Die casting is a pivotal manufacturing process renowned for its ability to produce complex metal parts with high precision and repeatability.
In the realm of die casting, two principal methodologies often surface A and B die casting. Each brings a unique set of attributes to the table, serving distinct purposes and meeting specific industrial requirements.
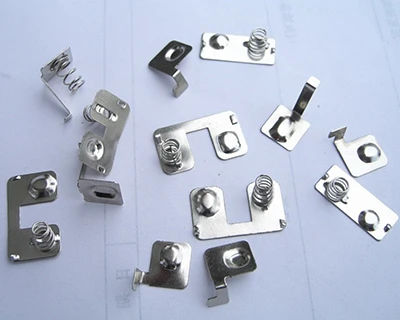
A die casting, often referred to within industry circles with specific proprietary methods, emphasizes high-pressure injection techniques. This method is celebrated for its ability to produce parts with exceptional detail and surface finish. A benefit of A die casting is its remarkable efficiency in producing large volumes of consistent parts swiftly. This quality is particularly advantageous for industries like automotive and aerospace, where precision and uniformity are paramount. A point of concern with A die casting, however, can be its upfront tooling cost, which might not be feasible for small-scale productions.
On the other side, B die casting introduces a different approach that prioritizes versatility and adaptability in the casting process. This method generally employs lower pressures and sometimes gravity-fed systems, making it suitable for larger and thicker-walled components. B die casting shines in its ability to accommodate a variety of metal alloys, giving manufacturers a broader selection of material options to tailor mechanical properties and suit diverse applications. It's often the go-to for producing machinery parts and components that need to withstand significant wear and tear.
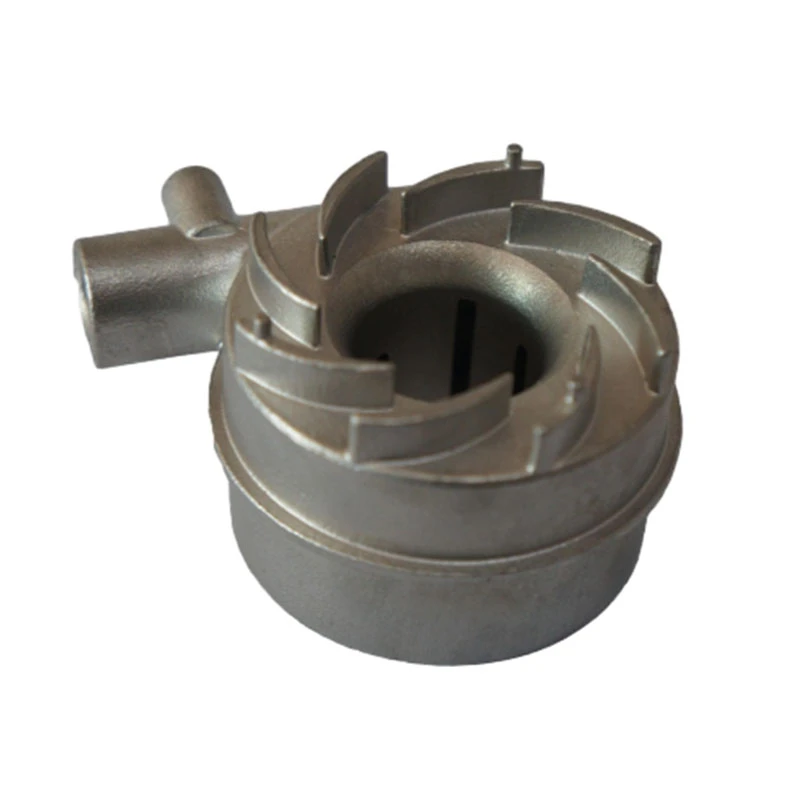
Professionals who excel in die casting processes understand the criticality of choosing the right method and material. For instance, the automotive sector frequently employs aluminum A die casting for engine blocks and transmission cases, exploiting its lightweight and superior strength. Meanwhile, industries requiring robustness and durability, like construction equipment manufacturing, may lean towards B die casting with zinc or magnesium alloys.
a and b die casting
Authoritative experts recommend that manufacturers conduct a comprehensive analysis of the product requirements, including dimensional tolerances, expected lifecycle, and exposure conditions, before selecting A or B die casting. This analysis not only influences material selection but also dictates the engineering of the die itself. As technology advances, integrating simulation tools into the design phase has become increasingly crucial. These simulations help predict fluidity, fill patterns, and cooling times, ensuring that the final product meets design specs without costly trial and error.
Trust in the die casting industry is further solidified by adhering to rigorous quality standards. Both A and B die casting processes benefit when manufacturers implement quality checks throughout the production cycle. Certification through ISO standards, alongside adherence to industry best practices, enhances credibility and assures clients of a product’s reliability.
In conclusion, both A and B die casting possess distinct advantages tailored for specific industrial applications. The choice between the two should be strategically aligned with the product’s technical specifications and financial considerations. As technology continues to evolve, so too do the opportunities for innovation within die casting, promising exciting advancements in material science and process optimization. This evolution underscores the importance of leveraging expert knowledge and technical prowess, ultimately paving the way for manufacturing excellence and consumer trust in die-cast products.