In the realm of industrial manufacturing, sand casting stands as a pillar of robust production processes. With roots tracing back to ancient times, this method has evolved significantly, becoming a cornerstone in creating a myriad of metal components. As a method, it is both economically viable and highly adaptable, catering to industries from automotive to aerospace and beyond.
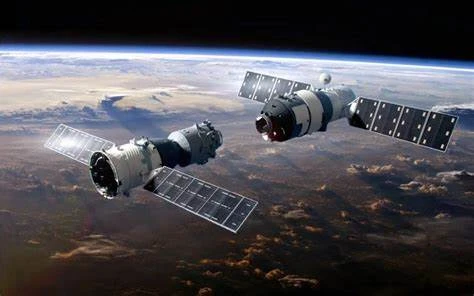
The experience of working within a sand casting facility is akin to witnessing a symphony of science, engineering, and art. Each phase of the process requires meticulous attention to detail and a deep understanding of material properties and behaviors. Upon entering a state-of-the-art facility, the aroma of freshly cured molds imbues the atmosphere, setting the stage for innovation and creation.
Professional expertise in sand casting demands a comprehensive grasp of both the theoretical principles and pragmatic techniques inherent to the process. The journey begins with the creation of a pattern, often crafted from materials such as wood, metal, or plastic. This pattern forms the precise shape of the desired final product and serves as the template for mold construction. At this stage, expertise in design and engineering principles is paramount, ensuring the pattern accounts for shrinkage, draft angles, and intricate geometrical features.
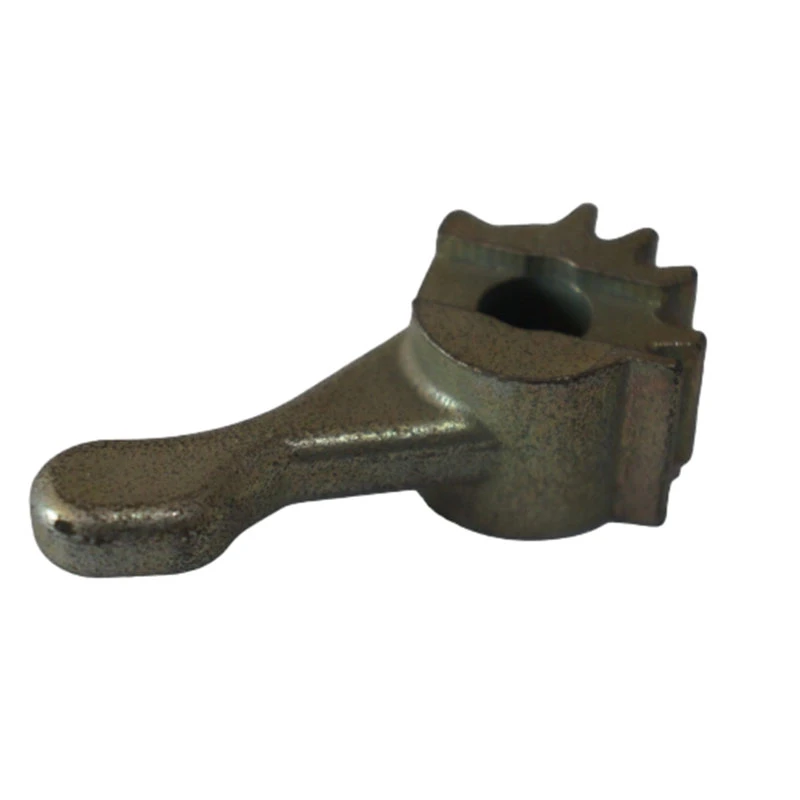
Upon completing the pattern, skilled craftsmen utilize it to construct a sand mold. The selection of sand – typically silica due to its high refractoriness and availability – is critical. Engineers often enhance sand with materials like clay and resin to fortify the mold and ensure its stability and precision under extreme temperatures. This part of the process is where traditional craftsmanship meets modern technology, with techniques that have been honed through centuries being augmented by contemporary innovations.
A pinnacle of authoritative application in sand casting lies in the alloy selection. A well-versed metallurgist plays a vital role here, advising on the alloy's suitability based on the component's intended function, the environmental conditions it will endure, and the mechanical stresses it must withstand. Each alloy requires specific melting practices, and expertise ensures the molten material retains homogeneity while minimizing the risk of defects like porosity or inclusions.
The pouring phase epitomizes the delicate dance between science and art. Trustworthiness in this stage is non-negotiable, as the fidelity of the entire casting hinges on precise handling of molten metal. Operational personnel employ cutting-edge techniques and often advanced robotic systems to manage the pouring, guaranteeing the mold is filled under optimal conditions to prevent turbulence and ensure even cooling.
sand casting manufacturing
Once the metal solidifies, demolding occurs, unveiling a raw casting that requires further refining. This is where machining expertise transforms a mere casting into a functional and precise component. Advanced CNC machines and finishing techniques bring the metal to its exact specifications, with fidelity measured in microns.
Throughout the sand casting process, credibility is reinforced through rigorous quality assurance protocols. Prior to leaving the facility, each component undergoes a battery of inspections, from visual checks to sophisticated non-destructive testing methods. These procedures not only ensure compliance with industry standards but also bolster trust in the component's performance.
Embracing cutting-edge technologies, such as simulation software, has further enhanced the reliability and efficiency of sand casting. These tools allow engineers to model the casting process digitally, predicting potential issues and optimizing parameters before physical production begins. This preemptive approach exemplifies authoritative,
modern manufacturing practices.
As industries continually seek ways to reduce their environmental footprint, sand casting offers a sustainable solution. The sand used in molds can be recycled and reused, reducing waste and conserving resources, aligning manufacturing processes with contemporary environmental expectations.
In essence, sand casting manufacturing is not merely a production technique but a testament to the harmonious blend of historical craftsmanship and modern scientific achievement. Its enduring relevance and adaptability speak volumes of its effectiveness and dependability, making it an invaluable asset to global manufacturing efforts.