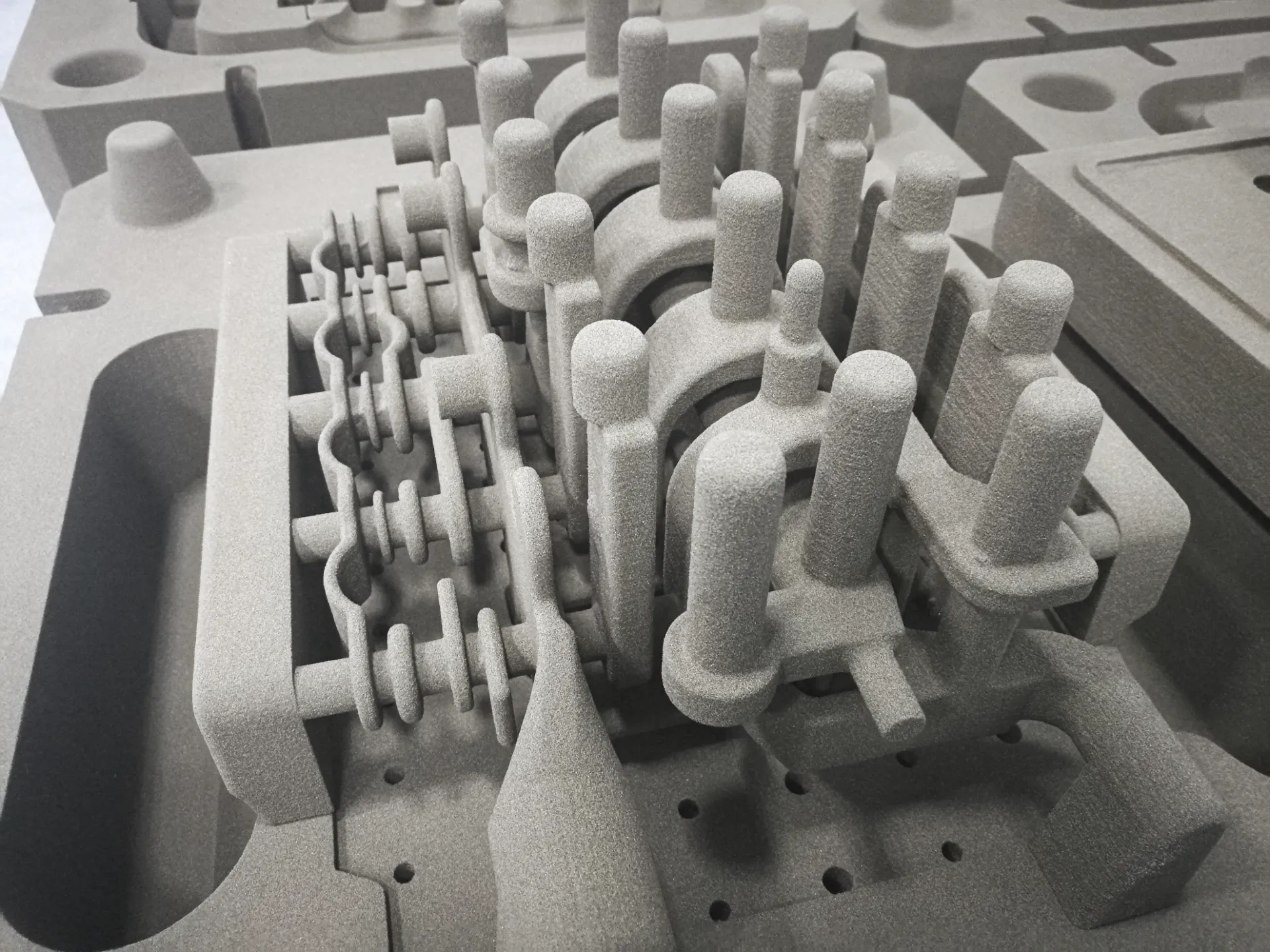
One of the most fundamental aspects of creating high-quality green sand is understanding its composition. Typically, green sand is composed of silica sand, clay, and water, mixed together to form a cohesive, moldable material. The silica sand provides the structural framework, ensuring thermal stability and strength. Bentonite clay, a type of refined clay, acts as the binder and gives the green sand its flexibility and adhesive properties. Water is the final component, facilitating the bonding by activating the clay to envelop the sand particles, further aiding in mold formation.
From a practical standpoint, the proportion of these components is critical. A common formula is 90% silica sand, 10% bentonite clay, and 4% water, although these proportions can be adjusted based on specific casting requirements and environmental conditions. Ensuring the proper mixture directly influences the green sand's effectiveness, impacting everything from surface finish to the integrity of the final cast.

Creating the perfect blend requires experience and finesse. Start by thoroughly mixing dry sand and bentonite clay until they are evenly distributed. This is best accomplished using a muller, which proficiently turns and mixes the components more effectively than hand mixing. Once the dry components are combined, gradually introduce water while continuously mixing to avoid clumping. The goal is to achieve a consistency resembling damp beach sand, where the mixture can hold its shape without excessive crumbling or becoming overly saturated.
A critical factor in making green sand, especially for professionals seeking authoritative quality, is the sand's green compression strength. This property ensures that the mold withstands the forces applied during the casting process. Ideally,
green sand should have a compression strength of approximately 1.5 to 3.5 PSI when appropriately mixed and compacted. Testing this involves compacting a sample into a cylindrical shape and determining the pressure at which it fails. This assessment ensures the green sand maintains shape and detail fidelity under the metallic weight and thermal stress.
making green sand for casting
After achieving the right consistency and strength, storing your green sand properly extends its usability and effectiveness. It should be kept in a covered container to prevent the loss of moisture and the penetration of contaminants, such as dust and debris. This step is crucial for maintaining its integrity over extended periods.
Safety is another significant consideration when making green sand. Always utilize protective gear, such as masks and gloves, to prevent inhalation of fine particles and protect skin from prolonged exposure to clay and sand. Working in a well-ventilated area further mitigates the risk of inhaling any airborne particles.
In terms of environmental sustainability—a vital factor in contemporary manufacturing—green sand casting is favorable as materials can be endlessly recycled. Used sand, after a casting process, can be rejuvenated by reconditioning with moisture and binders, reducing waste and lowering the environmental footprint of production facilities. This recycling aspect aligns green sand casting with growing global calls for sustainable industrial practices.
Anyone engaged in green sand casting should consider ongoing innovations and expert advice to remain at the forefront of the field. Consultations with industry professionals or participation in advanced workshops can provide insight into evolving methods and materials, helping practitioners refine their craft with authoritative and trusted techniques. Additionally, participating in well-renowned industry forums can foster a collaborative environment where emerging technologies and discoveries enhance both efficiency and craftsmanship.
By paying careful attention to the quality of materials, process, safety protocols, and advancements, individuals can produce superior green sand molds that contribute to high-quality castings—demonstrating both expertise and a commitment to the craft's enduring traditions.