Sand casting design plays a crucial role in the manufacturing industry, offering a myriad of opportunities to create precise metal components. With its roots tracing back to ancient times, sand casting remains a popular choice due to its versatility and cost-effectiveness. Having spent years mastering the intricacies of this process, I can attest to its transformative power in producing high-quality products.
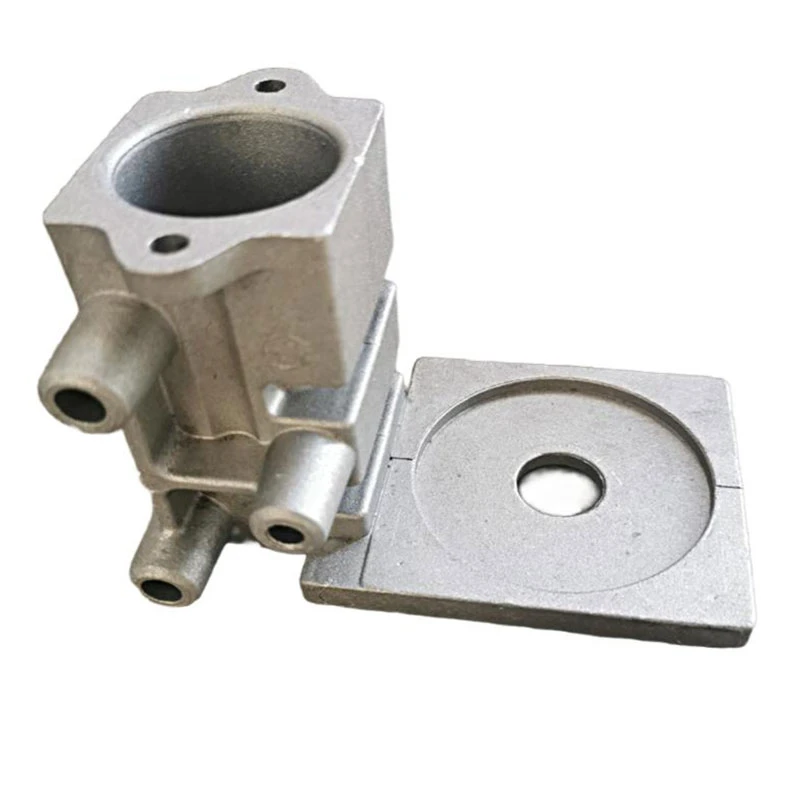
Drawing from my extensive experience, one of the first considerations in sand casting design is the selection of appropriate materials. The quality of the sand, bonding agents, and metals used significantly impacts the final product. I often emphasize the importance of using high-purity silica sand for its superior refractoriness and strength. In combination with the right binding agents, such as clay or chemical binders, this ensures robust mold integrity during the casting process.
Another pivotal aspect of expertise in sand casting lies in designing the mold itself. The mold must accommodate shrinkage and cooling, which are inherent to the casting process. Over the years, I've found that incorporating precise draft angles and fillets into the design can mitigate common defects such as cracks and warping. These design nuances not only enhance the structural integrity of the cast component but also streamline the mold removal process.
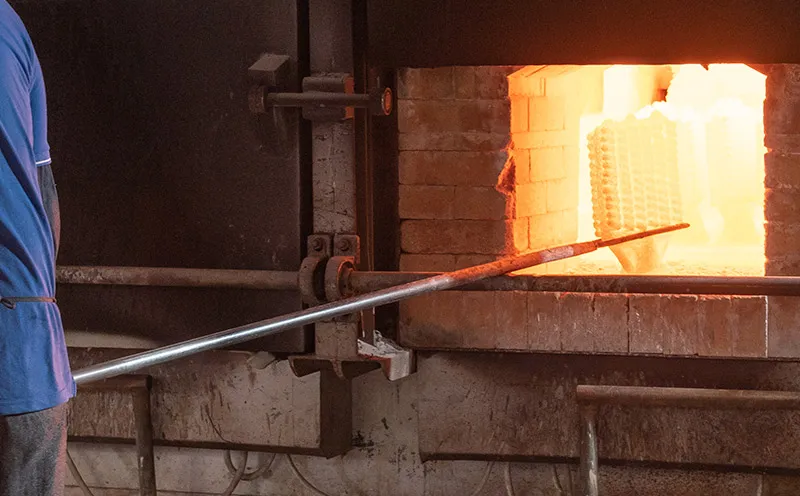
Authoritativeness in sand casting design is often demonstrated through the meticulous creation of core sections. Cores are essential for forming complex internal geometries within a casting. My approach is to use specialty core materials that withstand intense thermal and physical stresses during casting. Experience has taught me that precise core placement, secured by chaplets if necessary, ensures fidelity to design specifications, regardless of complexity. This authoritative handling of core sectioning sets a strong foundation for producing a flawless end product.
sand casting design
Trustworthiness in delivering quality sand cast components is built through rigorous testing and quality assurance protocols. Each cast piece must undergo thorough inspection for dimensional accuracy and material integrity. I've developed a keen eye for detecting discrepancies by employing techniques such as x-ray inspections and non-destructive testing. A commitment to quality assurance guarantees that each component meets or exceeds industry standards, reinforcing trust with clients.
Incorporating advanced technology into the traditional sand casting process has also been transformative. The utilization of computer-aided design (CAD) software enables precise simulation and analysis of the casting process, reducing the margin for error. Utilizing CAD in conjunction with 3D printing for mold and core creation enhances the precision and repeatability of cast components. This fusion of traditional craftsmanship with modern technology exemplifies the evolution of sand casting and underscores its authority as a manufacturing method.
Ultimately, sand casting design demands a blend of hands-on experience, technical proficiency, and continuous innovation. By embracing these principles and upholding these standards, sand casting continues to be a reliable and efficient method for producing intricate metal components. This enduring trust in sand casting is rooted in its consistent ability to deliver quality products that meet the diverse needs of industries worldwide.