Die casting is a widely used manufacturing process that produces complex metal parts with high precision and repeatability. For manufacturers aiming to optimize the quality and efficiency of their production, understanding the critical parameters involved in die casting is crucial. A comprehensive grasp of die casting parameters not only enhances product quality but also positions your brand as an industry leader.
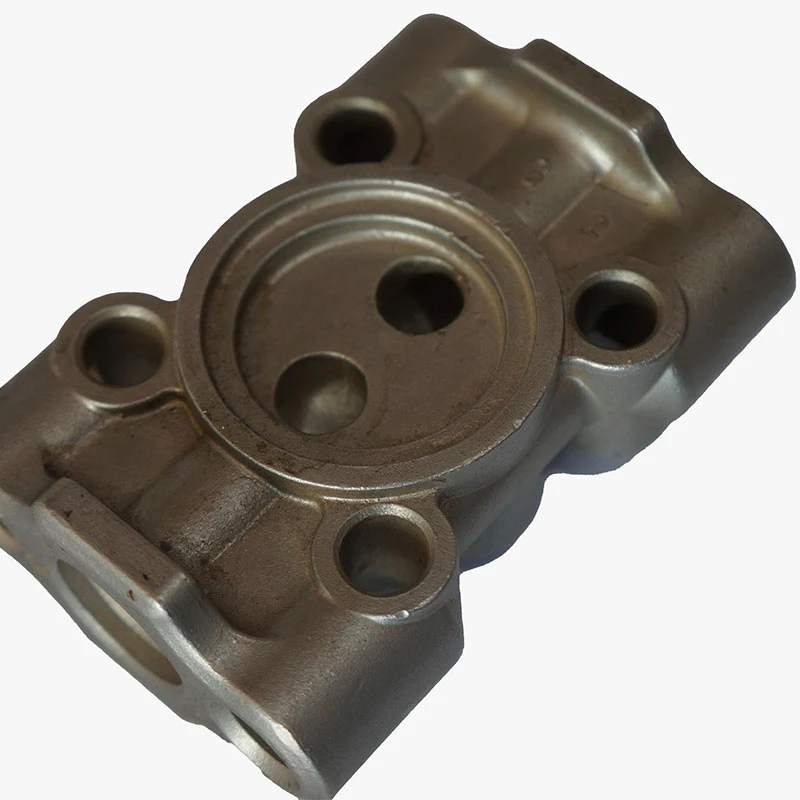
Temperature control is fundamental in die casting. Both die and molten metal temperatures have specific roles in determining the quality of the cast. Maintaining optimal die temperatures helps in reducing thermal shock, minimizes distortion, and prolongs die life. Similarly, ensuring the proper temperature of the molten metal reduces internal porosity and improves surface finish. Implementing advanced temperature control systems can lead to better cycle predictability and superior product quality.
Injection parameters significantly influence the final product's structural integrity and dimensional accuracy.
These parameters include shot pressure, velocity, and time. Setting the correct shot pressure ensures that the molten metal consistently fills the die cavity, reducing the occurrence of defects like air entrapment and cold shuts. Balancing shot velocity is also key, as it affects the metal's ability to fill complex geometries without causing turbulence or inconsistencies. Time management during injection further complements these efforts by ensuring that each phase is completed without compromising the material's properties.
