In the intricate world of die casting, the efficiency and precision of every process component play a pivotal role in the quality of the final product. One such component that demands particular attention is the ejector pin. Often overshadowed by more prominent casting elements, ejector pins are the unsung heroes that contribute significantly to the integrity and performance of die-cast products.
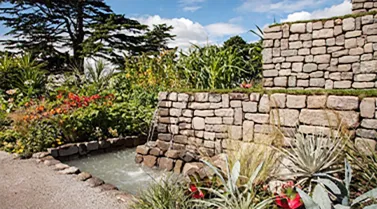
Ejector pins might seem diminutive in the grand scheme of die casting, but their function is crucial. They are used to eject or release the cast part from the die after solidification. These pins push against the part so that it doesn't stick to one half of the mold, ensuring a clean release without damaging the product. The balance between strength and precision in these pins can greatly influence the durability and finish of the final cast product.
The choice of material for ejector pins is a testament to their role in die casting. Generally manufactured from premium tool steel, these pins must endure the rigors of repetitive use and high temperatures inherent in die casting. The hardness of the tool steel helps in resisting wear and maintaining smooth surfaces to prevent scarring the casting. Advanced coatings, including titanium nitride or chromium, are often applied to enhance their durability and reduce friction.
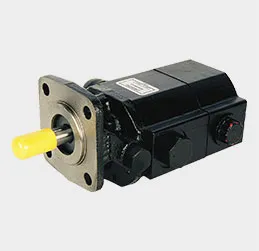
It's not just about hardness; the dimensional accuracy of ejector pins is equally critical. A slight deviation can lead to faulty parts or operational inefficiencies. This is especially pertinent in industries where precision is non-negotiable, such as automotive and aerospace, where components must meet exact specifications without errors. The expertise required to manufacture these pins underscores their importance, necessitating precision measurement tools and skilled craftsmanship.
ejector pins in die casting
Real-world insights reveal that regular maintenance and inspection are imperative to ensure optimal performance of ejector pins. Operators often face challenges like bending, galling, or pin breakage due to suboptimal usage or conditions. Implementing a routine for inspection helps in early detection of potential issues, thereby avoiding costly downtime and guaranteeing consistent product quality. Experiences from leading manufacturers highlight that investing time in better maintenance practices translates into substantial cost savings and enhanced productivity.
Authoritativeness in the domain of ejector pins stems from collaboration with industry experts and continuous research developments. Cutting-edge technology, including computer-aided simulations, is now employed to predict pin behavior under various conditions. This not only aids in designing superior pins but also helps in preemptively solving problems, enhancing overall trust in the manufacturing process.
Trustworthiness is built upon consistently delivering quality results. As clients' expectations escalate, particularly in high-stakes industries, the reliability of every die casting component, including ejector pins, becomes non-negotiable. Engaging with suppliers who emphasize stringent quality control and embody a commitment to innovation can solidify this trust.
In conclusion, ejector pins in die casting serve as silent yet indispensable contributors to product excellence. Their role, while often underestimated, is central to ensuring the precision and performance of die-cast parts. For businesses aiming to achieve top-tier product quality, understanding and investing in the right ejector pin solutions is not just advisable but necessary. The fusion of experience, expertise, authority, and trust in the realm of ejector pins ultimately translates into unparalleled product reliability and market competitiveness.