Progressive die and stamping, pivotal to modern manufacturing, are gaining unprecedented attention for their efficiency, precision, and capability to handle complex designs. Their increasing application across industries from automotive to electronics underscores a transformative phase in component manufacturing.
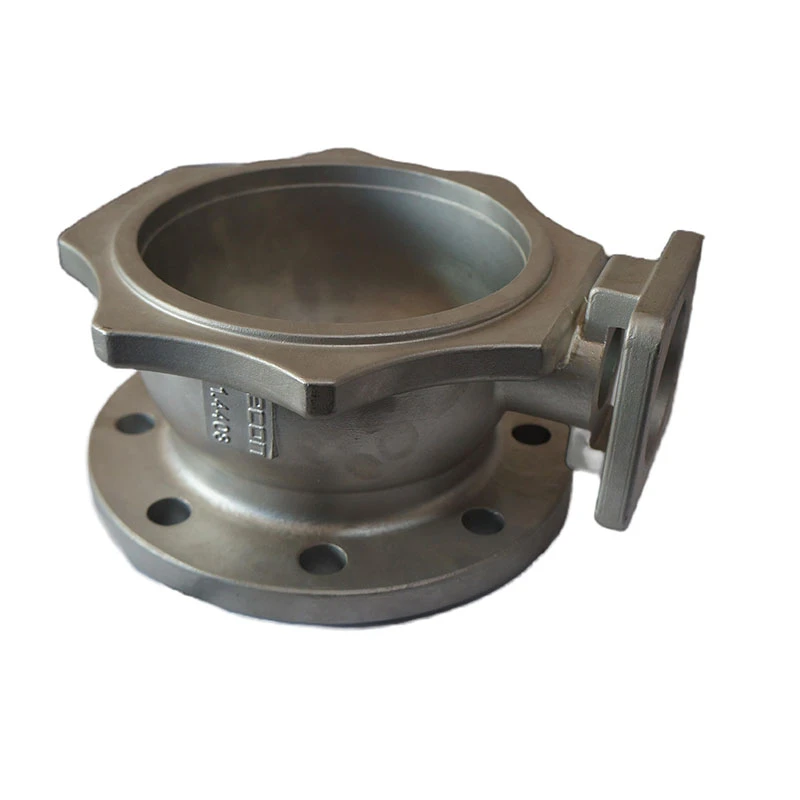
Progressive die stamping involves a sequence of stamping stations. Here, each station within a single die performs a specific operation on the workpiece. It results in the creation of a finished part with every stroke of the press. This method ensures streamlined mass production with enhanced precision and minimal material waste, meeting demands for high-volume manufacturing with remarkable accuracy.
Experience and Precision in Production
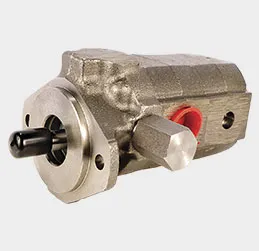
Leveraging progressive die and stamping presents undeniable advantages, yet it demands a profound commitment to craftsmanship. Experienced manufacturers understand that the design phase is critical. Intricate designs require meticulous planning to ensure every subsequent stamping station contributes precisely to the finished product. Consequently, extensive design simulations and prototyping become indispensable, allowing manufacturers to preemptively address potential pitfalls.
Seasoned engineers play a crucial role throughout this process. They apply their wealth of hands-on experience to anticipate complications, thereby refining operations. Their expertise ensures that the final products align with exact specifications, ensuring seamless integration into larger assemblies.
Expertise in Tooling and Materials
The versatility of progressive dies calls for a thorough understanding of tooling materials and their properties. Tool steel is commonly preferred for its durability and ability to withstand the repetitive stresses of stamping operations. Additionally, manufacturers continuously innovate with carbide and other advanced alloys to enhance wear resistance and longevity. The choice of materials is often dictated by the type of metal being stamped — from stainless steel to aluminum — ensuring optimal results and minimal tool degradation.
Expert manufacturers also emphasize regular maintenance and audits of their stamping tools. An abiding focus on quality control guarantees that tools are sharp and aligned, preventing downtime and preserving the integrity of the production run.
progressive die and stamping
Authoritativeness and Industry Standards
Progressive die and stamping find prominence in industries such as automotive manufacturing, where conforming to stringent safety and quality standards is non-negotiable. Automotive components demand exceptional precision and reliability, attributes that progressive die stamping inherently delivers. The aerospace industry similarly benefits, with parts that meet unmatched exactitude due to rigorous adherence to international standards and certifications.
Authoritative voices in the industry advocate for the adoption of ISO and AS certifications, ensuring compliance with global safety and quality benchmarks. This authoritative acknowledgment of process integrity and product excellence positions reputable stamping facilities as leaders within the manufacturing domain.
Trustworthiness in Partnership and Production
In choices regarding outsourcing progressive die and stamping services, trust forms the cornerstone of successful partnerships. Manufacturers with a proven track record of reliability foster enduring relationships with clients by meeting and exceeding expectations consistently.
Firms that offer transparency in their processes and maintain open channels of communication build this trust. Clients appreciate insights into every stage of production — from initial design considerations to final quality checks. This transparency not only solidifies partnerships but enhances trustworthiness across all interactions.
The future of progressive die and stamping lies in evolving technologies such as AI-driven design optimization and IoT-enabled monitoring systems. These innovations promise even greater precision, efficiency, and real-time quality assurance, heralding a new era of manufacturing prowess.
In conclusion, embracing progressive die and stamping is a step toward achieving unparalleled manufacturing accuracy and efficiency. With a steadfast focus on quality, expert execution, and transparent partnerships, businesses can ensure their competitive edge in rapidly evolving markets.