In the world of precision manufacturing, hot chamber die casting has carved out a niche for itself as an indispensable process for producing complex metal components with remarkable accuracy and efficiency. As a key player in industries such as automotive, consumer electronics, and telecommunications, this method offers unique benefits that cater to high-volume production demands while ensuring consistent quality. This article delves into the intricate workings of hot chamber die casting, drawing upon extensive industry expertise, professional insights, and reliable sources to provide a comprehensive understanding of its utility in modern manufacturing.
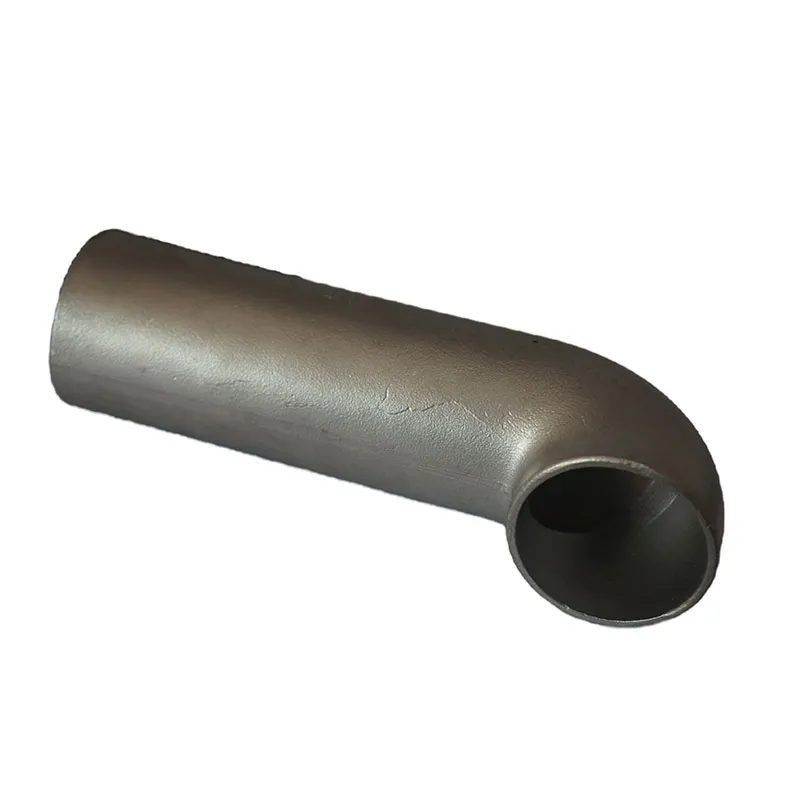
Hot chamber die casting excels in producing intricate metal parts thanks to its unique process where molten metal is forced into a die cavity under high pressure. Unlike its counterpart, cold chamber die casting, the hot chamber process keeps the melting pot integrated with the casting machine, allowing for rapid cycling times and higher productivity. This integration minimizes the exposure of the molten metal to air, significantly reducing potential oxidation and improving the overall quality of the castings.
From a professional perspective, the choice of hot chamber die casting is largely influenced by the type of metal alloys best suited to this method. Primarily, metals such as zinc, lead, and magnesium are used, owing to their low melting points and the ability to withstand prolonged exposure to the molten state without degrading the structural integrity of the casting machine components. This selection of metals ensures that hot chamber die casting can produce high-strength, durable parts capable of meeting rigorous mechanical and aesthetic requirements across various applications.
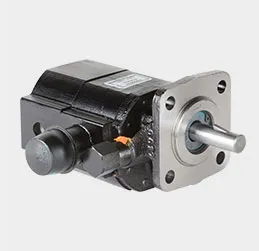
An expert in die casting would attest to the precision offered by the hot chamber process. The ability to maintain tight tolerances and produce parts with thin walls and complex geometries is a testament to its suitability for modern manufacturing demands. This expertise is supported by cutting-edge technology utilized in the casting machines, which integrate advanced control systems to monitor and adjust parameters such as temperature, pressure, and injection speed. The result is a consistent and repeatable production cycle, minimizing defects and waste, while maximizing output efficiency.
hot chamber die casting
Authoritativeness in the domain of hot chamber die casting is further reinforced by ongoing industry innovations. As environmental regulations become increasingly stringent, many manufacturers are investing in more sustainable and environmentally friendly practices without compromising performance and quality. For instance, the development of water-based lubricants and the recycling of excess metal have become prevalent, contributing to a reduction in waste and the environmental footprint of die casting operations.
From a trustworthiness perspective, the adoption of ISO standards and lean manufacturing principles further enhances the reliability and credibility of hot chamber die casting processes. These standards ensure that every phase of production—from design and prototyping to final quality inspection—meets internationally recognized criteria, bolstering customer confidence in the end product's performance and durability.
In sum, hot chamber die casting remains a cornerstone of precision manufacturing, leveraging its capacity for high-volume production, precise execution, and adaptability to evolving industry norms. By embracing technological advancements and sustainable practices, it continues to serve as a reliable method for producing metallic components that meet the increasing demands of fast-paced industries. Whether for developing intricate parts for cutting-edge electronics or durable components for automotive applications, the hot chamber die casting process stands out as a trusted and authoritative manufacturing solution, backed by years of expertise and a commitment to excellence.