Sand casting stands as a revered manufacturing process, intricately tied to the art and science of shaping metal components. At its core, sand casting uses a silica-based sand mixture to create a mold, which then shapes the molten metal poured into it. The sand used for the molding possesses distinct qualities essential for the success of the process. This article explores the significance of sand in sand casting, its selection, preparation, and its vital characteristics that ensure superior casting outcomes.
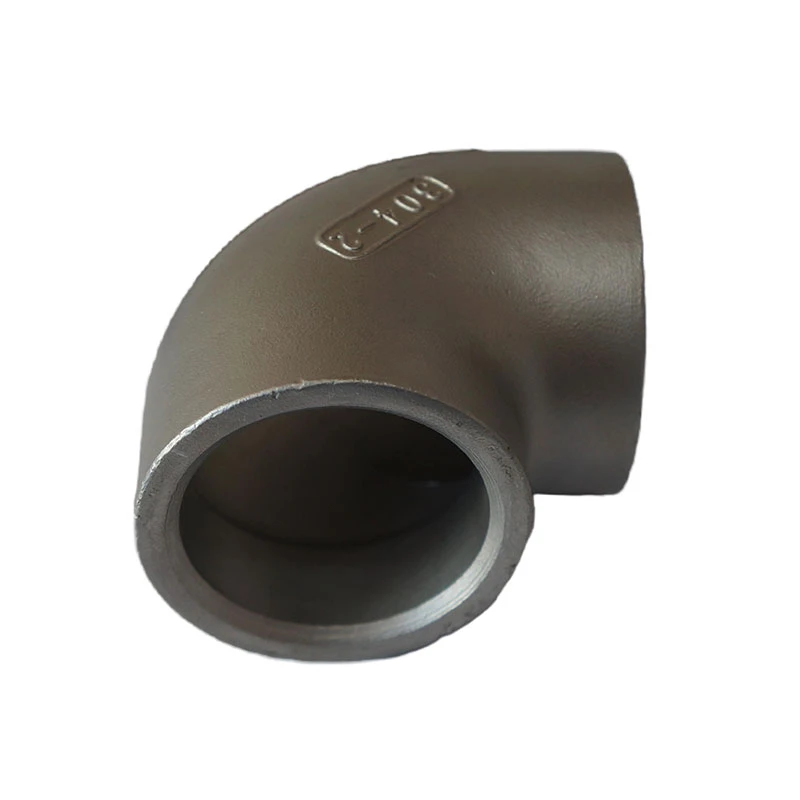
Selecting the right sand is the cornerstone of any successful sand casting endeavor. Primarily, the sand's grain size, shape, and composition determine its suitability. Fine-grained sand is essential for capturing intricate details, whereas coarser grained sand gives permeability, reducing the chances of gas defects. Round-shaped grains are preferred as they provide better flowability and pack tightly, enhancing the mold strength, which is crucial when handling high temperatures and pressure from molten metals.
The composition of the sand also plays a critical role in ensuring the quality of the final product. Traditionally, silica sand is prevalently used; however, synthetic alternatives are gaining popularity. Silica sand, resistant to high temperatures and chemically inert, provides a reliable base for casting molds. Additionally, specialty sands, such as zircon and olivine sands, offer specific benefits like improved refractoriness and lower thermal expansion, which are essential in precise casting processes like aerospace and automotive applications.

Furthermore, the binding agents mixed with sand are indispensable for maintaining mold integrity. Clay (usually bentonite) is the standard binder, which, when mixed with water, imparts the necessary plasticity and strength to the sand mold. Organic and inorganic binders are also employed to suit specific casting requirements. For instance, resin-based binders are often used in complex core molds to provide superior surface finishes and dimensional accuracy.
Preparing the sand mixture for casting demands meticulous attention to detail to attain optimal performance. Moisture content is a critical factor; excessive moisture can lead to steam formation, causing defects, while insufficient moisture compromises the mold's cohesiveness. Thus, achieving the right balance is essential. The compacting process, where the sand is packed into the mold frame, must be uniform to avoid weak points that might fail under the strain of molten metal.
sand used for sand casting
One cannot overlook the importance of sand reclamation and reuse in sand casting. As the process consumes a significant quantity of sand, economic and environmental considerations push for the recycling of used sand. Technologies for thermal reclamation and mechanical attrition reclaim significant volumes of sand, drastically reducing costs and environmental impact. Reclaimed sand, when properly treated, can match the performance of fresh sand, ensuring sustainable production cycles.
Quality control measures for sand ascertain the desired attributes for successful molds. Regular testing for grain size distribution, permeability, and compressive strength are standard practices in foundries. Advanced methodologies, such as X-ray fluorescence (XRF) analysis, are employed to confirm the chemical composition of sand and binders, ensuring they meet the stringent requirements of industry standards.
Lastly,
innovation continues to redefine the realm of sand casting. Developments in 3D printed sand molds and cores have revolutionized the industry by cutting lead times and enhancing the complexity of casts achievable. The precision of these techniques lowers the requirement for machining after casting, fostering efficient production cycles.
In summary, the sand used in sand casting is not merely a passive medium but an active facilitator of the entire casting process. Its selection, preparation, and treatment impact the quality, efficiency, and sustainability of the final product. By understanding and harnessing the unique attributes of sand, manufacturers can push the boundaries of what’s possible in metal casting, achieving new feats of engineering and design excellence.