Jet cooling in die casting represents a significant technological advancement in enhancing the quality and efficiency of die-cast products. This specialized cooling method provides notable improvements over traditional cooling techniques, offering manufacturers a competitive edge in precision and cost-effectiveness.
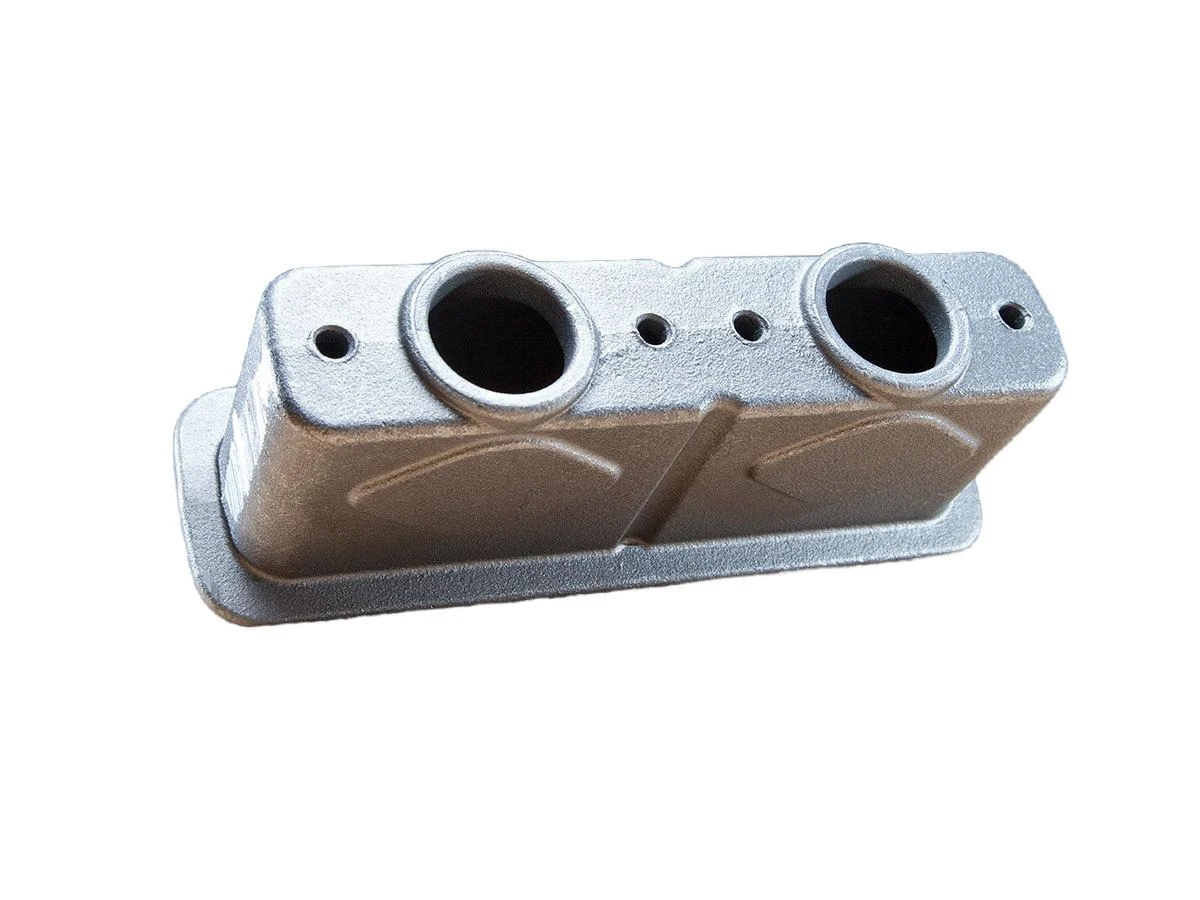
In the realm of die casting, maintaining optimal mold temperatures is crucial for product integrity. Traditional cooling methods often fall short, leading to defects such as porosity and inadequate mechanical properties. Enter jet cooling—a high-efficiency process that utilizes high-velocity air or fluid jets directed at specific mold areas, ensuring rapid and uniform temperature reduction.
Experience in the field shows that jet cooling significantly reduces cycle times, thereby enhancing production efficiency. By delivering targeted cooling directly where needed, it minimizes thermal gradients that can lead to warping or dimensional inaccuracies. This precision cooling allows for faster solidification, which not only speeds up production but also enhances the microstructural properties of the cast metal, leading to a superior product with better finish and improved strength.
