Sand casting, a staple in manufacturing for centuries, continues to be a cornerstone of modern production processes. This venerable method involves pouring molten metal into a sand mold to create a wide variety of metal parts with intricate shapes and sizes. Among the different types of sand casting processes, each has its unique characteristics, making it suitable for specific applications. Here, we delve deep into the types of sand casting with insights from seasoned professionals, shedding light on the nuanced experience, expertise, and trust that underpin this traditional yet dynamic industry.
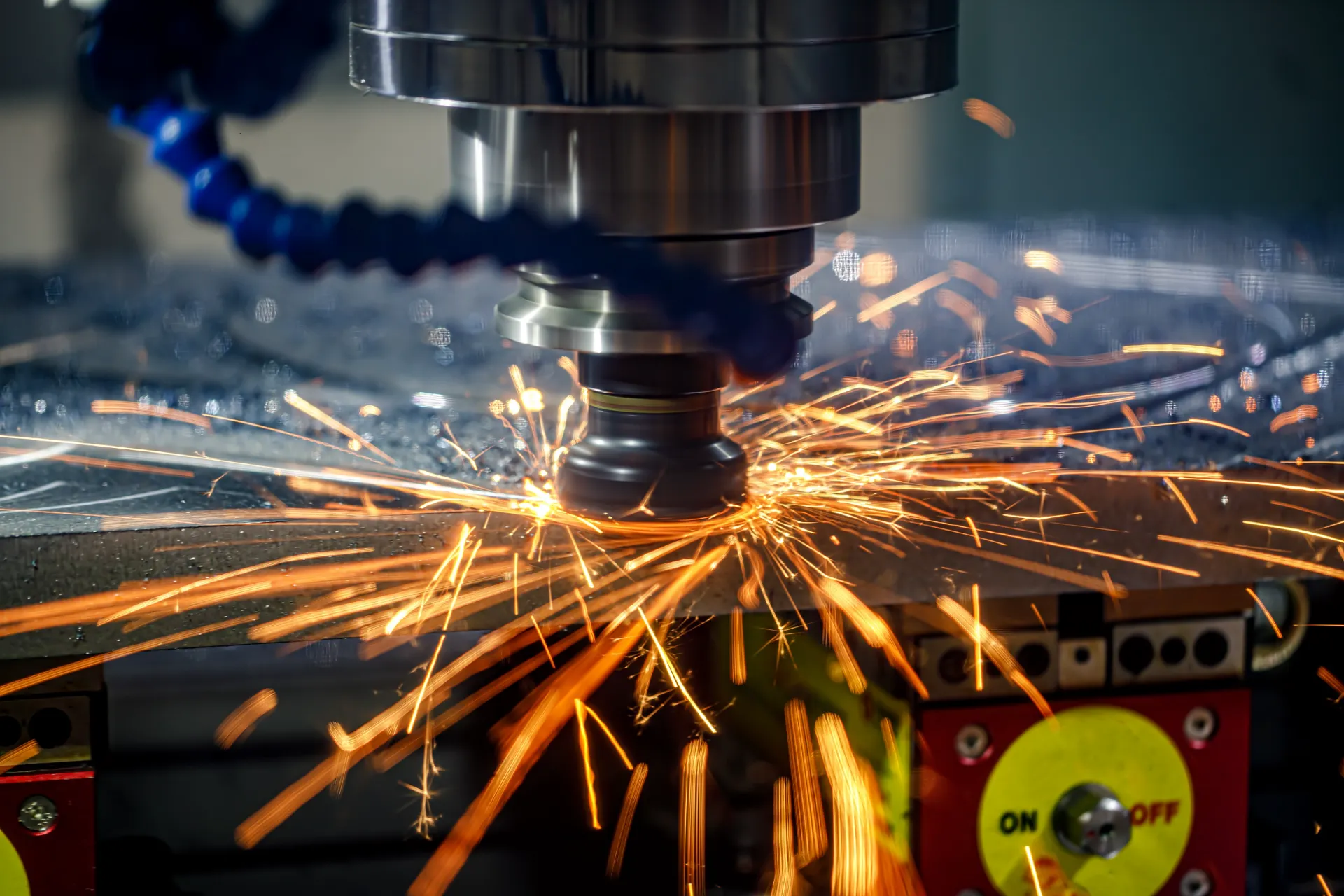
At the heart of sand casting is the green sand molding process, named for its moisture-rich composition. This method uses a mix of sand, clay, and water, forming a pliable mold that can produce detailed castings efficiently. Various experts acknowledge green sand molds for their cost-effectiveness and adaptability across a myriad of production scenarios. The process's ability to recycle mold materials adds an additional layer of sustainability that industries are increasingly valuing. Practitioners in the field praise its responsive adaptability to different metals, including aluminum, iron, and bronze, which allows for flexibility without compromising on quality.
