Precision cast plastic parts have revolutionized industries ranging from aerospace to consumer electronics. Their ability to be molded into intricate designs without the constraints seen in metal casting opens up a world of possibilities for engineers and designers. This article dives deep into the distinct advantages and applications of precision cast plastic components, affirming their pivotal role in modern manufacturing.
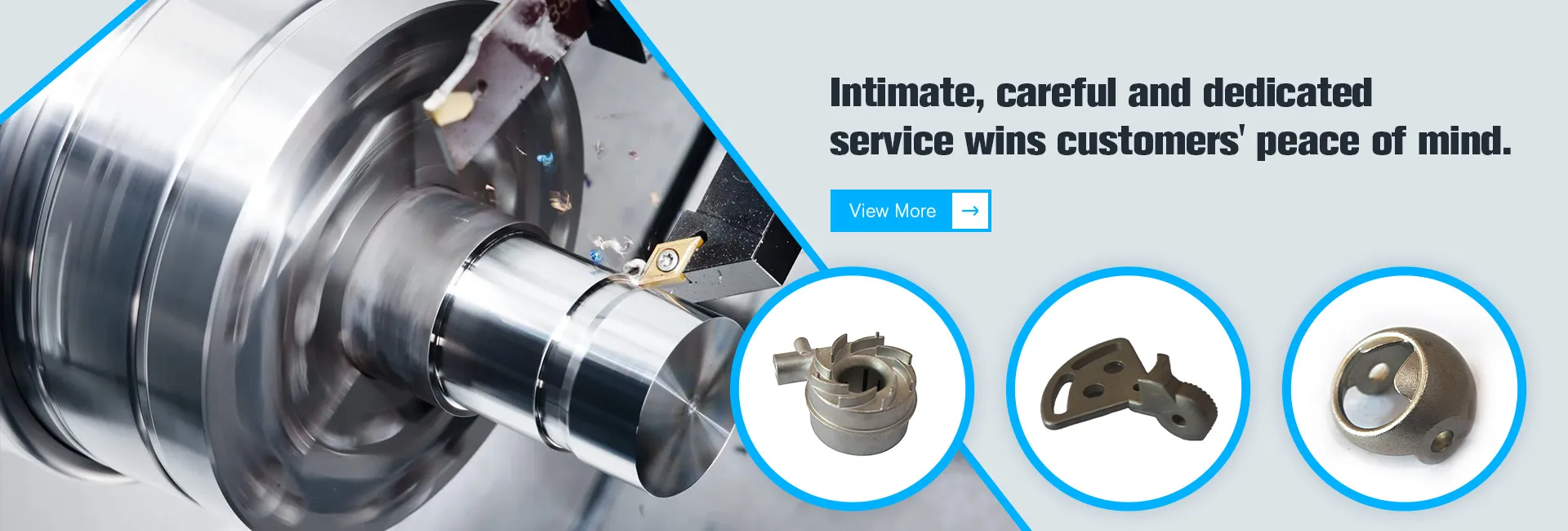
The journey begins with understanding what precision casting entails in the context of plastics. Unlike traditional plastic molding, precision casting allows for incredibly detailed and complex shapes that are often impossible to achieve with standard injection molding techniques. This is achieved through a meticulous process that starts with the creation of a mold, which is then filled with liquid plastic. Once solidified, the mold is removed, revealing a perfect replica of the desired part. The precision in this casting process is paramount, ensuring that every detail, from surface texture to dimensional accuracy, is reproduced to exact specifications.
Industries demanding high precision parts appreciate the inherent qualities of plastics—lightweight, corrosion resistance, and flexibility. In the aerospace sector, for instance, the reduction of even the smallest amount of weight can lead to significant fuel savings. Plastic components provide this advantage while still maintaining the rigidity and structural integrity required in flight-critical applications. Similarly, in electronics, the insulating properties and thermal resistance of certain plastic materials make them ideal for housing delicate circuitry without hindering performance.

Moreover, the scope of materials available for casting is extensive, allowing manufacturers to select plastics that best fit the technical requirements of their products. High-performance polymers like PEEK, with its exceptional temperature stability and strength, exemplify the advanced materials used in precision plastic casting. This not only optimizes the functionality of a part but also enhances its lifespan and cost-effectiveness compared to traditional materials.
precision cast plastic parts
Experience with precision cast plastic parts reveals a remarkable reduction in production costs and lead times. The casting process eliminates many labor-intensive steps associated with machining metal parts, such as multiple milling stages or the assembly of smaller components. As a result, the time from design to finished product is significantly decreased, giving companies a competitive edge in rapidly evolving markets. The efficiency gains are further amplified when considering large-volume production runs, where the economies of scale fully leverage the cost benefits of plastic casting.
From an expertise perspective, manufacturers involved in precision casting are continuously pushing the boundaries of what plastics can achieve. By investing in cutting-edge equipment and research, these companies are able to produce components with tolerances and qualities that were once thought unattainable. This expertise fosters innovation across industries, enabling designers to realize concepts that were previously limited by material constraints.
Trustworthiness and authoritativeness are cemented through rigorous testing and quality assurance protocols. Precision cast plastic parts undergo extensive scrutiny to ensure they meet regulatory standards and customer expectations. Reputable manufacturers pride themselves on their certifications, such as ISO standards, which validate their commitment to quality and reliability. This dedication to excellence reassures clients that their products will perform as intended in critical applications.
In conclusion, precision cast plastic parts offer unparalleled advantages in modern manufacturing, cutting across a diverse spectrum of applications. Their ability to deliver complex designs with consistent quality, reduced weight, and cost-effectiveness makes them indispensable in today’s innovative landscape. As industries continue to evolve, the role of precision cast plastics will undoubtedly expand, driving forward new advancements and possibilities.