Sand casting remains a cornerstone technique in the manufacturing industry, providing an efficient solution for creating complex metal components. At the heart of this process lies the critical component sand. More than just particles, the sand used in casting provides the mold structure and influences the final product's quality. Choosing the right sand supplies is vital for success, and we delve into why understanding and selecting high-quality sand is crucial for your casting operations.
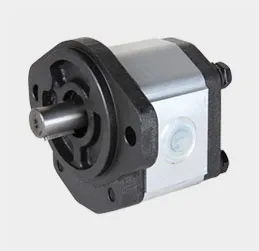
Sand casting sand supplies come in a range of types and grades, each with distinct properties that affect molding. Whether you’re a novice exploring sand casting or a seasoned expert, understanding these properties is indispensable. Silica sand, for instance, is the most pervasive choice due to its good refractory properties and availability. However, for more specialized applications, chromite sand, olivine sand, and zircon sand are also employed. These sands offer unique benefits such as low thermal expansion and enhanced permeability – characteristics that can drastically influence casting outcomes.
Experience guides us toward evaluating sand quality through various parameters. Grain shape, size, and distribution are pivotal in determining the mold quality. Round grains offer good permeability, whereas angular grains provide superior adhesion. The fineness of sand, often measured by AFS (American Foundry Society) grain fineness number, directly influences surface finish and mold strength. Therefore, understanding these variables not only requires technical knowledge but also practical insight into how they impact your casting process.

From an expertise perspective, the binding agents mixed with sand are crucial to achieving the desired mold performance. Clay binders like bentonite provide sufficient bond strength and thermal stability. In contrast, organic binders such as resin offer better surface finishes and are preferred for more intricate detail. The balance between strength, flexibility, and erosion resistance is crucial, which necessitates knowledge of sand chemistry and binder interactions. Past projects have shown that even slight changes in these parameters can significantly affect the soundness and surface quality of the cast component.
sand casting sand supplies
Authoritativeness in sand casting also encompasses the environmental and safety aspects of sand selection. Regulatory bodies have been increasingly stringent with health-related concerns, such as silica dust exposure, pushing manufacturers toward more sustainable and health-conscious alternatives. Green sand, a mixture of silica sand, clay, water, and other additives, represents a more environmentally friendly solution with its ease of reclamation and lower emission levels.
Trustworthiness in supplying the right sand for casting is built on a foundation of consistent quality, fair pricing, and reliable delivery. Partnering with reputable suppliers ensures that the sand used aligns with industry standards and your specific requirements. Suppliers who offer test certificates and detailed material specifications empower you to make informed decisions, reducing the risk of casting defects and ensuring project timelines are met. This level of transparency and consistency fosters a reliable production environment, opening avenues for innovation within traditional sand casting methods.
In conclusion, navigating the complexities of sand casting sand supplies requires an intricate blend of experience, expertise, authoritativeness, and trustworthiness. Understanding material properties is not merely an academic exercise but a practical necessity for optimizing production efficiency, quality, and sustainability. By leveraging knowledge in sand selection, binding materials, and industry standards, manufacturers can enhance product integrity while maintaining cost-effectiveness. Embrace the art and science of sand casting with a comprehensive approach to sand supplies, and you’ll undoubtedly see an improvement in your casting outcomes.