In the world of manufacturing, the choice of stamping parts material plays a critical role in determining the quality and success of the final product. Selecting the right material for stamping is not merely a technical decision but a strategic one that can impact the entire lifecycle of a product from design to production, and eventually, its market performance. The landscape of stamping materials is vast and includes several options, each with its unique properties and applications.
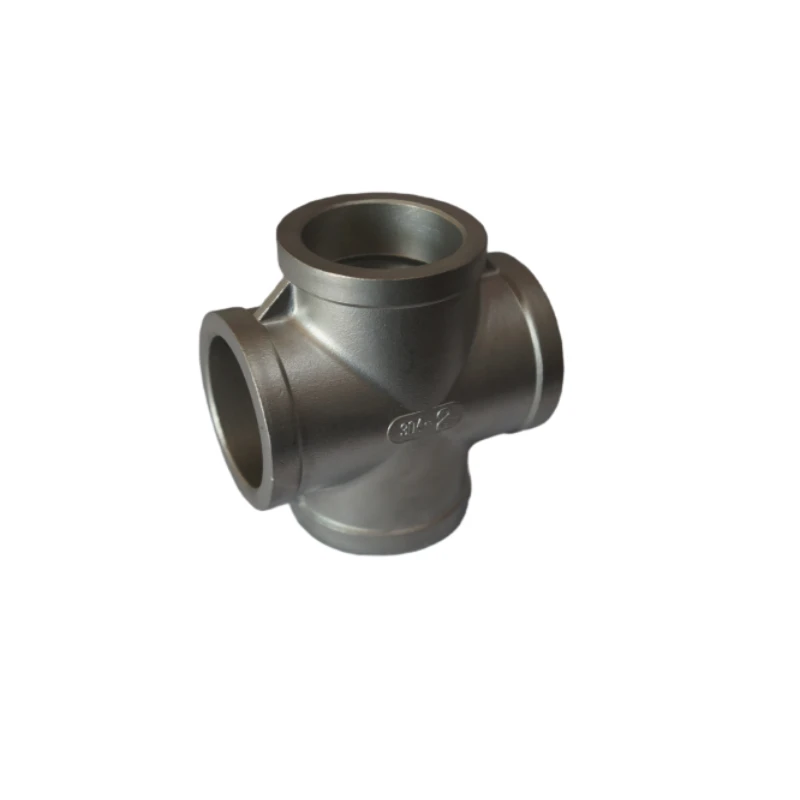
Materials used in stamping range from common metals to advanced alloys, each offering distinct characteristics that can be leveraged to meet specific requirements. Steel, for example, remains the most popular choice for many industries due to its excellent strength, durability, and affordability. In particular, cold-rolled steel is frequently used because it provides a smooth finish and precise dimensions, which are crucial for parts that demand high accuracy.
Aluminum is another widely favored material in the stamping industry. Its lightweight nature makes it ideal for applications in the automotive and aerospace sectors where reducing weight without compromising strength is essential. Aluminum also offers excellent corrosion resistance, which extends the lifespan of parts and reduces maintenance costs. The flexibility of aluminum allows it to be formed into complex shapes, making it suitable for a variety of intricate designs.
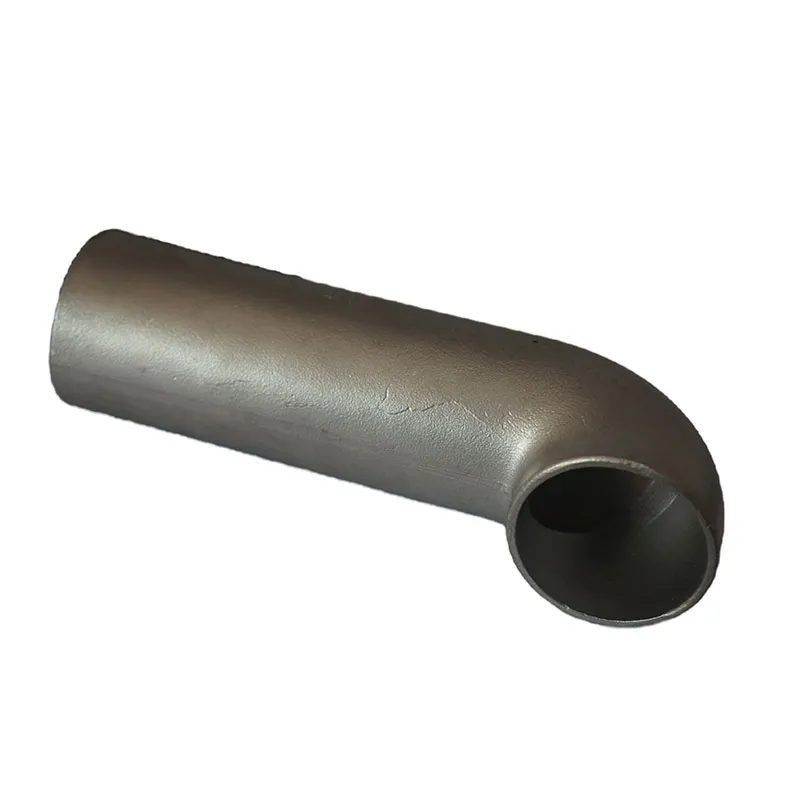
On the cutting edge of material technology are advanced alloys, including stainless steel and high-strength, low-alloy (HSLA) steels. These materials provide superior corrosion resistance and mechanical properties, which are vital in environments exposed to harsh conditions. Stainless steel, in particular, is prized for its aesthetic appeal and ability to withstand extreme temperatures, while HSLA steels offer increased strength and toughness without adding significant weight.
In the electronics industry, copper and brass are commonly used in stamping parts due to their high electrical conductivity and excellent thermal performance. These materials enable the production of components that require efficient electrical pathways, such as connectors and terminals, which are crucial in ensuring the reliability of electronic devices.
stamping parts material
Material selection also involves considering environmental and sustainability factors. The demand for eco-friendly materials has led to innovations in stamping processes and materials that align with green manufacturing principles. Recyclable materials like aluminum can be reprocessed and reused, reducing the overall environmental impact. Manufacturers are increasingly gravitating towards sustainable materials that not only meet performance criteria but also contribute to a reduced carbon footprint.
The success of stamping parts material selection relies heavily on industry experience and expertise. Manufacturers with a deep understanding of material properties, coupled with practical experience, can provide invaluable insights into optimizing designs for specific applications. This expertise ensures that the selected material not only fits the functional requirements but also enhances the manufacturability and economic feasibility of the product.
Achieving authoritativeness in material selection necessitates continuous research and development. Staying abreast of the latest advancements in material science ensures that manufacturers can leverage cutting-edge options to gain a competitive advantage. Additionally, partnerships with reputable material suppliers can bolster a company's authority, offering access to premium materials and technical support.
Trustworthiness in material selection derives from transparent processes and quality assurance measures. Manufacturers must adhere to stringent standards and testing protocols to verify that materials meet specified criteria. This involves rigorous quality control at each stage of production to ensure consistency and reliability, which in turn builds trust with consumers and stakeholders.
In conclusion, the selection of stamping parts material is a multifaceted decision that intertwines experience, expertise, authoritativeness, and trustworthiness. By striking a balance between these elements, manufacturers can not only produce superior quality components but also forge a path towards innovation and sustainability in the manufacturing industry. As material science continues to evolve, those who adeptly navigate these complexities will set themselves apart in the competitive landscape of stamping parts.