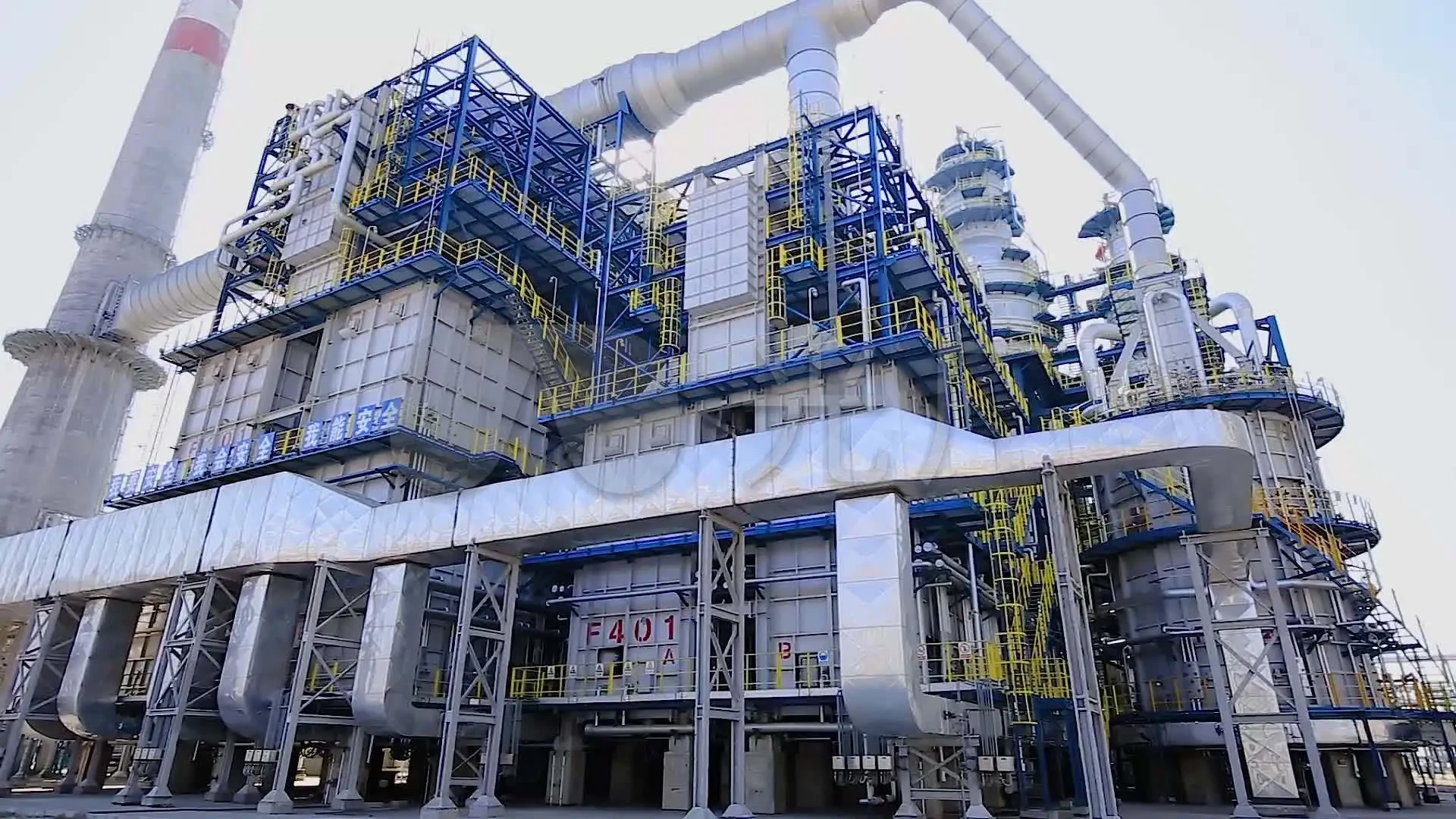
One must not overlook the intricacies of die design and material selection, which go hand-in-hand with die casting parameters. A well-engineered die minimizes defects and enhances production efficiency. Material selection impacts thermal conductivity and expansion rates, both of which are pivotal during the casting process. Choosing the appropriate steel grades and incorporating precision machining techniques can significantly improve die performance and longevity.
Pressure die casting parameters, such as clamping force and vacuum assistance, play instrumental roles in maintaining structural consistency and reducing defects. Clamping force must be correctly calibrated to avoid flash and to maintain the form of the part. Introducing vacuum assistance aids in eliminating air pockets, resulting in denser and more robust components. These practices underscore the importance of fine-tuning equipment and methodologies to accentuate product perfection.
die casting parameters
Lubrication is another vital parameter that ensures the smooth operation of die casting machinery and enhances the quality of the cast parts. Proper lubrication reduces wear and tear on the die and plunger, diminishes cycle time by facilitating quicker release, and enhances surface finish. Deploying cutting-edge lubricants or coatings could significantly amplify productivity and longevity of the molds.
Monitoring and analyzing die casting parameters through data-driven techniques further solidifies a company’s competitive edge. Employing real-time monitoring systems and analytics can lead to precise adjustments, reducing waste and optimizing energy consumption. By embracing Industry 4.0 technologies such as IoT-enabled sensors, manufacturers can anticipate equipment maintenance needs, thus avoiding unexpected downtimes.
Continuous training and expertise development of the workforce are paramount to harnessing the full potential of die casting parameters. Skilled operators and engineers should remain adept with the latest trends and technologies in die casting to maintain a high standard of quality and innovative spirit. Companies investing in education and certification programs demonstrate their commitment to excellence and leadership in the industry.
Ultimately, mastering die casting parameters is less about a set of numbers and more about understanding the symbiotic relationship between materials, design, and human input. For an enterprise, this mastery translates into delivering superior products, gaining an authoritative presence in the market, and establishing trust with clients, thereby solidifying its reputation as a true expert in die casting technology.