Die casting is a highly efficient manufacturing process used to produce complex metal parts with exceptional precision and consistency. This technique is particularly prevalent in the automotive, aerospace, and consumer electronics industries due to its ability to create durable, high-quality components with tight tolerances. By forcing molten metal under high pressure into a mold cavity, die casting allows for the creation of parts with intricate geometries that would be challenging or impossible to produce with other manufacturing methods.
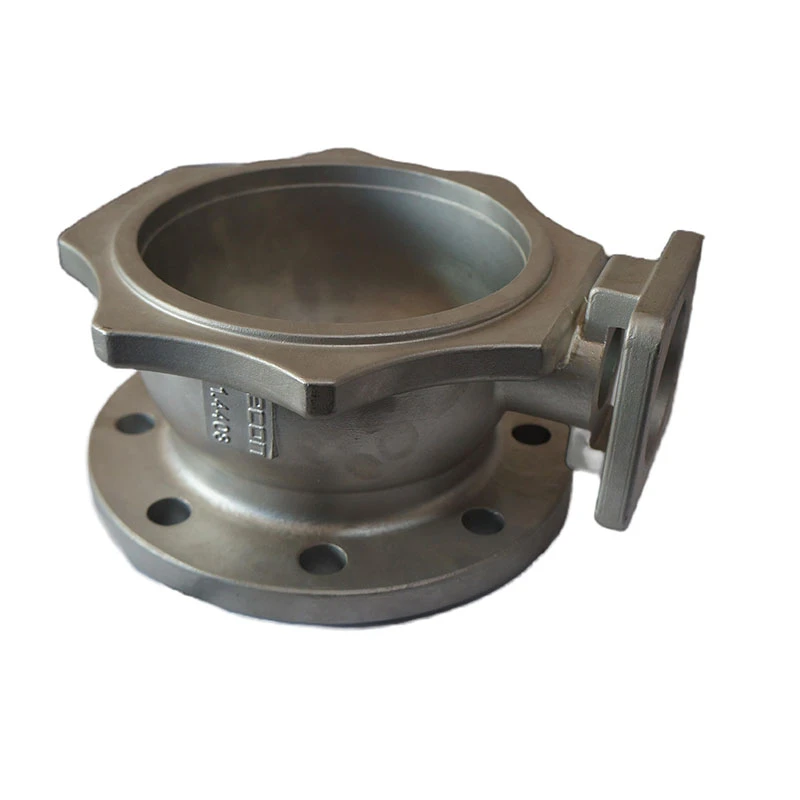
From an expert perspective, die casting offers numerous benefits for product manufacturers. The process is known for its speed and efficiency, producing large volumes of uniform components with minimal waste. This is especially critical in industries where material costs can significantly impact profitability. Moreover, die-cast parts are often ready for use with minimal machining, as the accuracy of the molds ensures each piece meets strict design specifications.
Die casting processes can be divided into two main types hot chamber and cold chamber. Hot chamber die casting is typically used for metals with lower melting points, such as zinc, magnesium, and lead alloys. This method is advantageous because it allows for quicker cycling times and reduced thermal strain on the equipment. Conversely,
cold chamber die casting is used for metals like aluminum, which have higher melting points. The cold chamber process involves manually transferring the molten metal into a separate injection chamber, which can slightly slow down production but is necessary to handle high-temperature materials.

Real-world experience underscores the importance of quality control and precision in die casting. Successful die casting operations often rely on advanced simulation software to model the flow of molten metal and anticipate potential defects. This preemptive approach minimizes casting defects such as porosity, flash, and dimensional inaccuracies. Continuous monitoring and adjustments during production further ensure that each part meets rigorous quality standards.
die casting explanation
In terms of expertise, designing die-casting molds demands a deep understanding of material properties and the casting process. Engineers must take into account factors like mold release mechanisms, draft angles, and thermal expansion. Optimal mold design not only enhances the quality of the cast parts but also extends the lifespan of the molds, reducing costs over the product's lifecycle.
Authoritativeness in the die casting domain often involves adherence to industry standards and certifications. Many manufacturers strive to comply with ISO and ASTM standards, which govern material properties, testing methods, and quality management systems. These standards provide customers with assurance that the die casting process is conducted under strict quality controls, leading to reliable and consistent products.
Finally, trustworthiness is built through transparent communication and collaboration with clients. Manufacturers who openly discuss the capabilities and limitations of the die casting process help clients make informed decisions. This transparency, coupled with a track record of delivering high-quality components on time and within budget, fosters long-term partnerships.
In summary, die casting is a cornerstone technology for producing precision metal parts across various industries. Its successful utilization depends on a combination of technical expertise, strategic planning, and stringent quality control. As industries continue to evolve, die-casting will likely remain a pivotal process, adapting to new materials and innovative designs to meet the demands of modern manufacturing.