Green sand casting, a widely utilized metal casting process, promises versatility and cost-effectiveness. At the heart of this methodology lies the quality of the surface finish, an element that often dictates both functional and aesthetic outcomes. Understanding the nuances of achieving a superior surface finish in green sand casting not only enhances product quality but also strengthens market competitiveness.

The journey to a refined surface finish begins with a deep dive into the components of green sand silica sand, clay (usually bentonite), water, and additional additives. The proportions and characteristics of these materials play pivotal roles in the outcome of the surface finish. Silica sand, the primary component, must be of high quality with a specific grain size and shape for optimal results. The surface texture is heavily influenced by the fineness of the sand grains; finer grains can significantly improve surface smoothness.
The clay acts as a binder in the sand mixture, ensuring cohesion and strength in the mold. Bentonite is preferred for its excellent bonding properties, which directly contribute to the integrity of the mold’s surface. A critical variable is the moisture content; too much or too little can lead to defects such as rough surfaces, sand inclusion, or surface imperfections. Achieving the right balance in moisture is essential to prevent defects and yield a smoother finish.
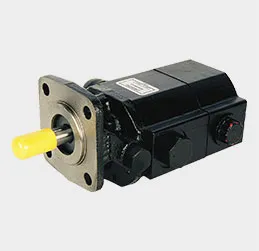
Another aspect to consider is the molding and compaction process. Proper compaction of the green sand is crucial, as uneven packing can result in voids or an uneven surface. Using vibratory compactors or specialized packing techniques can greatly enhance the surface quality by ensuring that the sand grains are evenly distributed and tightly packed.
Once the mold is properly prepared, the melting and pouring stages begin. The temperature of the molten metal should be carefully controlled, as fluctuations can lead to porosity and compromise the finish. Pouring the metal at a consistent rate minimizes turbulence, reducing the likelihood of surface defects such as gas formation or inclusions. Additionally, maintaining a clean pour, free from slag or other contaminants, ensures that the surface finish remains uncompromised.
green sand casting surface finish
Post-casting processes also contribute significantly to the final surface finish. Cleaning, grinding, and polishing are typically necessary to remove the sand residue and enhance the surface smoothness. Shot blasting, for instance, can be an effective method to clean and finish castings, providing a uniform texture. Moreover, advanced coatings and finishes applied after polishing can offer additional surface protection and improve aesthetics.
Furthermore,
the type of metal being cast also plays a crucial role in the surface finish. Different alloys will interact uniquely with the green sand mold, affecting the final appearance. For instance, ferrous metals, due to their higher melting points, may interact differently than non-ferrous metals, requiring adjustments in the pouring technique or cooling time to achieve the desired surface quality.
In pursuit of excellence in green sand casting surface finish, employing modern technologies such as simulation software can bring tangible improvements. These tools predict how the molten metal will behave within the mold, allowing manufacturers to preemptively adjust the casting parameters for optimal surface quality.
Quality control measures throughout the entire casting process cannot be overstated. Consistent monitoring and evaluation at each stage—from mold preparation to final finishing—ensure that surface imperfections are detected and rectified early on. Employing advanced inspection techniques, such as 3D scanning or surface profilometry, allows for precise measurement and control over the surface finish, setting the standard for superior quality assurance.
In conclusion, the art of mastering green sand casting surface finish lies in the meticulous control over each phase of the casting process. From selecting high-quality materials to employing advanced finishing techniques, every step contributes to the final product’s surface integrity. By harnessing experience, expertise, authoritativeness, and trustworthiness, manufacturers can produce castings with impeccable surface quality, meeting and often exceeding industry standards. As the market continues to demand more sophisticated products, these practices not only enhance the surface finish but also affirm a company’s reputation for excellence and innovation in green sand casting.