Green sand casting and dry sand casting stand as two predominant methods in the world of metal casting, each offering unique advantages tailored to different manufacturing needs. A deep dive into these processes unveils insights critical for engineers, production managers, and decision-makers in choosing the best approach for their specific applications.
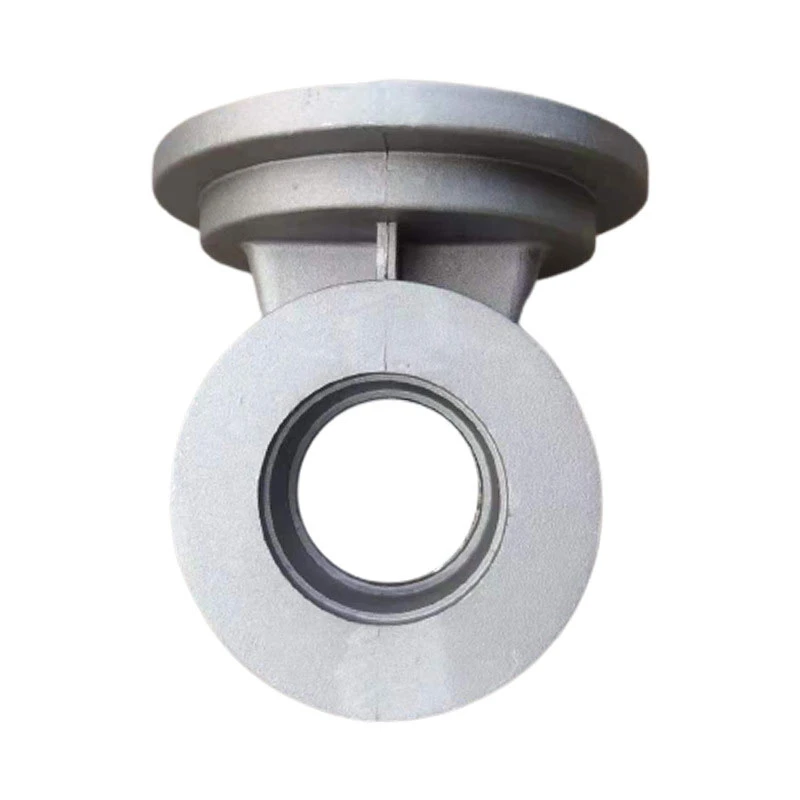
Green sand casting derives its name not from the color of the sand, but from the presence of moisture in the mixture of sand, clay, and water. This method's hallmark is its flexibility and efficiency, especially in producing intricate geometries. The moist sand acts as a reliable binder, creating molds that deliver excellent surface finishes. One notable benefit is its reusability—after casting, the sand can be recycled for future molds, making it an environmentally sustainable choice. The moisture in green sand provides excellent thermal conductivity, essential for casting ferrous materials, such as iron and steel. However, the presence of moisture can also lead to potential steam-related casting defects, necessitating careful process controls and experience-driven adjustments.
Conversely,
dry sand casting involves using chemically-bound sand without moisture. The absence of moisture means the potential for certain defects, such as gas porosity, is significantly reduced. This makes dry sand casting particularly advantageous for non-ferrous metals, such as aluminum and copper alloys. The method is celebrated for producing dimensionally precise components, crucial in industries where tight tolerances are non-negotiable. Additionally, dry sand molds are typically stronger, allowing for the casting of larger parts without compromising structural integrity. The higher initial setup costs and process times are often outweighed by the high-quality outcomes and consistent repeatability of the molds.
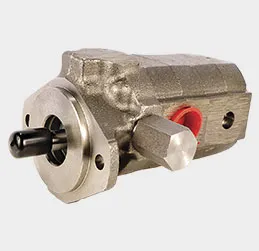
From a product standpoint, the choice between these methods can profoundly affect manufacturing efficiency, cost, and ultimately, the end product's quality. Companies operating in high-volume production cycles often gravitate towards green sand casting due to its economical scalability. Meanwhile, industries requiring precision and superior surface finishes, such as aerospace and automotive sectors, might find dry sand casting more fitting despite the higher initial costs.
green sand vs dry sand casting
Innovation within these casting realms continues to advance, with ongoing research focused on enhancing the properties of mold materials and improving the quality control processes. Developments in automation and real-time monitoring are minimizing human error, making both green and dry sand casting more reliable and efficient than ever before.
Professionals exploring the implementation of either method should consider the nuances of their specific application needs, including material type, production volume, and desired consistency. It is advisable to conduct pilot runs with both casting methods, using the same design specifications, to evaluate the suitability based on dimensional accuracy, surface finish, and mechanical properties of the cast products.
In conclusion, while both green and dry sand casting offer unique benefits and challenges, the strategic selection based on empirical data and industry requirements can lead to significant competitive advantages. Expertise in these processes not only optimizes production efficiencies but also enhances product quality, ensuring a robust response to evolving market demands.