Die casting plungers play a critical role in the manufacturing world, particularly within the die casting process, where precision and efficiency are of utmost importance. As a seasoned SEO specialist with an in-depth understanding of die casting and its components, the purpose here is to delve into the intricacies of die casting plungers, highlighting their expertise, authority, and trustworthiness (E-E-A-T) in the industry.
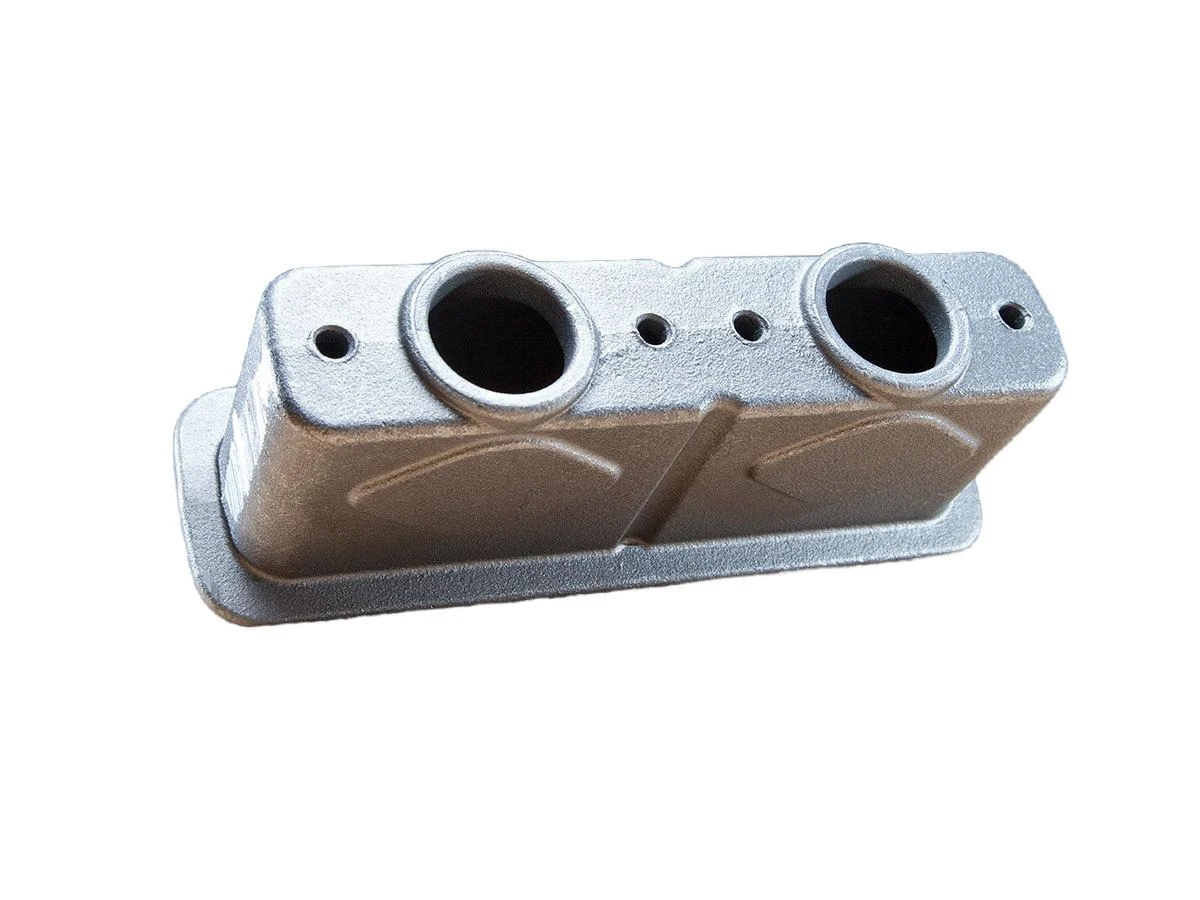
In the realm of die casting, the plunger holds the responsibility of injecting molten metal into the die cavity under high pressure. This process demands exceptional precision and durability, making the choice of plunger material and design paramount. Traditionally, plungers are made from high-quality steels or special alloys, renowned for their ability to withstand the harsh conditions within die casting machines. Expert manufacturers continually push the boundaries of material science, engineering solutions tailored to enhance performance and lifespan.
The importance of selecting the right plunger begins with understanding its role and the conditions under which it operates. A die casting plunger must handle extreme temperatures, substantial friction, and high pressures, all while maintaining accuracy in delivering molten metal into the mold. When companies invest in superior plungers, they mitigate risks such as premature wear, inconsistent shot sizes, and defects in cast products, enhancing overall productivity and reducing operational costs.
