Sand casting is a foundational process within the manufacturing sector, capable of producing a broad array of components with precision and adaptability. Exploring the intricate aspects of sand casting unveils its profound impact on industries ranging from automotive to aerospace. This traditional yet robust technique leverages granular materials to create complex geometric shapes, tailoring its applications to meet unique production demands.
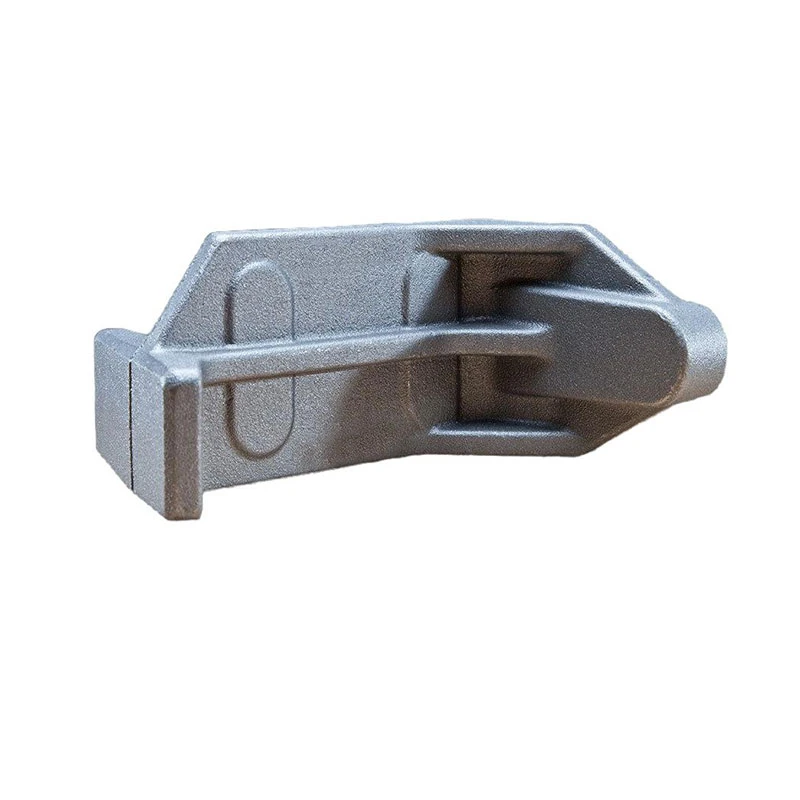
In the realm of product manufacturing, sand casting stands out for its versatility. It is engineered to accommodate a diverse selection of metals, including aluminum, iron, steel, and bronze, each offering distinct benefits. The process begins with the creation of a mold, typically crafted from silica sand due to its availability and physical properties. This sand is coated with a binding agent, often clay, which imparts durability and heat resistance to withstand the molten metal’s temperatures.
Expertise in sand casting is pivotal for optimizing product outcomes. One must consider the precise composition of the sand mixture, the type of binder used, and the intricacies of mold design. The latter includes the incorporation of sprues, gates, runners, and risers within the mold's design to facilitate the flow of metal and account for any volumetric shrinkage during cooling. It is these technical details that influence the quality, surface finish, and dimensional accuracy of the final product.
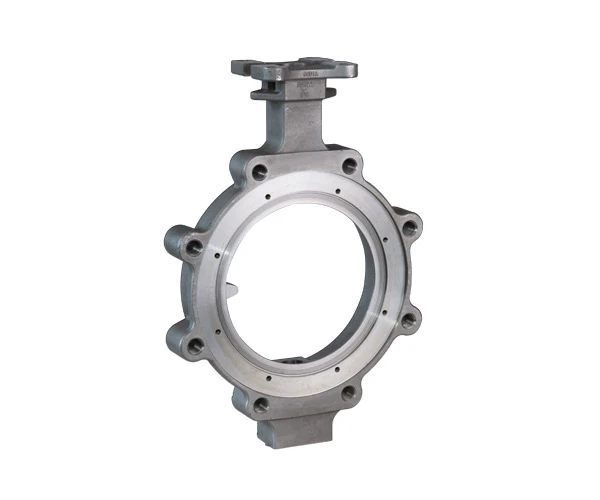
Operational experience is indispensable in sand casting to navigate the complexities and mitigate potential difficulties inherent in the process. Seasoned foundries prioritize controlling the parameters like moisture content in the sand, which can affect mold integrity and metal casting accuracy. Over time, they develop an intuition about the nuanced behaviors of different metal alloys during melting and solidification, adapting their methods to optimize performance and minimize defects such as porosity, inclusions, or misruns.
sand caster
The authoritativeness of established foundries and industry experts imbues confidence in sand casting as a reliable manufacturing process. These professionals often share their insights and case studies in trade publications and forums, contributing to a richer understanding within the industry. Their endorsement of best practices and innovative techniques fosters an environment of continuous improvement and knowledge exchange.
Trustworthiness in sand casting is reinforced through adherence to stringent quality assurance standards and certifications. From ISO compliance to industry-specific benchmarks, foundries are committed to maintaining high standards of quality and consistency. These standards not only ensure product efficacy but also instill trust among clients who rely on sand casting for critical components.
Looking towards the future, sand casting continues to evolve with advancements in technology. The integration of computer-aided design (CAD) and simulation tools offers unprecedented precision in mold and pattern design. Furthermore, the adoption of automation and robotics within foundries enhances production efficiency and reduces human error, further cementing the reliability of sand casting in producing high-quality components.
In conclusion, sand casting remains a cornerstone of modern manufacturing, celebrated for its versatility, reliability, and adaptability. By harnessing the collective experience, expertise, and innovations of industry professionals, this time-honored technique continues to set benchmarks for quality and performance across diverse sectors. As the technology advances, sand casting is poised to remain at the forefront of manufacturing solutions, a testament to its enduring significance and trusted reputation.