Understanding the nuances between hot chamber die casting and cold chamber die casting is crucial for manufacturers deciding on the most efficient method for producing intricate metal components. These two approaches, while serving similar end goals, each come with unique attributes affecting everything from production speed to metal choice, influencing overall project efficiency.
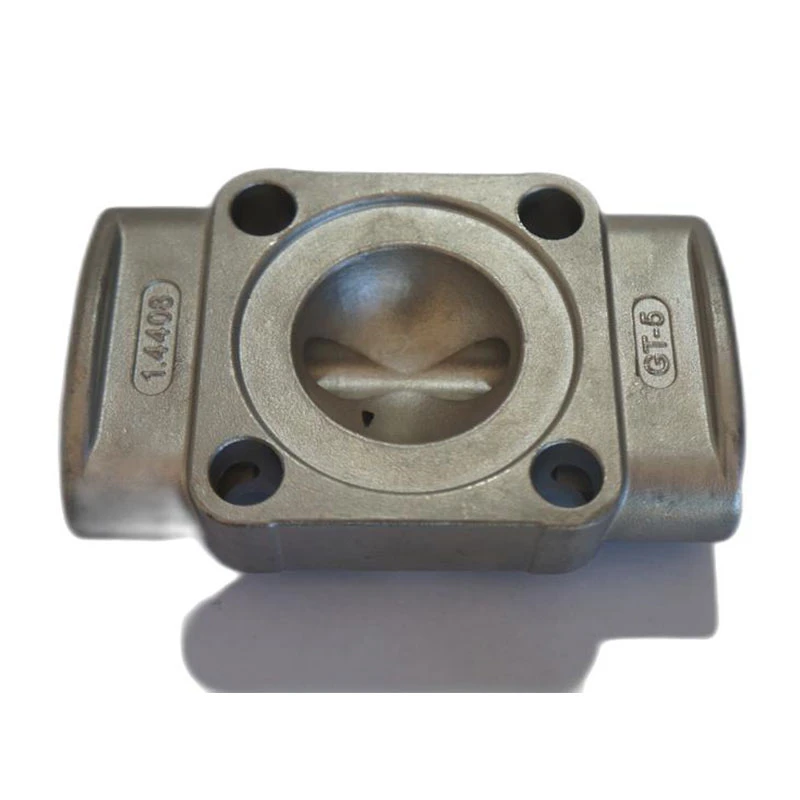
Hot chamber die casting, often favored for its rapid cycle times, is instrumental in producing high-volume runs of small to medium-sized parts primarily made from metals like zinc, lead, and tin. Its operational advantage lies in the configuration where the metal is melted within the casting machine itself. The simplicity and speed of directly injecting molten metal into the molds make it an excellent choice for metals with lower melting points that don't adhere aggressively to steel dies. This intrinsic advantage reduces downtime and increases production speed, enhancing manufacturing agility and throughput.
Despite the obvious benefits, hot chamber casting has its limitations. The primary constraint is the type of metals it can handle. High melting point materials like aluminum would degrade the chamber and plunger system used for injection in hot chamber machines, rendering it unsuitable for such applications. Furthermore, the simpler setup can sometimes limit the complexity of the achievable part geometries compared to cold chamber methods.
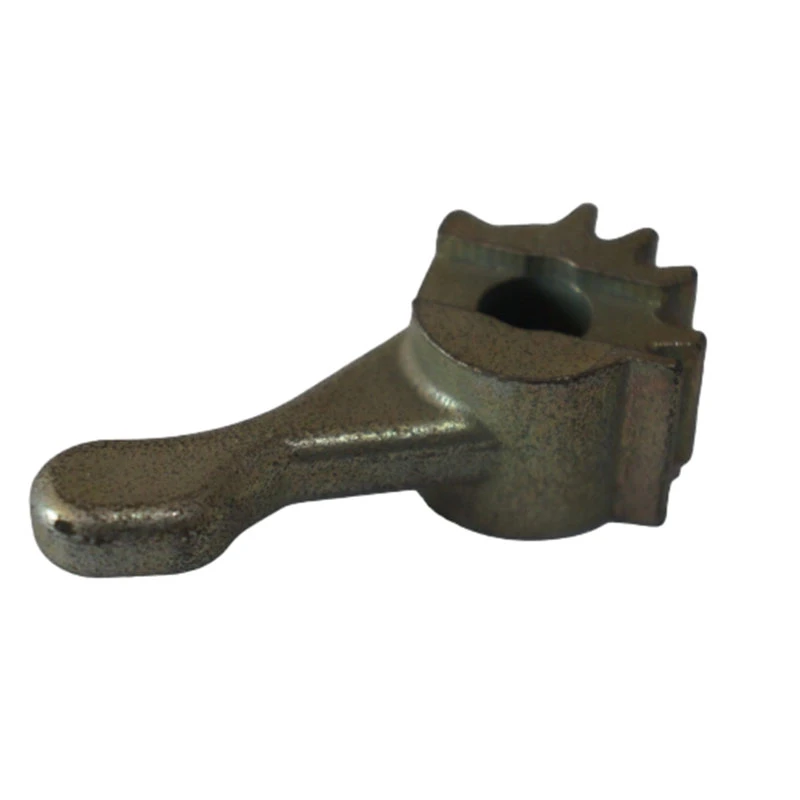
In contrast, cold chamber die casting is tailored for metals with higher melting points, such as aluminum and magnesium. In this process, the metal is liquefied in a separate furnace and transported to the casting machine, where it's then injected into the die. This separation of melting and casting operations minimizes the risk of excessive wear and tear on the casting equipment, enabling the use of more robust metals. Cold chamber machines are especially adept at producing large, complex parts that require high dimensional stability and strength.
hot chamber die casting and cold chamber die casting
The major drawback of cold chamber die casting is the longer cycle times. The additional steps of melting the metal in a separate furnace and transferring it to the injection system increases production time per part, reducing throughput compared to the hot chamber process. Moreover, the potential for heat loss during transfer can slightly impact the quality and consistency of the cast metal unless meticulously controlled.
Manufacturers often base their choice between these two processes on the specific materials required and the complexity of the parts being produced. The decision involves balancing cost, efficiency, and the technical demands of the finished product. For example, if speed and low material cost are the priority, and the parts can be made from lower melting point metals, hot chamber die casting stands out as more beneficial. Conversely, if the parts require the strength of high melting point metals and offer complex geometries, cold chamber die casting is often the preferred route despite potentially higher costs and longer production times.
The technological advancements in both hot and cold chamber processes aim to mitigate their respective limitations. Improved materials for dies and chambers, innovative thermal management systems to reduce heat loss, and automated systems for handling and transporting molten metals are continuously being developed to enhance efficiency, quality, and scope of application for each method. Moreover, computer-aided design (CAD) and computer-aided manufacturing (CAM) advancements allow for more precise mold and die creations, further blurring the lines between the capabilities and applications of these two methods.
In summary, the choice between hot chamber and cold chamber die casting should be meticulously pondered, taking into account material properties, part design intricacies, production volume expectations, and economic considerations. Gathering insights from industry experts, leveraging the latest technological advancements, and thoroughly analyzing production variables are essential strategies to ensure the selected method aligns seamlessly with the desired manufacturing outcomes. This nuanced understanding fosters not only efficient production cycles but also enhances the quality and integrity of the final components produced.