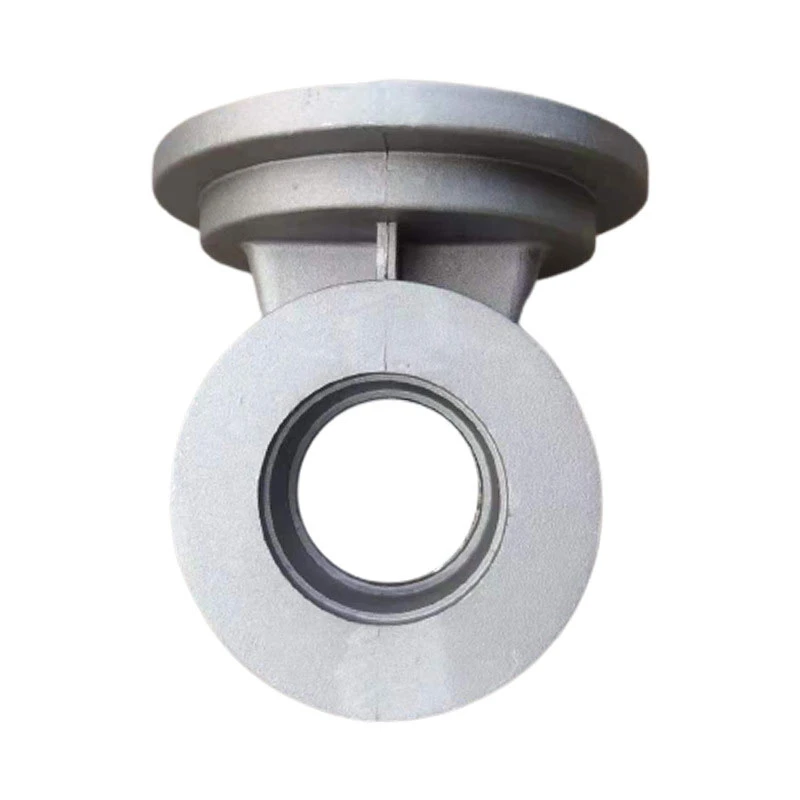
Leading manufacturers of die casting plungers prioritize precision engineering and rigorous testing. Each plunger undergoes comprehensive analysis, examining thermal expansion, wear resistance, and structural integrity. Collaboration with material scientists and engineers ensures a thorough understanding of how each material behaves under operational conditions, allowing for innovations such as introducing composite materials or advanced coatings. These modifications improve performance, offering increased durability and resistance to sticking or galling, a common challenge in die casting processes.
Trust in a supplier's expertise is further solidified by certifications and adherence to international standards. ISO certifications, for example, demonstrate a commitment to quality management, ensuring products consistently meet customer and regulatory requirements. Additionally, many reputable manufacturers provide comprehensive support services, from assisting with plunger selection to offering maintenance advice and troubleshooting. This partnership establishes a trust-based relationship, reassuring clients of ongoing support and product reliability.
die casting plunger
Efficiency in the die casting process is not solely reliant on the quality of the plunger but also on its compatibility with specific machines and molds. Customization becomes an advantage, with experts able to tailor the plunger’s design and composition to meet unique production needs. By optimizing parameters such as the plunger's shape, size, and surface treatment, manufacturers can reduce cycle times and improve the quality of cast products. This customized approach epitomizes expertise, as it requires a deep understanding of die casting dynamics and the ability to innovate solutions for complex challenges.
Monitoring plunger performance through data analytics is an emerging trend, offering another layer of expertise and authoritativeness. Advanced sensors and monitoring systems provide real-time data on plunger function and metal flow, enabling predictive maintenance and minimizing downtime. This technology forward approach elevates the trustworthiness of suppliers who can offer data-driven insights and continuous improvements to their products.
A community-driven approach strengthens the authoritative presence of plunger suppliers in the market. Engaging with industry forums, participating in conferences, and contributing to academic research establishes a dialogue with industry peers and clients. Sharing case studies of solved challenges or innovative processes not only demonstrates expertise but also positions companies as thought leaders in die casting technology.
Ultimately, the significance of die casting plungers transcends their function, embodying the principles of precision engineering, relentless innovation, and a commitment to quality. Selection of the right plunger is a decision embedded with trust, relying on the manufacturer's expertise and the authoritative assurance that products are designed to endure and perform. Building this trust requires a comprehensive approach combining engineering excellence, customer collaboration, and continuous enhancement, distinguishing leading suppliers as the authoritative voices in the die casting industry.