Gravity die casting, a specialized process used in the manufacturing sector, involves pouring molten metal into a mold under the force of gravity. This method is favored by many industries due to its precision, cost-effectiveness, and suitability for medium to high volume production runs.
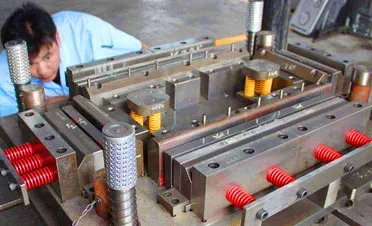
Notably, gravity die casting stands out in its ability to produce components with intricate details and smooth surface finishes, which makes it ideal for automotive, aerospace, and machinery applications. Gravity die, commonly made from metal, offers a durable option that withstands repeated use, thus making it a cornerstone in efficient production cycles.
In-depth understanding and expertise in gravity die casting are essential for leveraging its full potential. The process begins with the careful design and construction of the die itself. Engineers and designers collaborate to ensure the die is capable of producing parts that meet exact specifications. Design considerations include mold material, thermal conductivity, and cooling rates, as these factors influence the final product's integrity and performance.
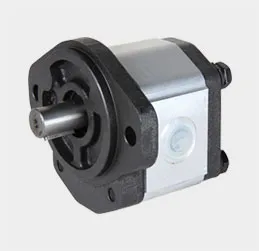
Successful gravity die casting requires a blend of experience and technical knowledge. Professionals in this field must be adept in metal properties, be they aluminium, zinc, or magnesium, and understand how each metal reacts under different conditions. Mastery over pouring techniques, cooling curves, and solidification patterns ensures that the final product is free from porosity, shrinkage, and other defects.
This expertise results in parts with consistent quality and structural reliability.
gravity die
When selecting a supplier for gravity die casting services, assessing their authoritativeness in the industry is crucial. Suppliers with a long-standing reputation often have extensive case studies and references that validate their capabilities. Look for certifications and affiliations with industry bodies as these are indicative of a supplier's commitment to maintaining high standards and staying updated with technological advancements.
Trustworthiness is equally vital in partnerships involving gravity die casting. A supplier who guarantees transparency in their processes and offers comprehensive quality assurance checks is more likely to deliver components that meet or exceed expectations. They should employ rigorous testing, such as X-ray and metallurgical inspection, to ensure that the final products adhere to the defined specifications.
A trustworthy supplier also provides insightful guidance on cost reduction without compromising quality. By optimizing designs and streamlining production, they offer solutions that reduce waste, improve resource utilization, and ultimately, lower costs. Such an approach not only benefits the immediate project but also enhances long-term partnerships.
Gravity die casting is a sophisticated art and science, driven by the principles of engineering and innovation. It transforms molten metal into vital components that propel various sectors forward. For businesses seeking reliable and high-quality manufacturing solutions, engaging with a knowledgeable and credible gravity die casting expert is paramount. Ultimately, these experts hold the key to unlocking efficiency and excellence, ensuring every component is crafted to perfection and delivered with utmost precision.