Another popular variant is the dry sand mold technique. As its name suggests, this process involves the use of sand that has been chemically bonded, often providing superior strength and dimensional control. The lack of moisture helps mitigate gas-related defects during casting, a common concern in green sand molds when high temperatures are involved. Industries reliant on precision and durability, such as aerospace and automotive sectors, lean heavily on dry sand casting. Experts recognize this method for its ability to produce more structurally sound and reliable components that can withstand rigorous performance standards.
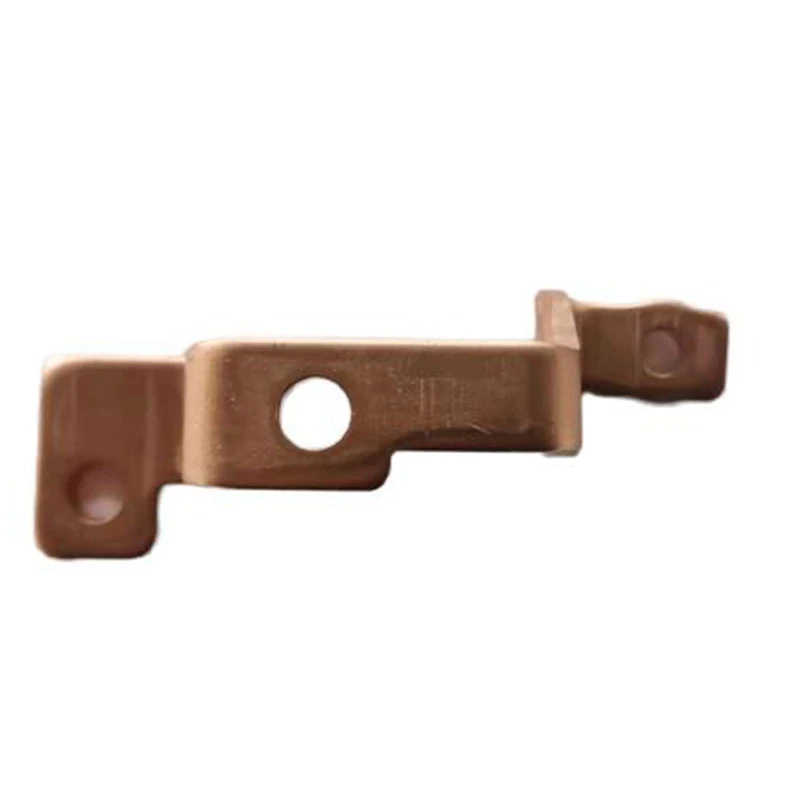
The investment in chemically bonded sands represents an intersection of tradition and innovation, demonstrating the field's responsiveness to the demands of modern engineering challenges. Chemical binders, including furan and phenolic esters, have revolutionized mold stability, particularly useful in larger castings where the risks of shifting and deformation are magnified. Companies that have employed chemically bonded sands report buoyed productivity due to reduced defect rates and decreased need for post-casting machining – a testament to expert-driven advancements in the field.
sand casting types
Furthermore, lost foam casting, a process gaining traction, expounds on the adaptability of sand casting by using expandable foam patterns. When these patterns are encapsulated in unbonded sand and the metal is poured, the foam evaporates, leaving behind a precise casting. This method shines in reducing machining time and waste metal, aligning with the industry's growing commitment to sustainability. Experts in metallurgy highlight its efficacy in producing complex geometries, making it indispensable for innovative designs in modern manufacturing spheres.
Finally, air set mold or no-bake mold casting rounds out the primary sand casting types with its distinct use of dry sand and a fast-setting resin binder. Praised for its incredible strength and rigidity, air set molds afford operators the luxury of creating large-scale components without sacrificing detail or structural integrity. Industries focusing on heavy machinery and infrastructure often turn to this method, capitalizing on its reputation for producing components that can endure severe working environments.
In conclusion, sand casting remains a bedrock of industrial manufacturing, possessing a versatility mirrored in its various types. By leveraging expertise and insights from seasoned professionals, industries can match their specific requirements with the most fitting sand casting method. The ongoing innovation within sand casting methods not only showcases the expertise and authority of professionals in the field, but also reinforces the trust industries place in this time-tested technique to produce high-quality, reliable components. As manufacturing processes continue to evolve, the fundamental principles of sand casting will undoubtedly persist, adapted expertly through rich experience and driven by a profound commitment to excellence.