Sand casting, an ancient yet remarkably effective method, lies at the core of manufacturing grey cast iron products. The process involves crafting a sand mold to form this pivotal alloy, known for its excellent machinability, vibration damping properties, and wear resistance. Grey cast iron's distinct graphite microstructure lends it unique characteristics, enhancing its performance in various industrial applications.
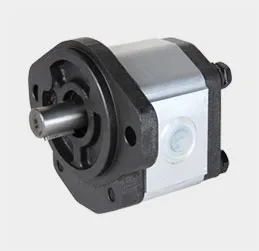
To achieve superior quality and durability in grey cast iron products, precise control over the sand casting process is crucial. The first step involves creating a pattern, usually made from wood, plastic, or metal, reflecting the size and shape of the desired final product. This pattern is then used to construct the sand mold. Properly formulated, the sand mixture is key; it typically comprises silica sand, clay, and water. The blend must be managed carefully to ensure requisite mold strength and permeability, thereby preventing defects such as porosity or poor surface finish.
Once the mold is crafted,
molten grey cast iron is introduced into the cavity. Mastery of the pouring process is essential. The melting temperature must be accurately maintained to avoid overcooling or overheating, which could compromise the integrity of the casting. Moreover, the pouring speed must be controlled to minimize turbulence, which can lead to flaws like air entrapment.
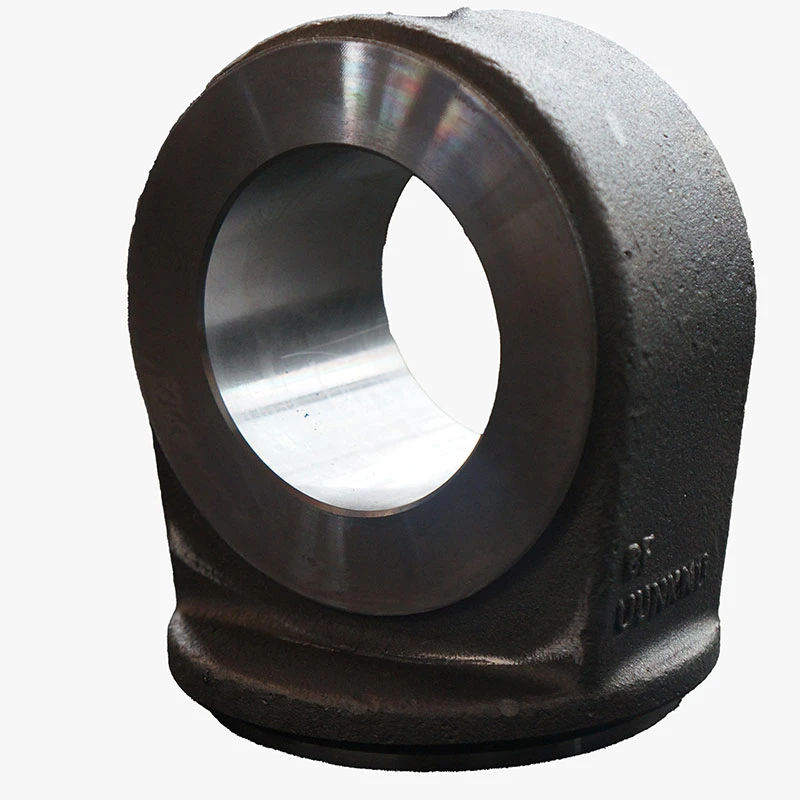
Grey cast iron boasts an array of mechanical properties that make it invaluable across industries. Its compressive strength and rigidity make it ideal for use in constructing machine tool bases, cylinder blocks, and pipes. Additionally, its thermal conductivity and ability to withstand thermal cycling suit it perfectly for kitchen utensils and automotive components, where consistent performance under varying temperatures is vital.
sand casting grey cast iron
Understanding the nuances of sand casting grey cast iron allows manufacturers to innovate and optimize product quality. Employing advanced techniques such as computer simulations can predict potential defects and improve mold design. It ensures that every casting meets exacting standards, vital for industries where precision and reliability are non-negotiable.
Expertise in both the chemistry and physics of grey cast iron further enhances the process. Knowledge of metallurgy allows adjustments to the iron's composition, optimizing properties like hardness and tensile strength for specific applications. By tweaking the carbon and silicon content, or adding trace elements, distinct variants of the alloy can be crafted to meet diverse industrial needs.
This approach underscores the worth of expertise within the manufacturing realm, especially in sectors reliant on grey cast iron. Continuous research and development elevate the process, driving innovations that ensure the material remains indispensable, even in modern times. The ever-evolving landscape of sand casting grey cast iron emphasizes the blend of tradition with technological advancements, harnessing the material’s inherent strengths while adapting to contemporary demands.
Products forged from grey cast iron through sand casting endure as symbols of reliability and efficiency. The deep-rooted trust in their performance is a testament to the meticulous efforts in their creation, ensuring quality control at every step. From the crafting of the mold to the final machining of the casting, each phase demands dedication and precision, underpinning the trustworthiness expected in high-stakes industrial applications. The expertise applied to this time-honored process assures not just functionality, but excellence, ensuring it remains a cornerstone of product manufacturing for years to come.