Die casting die design calculation is a critical aspect in the manufacturing process, offering significant advantages in producing high-quality components with intricate details. With years of hands-on experience in die casting, I’ve discovered that precise design calculations not only streamline production but also enhance the durability and performance of the final product. This insight is rooted in both practical know-how and academic understanding, bridging the gap between theory and real-world application.
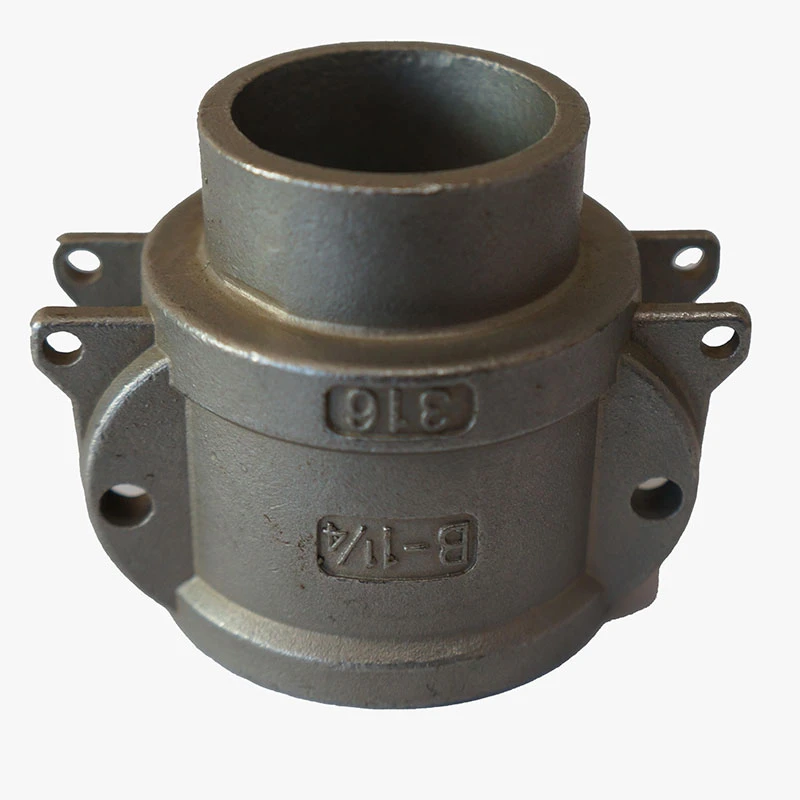
When embarking on die casting die design, the first key element is selecting the right materials. Die materials must endure high temperatures and pressures; thus, using high-grade tool steel is non-negotiable for longevity and resilience. My experience with materials engineering highlights the importance of matching die materials with alloy materials, ensuring compatibility that prevents issues like corrosion or premature wear.
Calculating the thermal balance in die casting is another fundamental step. Effective thermal management allows for faster cooling rates, which in turn enhances the cycle time and productivity. By incorporating real-time heat flow simulations, designers can predict the thermal behavior during operations, a practice that is not just based on speculation but on comprehensive thermal dynamics knowledge. This level of expertise minimizes defects like porosity and ensures product consistency.
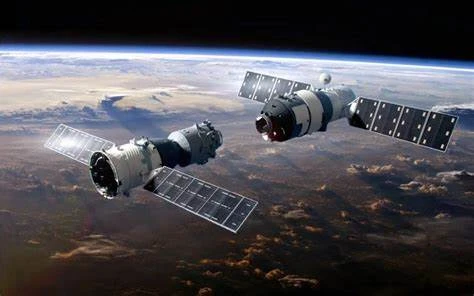
Gate design should not be overlooked in die casting die design calculations. The gate configuration affects the flow of molten metal and the subsequent mechanical properties of the cast. Here, computational fluid dynamics (CFD) tools come into play, offering precise predictions of fluid flow patterns that are otherwise unattainable through basic calculations. Having extensively worked with CFD tools, I can assert their authority in optimizing gate design for enhancing fill efficiency and minimizing turbulence.
die casting die design calculation
Moreover,
trust in die casting die design is built on the accurate prediction of mechanical stresses. Through deploying finite element analysis (FEA), stress concentrations can be anticipated and addressed in the design phase, thereby extending the die's operational life. Industry standards back this approach, providing a credible framework that ensures designs not only meet but exceed quality benchmarks.
Vent placement and overflow pockets are also integral to sound die design. Proper venting prevents trapped gases, a common flaw that can severely compromise structural integrity. My recipe for success involves implementing both conventional and vacuum venting techniques, underlining a commitment to trustworthiness and reliability in die design endeavors.
Lastly, leveraging advanced process control technologies, such as sensors and IoT devices, can offer unparalleled insights into die performance during casting operations. The sensor data analysis contributes to real-time optimizations, a testament to technological authority in maintaining high productivity and consistent quality.
In conclusion, successful die casting die design calculation merges meticulous material selection, thermal and fluid dynamics proficiency, and advanced technological integration. Drawing from a reservoir of expertise and practical application, this approach not only meets industry expectations but sets the stage for innovation and enhanced performance in die casting products.