Precision casting, often referred to as investment casting, is a manufacturing process that has revolutionized the way intricate metal components are produced. This method is renowned for its ability to create products that require intricate details and exceptional dimensional accuracy. Drawing from years of industry experience and expertise, I'll walk you through the essential aspects of precision casting, highlighting its importance and application in various sectors, underscoring its authority and trustworthiness in the manufacturing world.
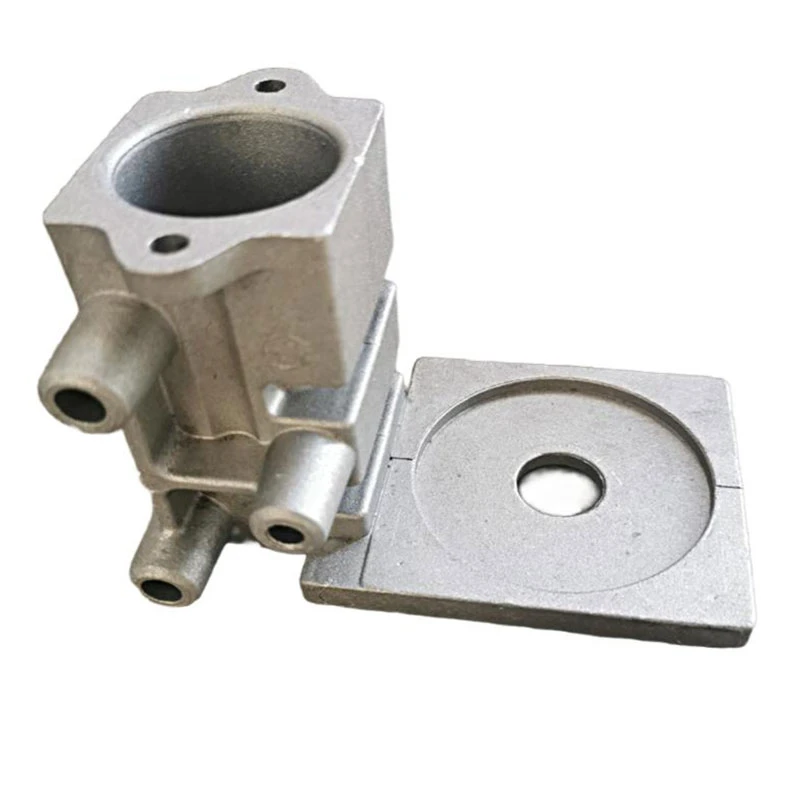
Precision casting, distinguished by its use of high-quality materials and innovative processes, is widely trusted across industries such as aerospace, medical, automotive, and more. This process begins with the creation of a wax model, which is an exact replica of the final metal part.
This wax model is then encased in a ceramic shell to form a mold. Once the ceramic hardens, the wax is melted away, leaving behind a hollow cavity. Molten metal is then poured into this mold to form the final component. The capability of precision casting to produce components with micro-level details makes it the process of choice for projects where precision and quality cannot be compromised.
Experience gleaned from long-term practice has shown that one of the key benefits of precision casting is its ability to eliminate the need for additional machining. When implemented correctly, the parts come out of the mold already in their final form, requiring little to no additional processing. This not only speeds up production but also significantly reduces costs. The consistency and repeatability of this process make it exceptionally reliable, and its versatility supports the easy adaptation of materials and design requirements.
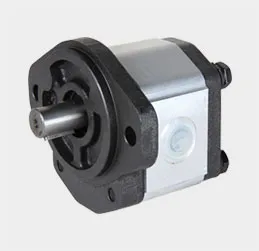
Expertise in precision casting is demonstrated through the precise control of the casting variables such as temperature, mold composition, and cooling rate. Successful execution relies heavily on advanced technology and a profound understanding of metal properties and behaviors. Professional foundries employ engineers who dedicate considerable time to researching and refining methods to optimize the casting processes. Their continuous advancements contribute heavily to the authority and credibility of precision casting as a leading manufacturing solution.
what is precision casting
Furthermore, the authoritative standing of precision casting is evidenced by its strict adherence to industry standards and certifications. The process is governed by rigorous quality controls to ensure each cast meets the high standards required in demanding environments. Alloys used are often documented to secure traceability from raw material through to the finished product, thereby ensuring trustworthiness in terms of performance, durability, and reliability.
A trustworthiness hallmark of precision casting is its ability to reproduce the most complex geometries while maintaining the integrity and strength of the material. Industries trust this method for its capability to deliver high-performance components consistently. Customers can depend on precision-cast items with the assurance that these parts have passed numerous quality assurance tests, confirming they meet the necessary safety and efficacy standards.
In terms of product applications, precision casting is utilized to develop a broad array of items including turbine blades, medical instruments, and complex mechanical assemblies. These are precision-designed to function under extreme conditions and strict specifications, highlighting the adaptability of precision casting to meet diverse industry needs.
In conclusion, precision casting stands out as an indispensable tool in modern manufacturing, characterized by superior expertise, professional practice, authoritative command of processes, and an assured trust in product reliability. Its capacity to meet the critical demands of high-quality and precise components while offering cost-effective solutions solidifies its place in today’s globally competitive market. As we continue to look for ways to enhance production and innovative potential, the already crucial role of precision casting will undoubtedly expand, offering further value to an ever-evolving industry landscape.