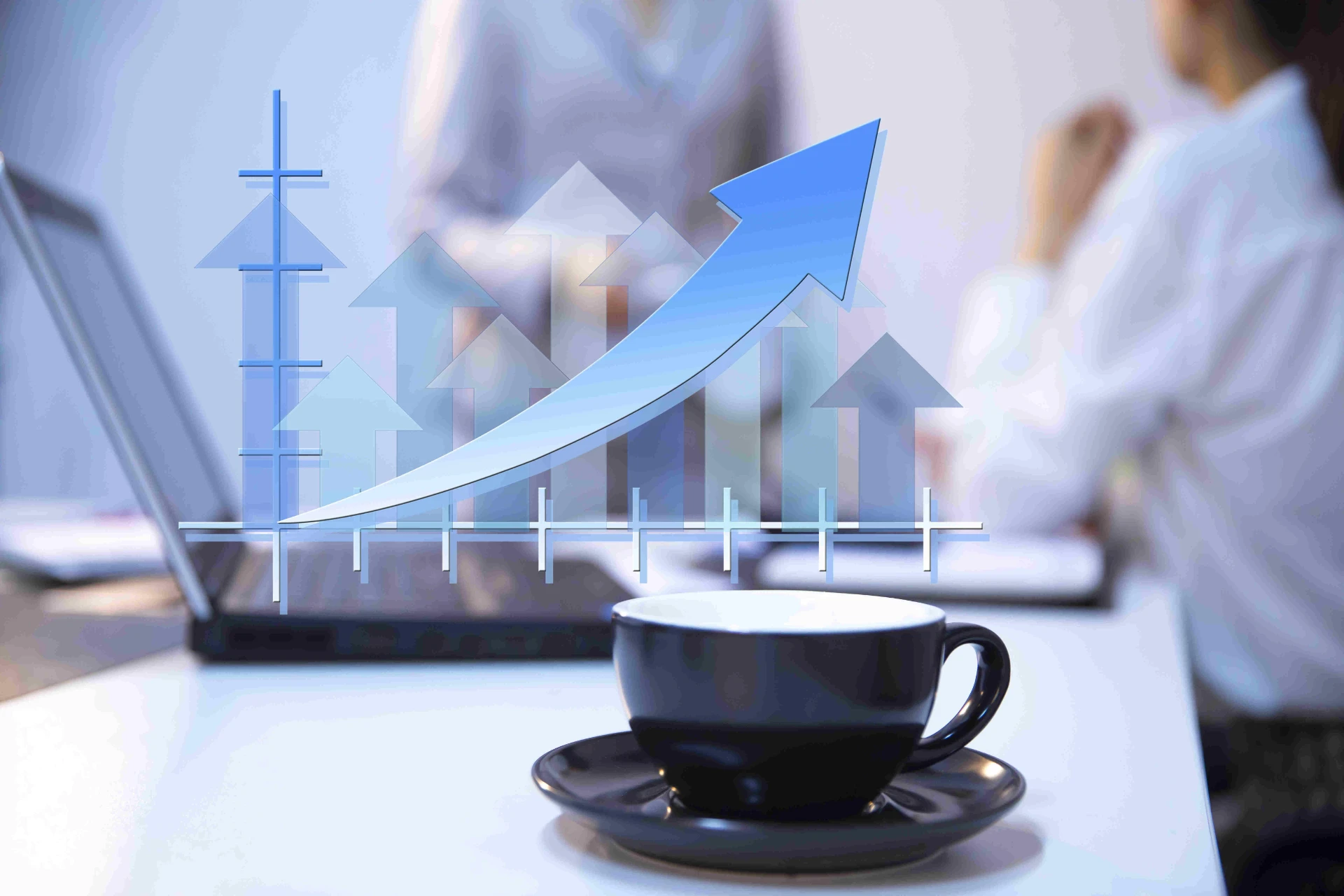
The expertise behind jet cooling technology is rooted in thermodynamics and fluid dynamics. Specialists in these fields have meticulously analyzed the flow patterns and heat transfer coefficients to optimize nozzle design and placement, ensuring that the cooling is both effective and energy-efficient. This depth of expertise means that manufacturers can adopt this technology with confidence, knowing it is backed by rigorous scientific principles and testing.
Authoritativeness in jet cooling is increasingly being recognized by industry leaders. Reports and case studies from respected organizations highlight its benefits in various applications, from automotive parts to complex industrial components. One notable example includes its application in the production of aluminum alloy wheels, where jet cooling has been shown to reduce scrap rates significantly while maintaining stringent quality standards. Such endorsements from authoritative bodies underline the transformative potential of jet cooling in die casting processes.
jet cooling in die casting
Trustworthiness of the technology is further established by documented success stories and testimonials from manufacturers who have integrated jet cooling into their processes. These narratives emphasize consistent quality improvements and cost savings, building a strong case for its adoption. Moreover, the equipment required for jet cooling is typically robust, requiring minimal maintenance, which further cements its reliability and appeal.
In terms of product offerings, suppliers of jet cooling solutions provide comprehensive systems that are customizable to specific casting needs. These systems often include advanced control units that allow for precise adjustment of cooling parameters, ensuring maximum compatibility with different mold designs and materials. The ability to tailor cooling profiles to specific casting scenarios not only enhances product quality but also maximizes energy efficiency, reducing operational costs.
As manufacturers seek to optimize their processes in an increasingly competitive market, jet cooling stands out as a cutting-edge solution. Its ability to deliver high-quality cast products at reduced cycle times and costs makes it an indispensable tool for modern die casting operations. Embracing jet cooling technology not only satisfies immediate production needs but also supports long-term sustainability goals, thanks to its energy-efficient design.
Furthermore, training programs and support services provided by suppliers ensure that manufacturers can seamlessly integrate jet cooling into their production lines. These programs cover everything from initial setup and calibration to advanced troubleshooting techniques, ensuring that teams are fully equipped to leverage the full potential of the technology.
In conclusion, jet cooling in die casting is more than just a technological upgrade; it is a strategic enhancement that elevates casting operations to new heights of efficiency and quality. Its proven advantages in reducing cycle time, improving product quality, and lowering operational costs makes it a highly valuable investment. As the industry moves toward more sophisticated and sustainable manufacturing practices, jet cooling is poised to play a central role in shaping the future of die casting.