Turning a backyard or garage into a space for sand casting aluminum is an exciting prospect for DIY enthusiasts and small-scale craftsmen. This art and science combine to create anything from custom car parts to artistic sculptures. The unique appeal of sand casting at home lies not only in its practicality but also in the creative expression it facilitates. But just like any craft, it requires a blend of experience, expertise, and attention to detail to achieve successful results.
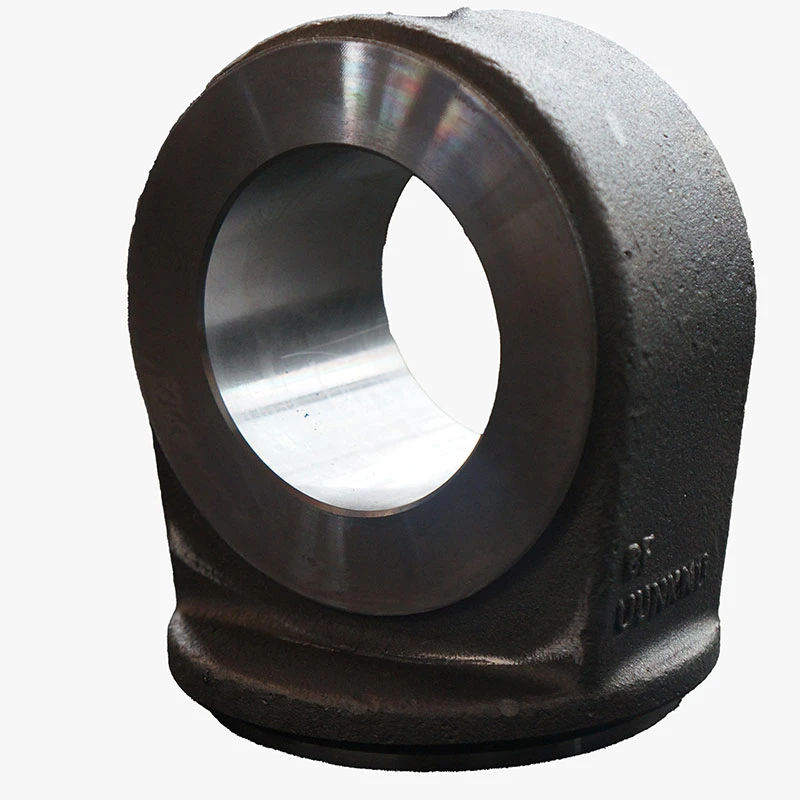
Starting with the fundamentals, sand casting aluminum at home begins with understanding the materials and tools you will need. Aluminum, due to its lightweight and malleable properties, is a preferred choice. It’s crucial to source quality aluminum, often recycled from old engines or redundant window frames, balancing cost-effectiveness with quality.
Next, creating the mold is vital. This requires patience and practice, typically using a mixture of sand, clay, and water, forming what is known as green sand. The key here is achieving the right moisture content; too wet or too dry sand can ruin the mold’s stability and precision. For newcomers, experimenting with small, simple molds is advisable to comprehend the sand consistency and packing technique.
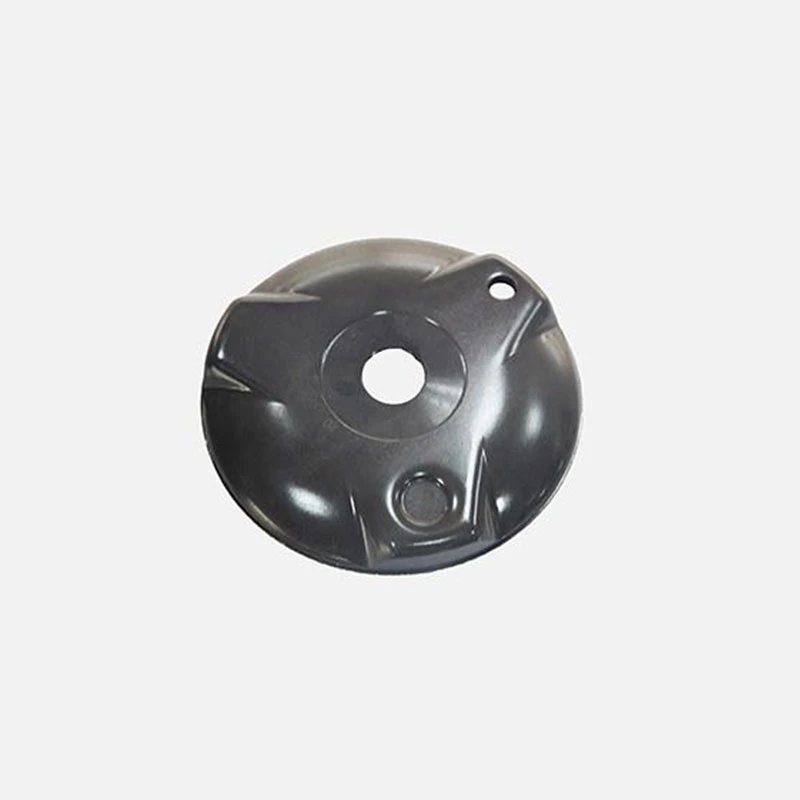
Safety cannot be overstated when engaging in home foundry work. Aluminum’s melting point exceeds 1200°F, necessitating appropriate protective gear—heat-resistant clothing, gloves, eye protection, and a quality respirator mask. Working in a well-ventilated area is crucial to avoid hazardous fumes, along with a clear understanding of emergency procedures in case of spills or burns.
Melting aluminum requires a reliable furnace. Homemade furnaces often utilize a steel drum, lined with heat-resistant materials, and can be powered by propane or charcoal. Precision in controlling temperature and melting time differentiates a rough casting from a refined one. For those more experienced, considering an electric furnace might elevate the level of control over the melting process.
Expertise in sand casting develops with the finesse in pouring the molten aluminum into molds. Pouring requires a steady hand and timing as mistakes here can introduce air pockets or incomplete casts. Understanding thermodynamics plays into the cooling phase; slow, even cooling helps in avoiding cracks and ensuring dimensional accuracy. These are subtle arts learned over repeated attempts and builds, turning experience into mastery.
sand casting aluminum at home
Post-casting, the work transitions into finishing. This involves breaking away excess sand, grinding burrs, sanding, and polishing the finished piece. Each step demands attention to detail as carelessness can lead to surface flaws or structural weaknesses. Hands-on experience becomes invaluable here, with each project informing the precision and efficiency of future endeavors.
For those wondering about the legitimacy of crafting at this scale, historical context offers credibility. Sand casting has been used for centuries, creating tools, household goods, and even art. The knowledge passed down is an endorsement from eras of craftsmen who laid the foundation for today’s backyard innovators.
In essence, home sand casting is not merely about melting and molding metal. It is a multifaceted craft demanding a combination of safety precautions, technical understanding, and artistic vision. As projects evolve in complexity, so does the craftsman’s capability and pride. Sharing these experiences in community forums and collaborating with other enthusiasts elevates one's skills, fostering a rich knowledge base that benefits newcomers and veterans alike.
Undoubtedly, patience and practice are the pathways to precision. It's an endeavor where the learning curve serves as the crucible, forging both skill and character. These foundational elements build trust among peers and professionals in the community, establishing credibility and authority in the nuanced world of metalwork.
For product developers and artists alike, mastering sand casting at home can result in unique pieces that stand apart in a marketplace increasingly interested in bespoke, original designs. As each project progresses, the blend of traditional technique and modern innovation set these craftsmen apart, ensuring their creations—and methods—are as unique as they are efficient.