In the competitive realm of high-precision manufacturing, pressure die casting is a method widely utilized to fabricate intricate and lightweight metal parts. One critical aspect of this process is determining the appropriate tonnage required for the die-casting machine. An accurate calculation ensures not only the quality of the end product but also optimizes production efficiency and cost-effectiveness.
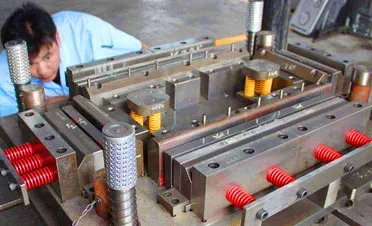
Pressure die casting involves injecting molten metal into a die cavity under high pressure, which can be as much as several thousand pounds per square inch. The tonnage required for a die-casting operation is directly related to the clamping force necessary to hold the mold halves together during this high-pressure injection. If the clamping force is inadequate, defects such as flash or incomplete casting may occur. Conversely, excessive tonnage could lead to unnecessary energy consumption and wear on the machinery, reducing equipment lifespan.
Experience in Tonnage Calculation
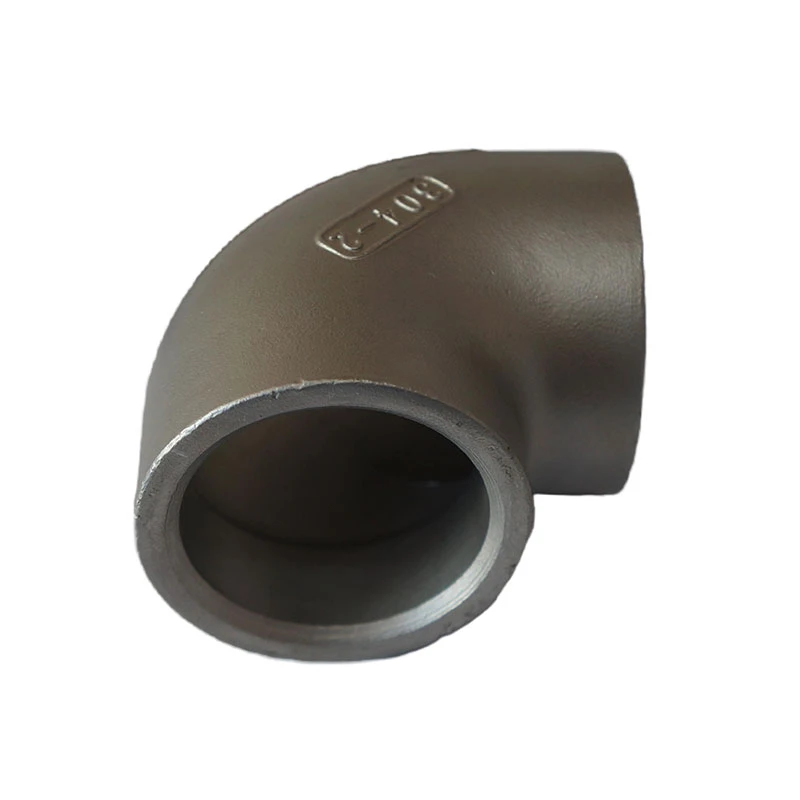
From extensive industry experience, the tonnage required for a pressure die casting machine is primarily influenced by three variables the projected area of the casting, the type of alloy used, and the complexity of the part. Experienced technicians often begin with calculating the projected area, which is simply the largest cross-sectional surface area of the component being cast. This figure determines the basic clamping force required for the operation.
Each type of alloy—with its unique density and flow characteristics—demands specific considerations. For instance, aluminum alloys, being lightweight, demand less tonnage compared to denser metals like zinc. The complexity and intricacy of the part also affect the tonnage calculations; more intricate parts with delicate features require careful pressure distribution to ensure complete cavity filling without defects.
Expertise in Applying Formulas
The industry-standard formula to compute the necessary tonnage involves calculating the product of the total projected area of the casting and the cavity pressure specific to the alloy used. For instance, aluminum might require approximately 6,000 psi of pressure. The formula appears as follows
pressure die casting tonnage calculation
Tonnage = Projected Area (in square inches) x Cavity Pressure (psi) / 2000
This formula provides a baseline, ensuring that a sufficient clamping force is established to prevent mold separation during metal injection. However, it is critical to couple this calculated value with empirical knowledge and practical adjustments based on the specific properties of the casting task at hand.
Authority on Regulatory and Safety Standards
As experts in the field, it’s imperative to adhere to regulatory safety and operational standards. Casting professionals must align with standards set by organizations such as the North American Die Casting Association (NADCA) and the International Organization for Standardization (ISO). These standards not only advocate for safety but also provide guidelines for quality control and machine efficiency that can influence tonnage calculations and overall machine settings.
Trustworthiness through Adoption of Best Practices
To enhance trustworthiness and consistency in pressure die casting operations, adopting best practices is essential. Regularly calibrated equipment, continuous operator training, and a comprehensive understanding of metallurgical properties reinforce the reliability of tonnage calculations. Utilizing advanced simulation software for die design also aids in predicting potential errors and optimizing the tonnage needed for different production scenarios before physical trials, reducing material wastage and improving resource allocation.
In conclusion,
the calculation of pressure die casting tonnage is integral to efficient manufacturing operations. By leveraging real-world experience, applying scientific formulas with expertise, adhering to authoritative standards, and employing best practices, manufacturers can assure that their operations are not only cost-effective and efficient but also produce high-quality, defect-free components.