In the world of manufacturing, die casting has long been heralded as a go-to process for crafting intricate and robust components. Central to this process are die casting cores, which play a pivotal role in achieving the desired geometric intricacies in products. These cores are not merely a component; they are the linchpins of sophisticated design and precision engineering.
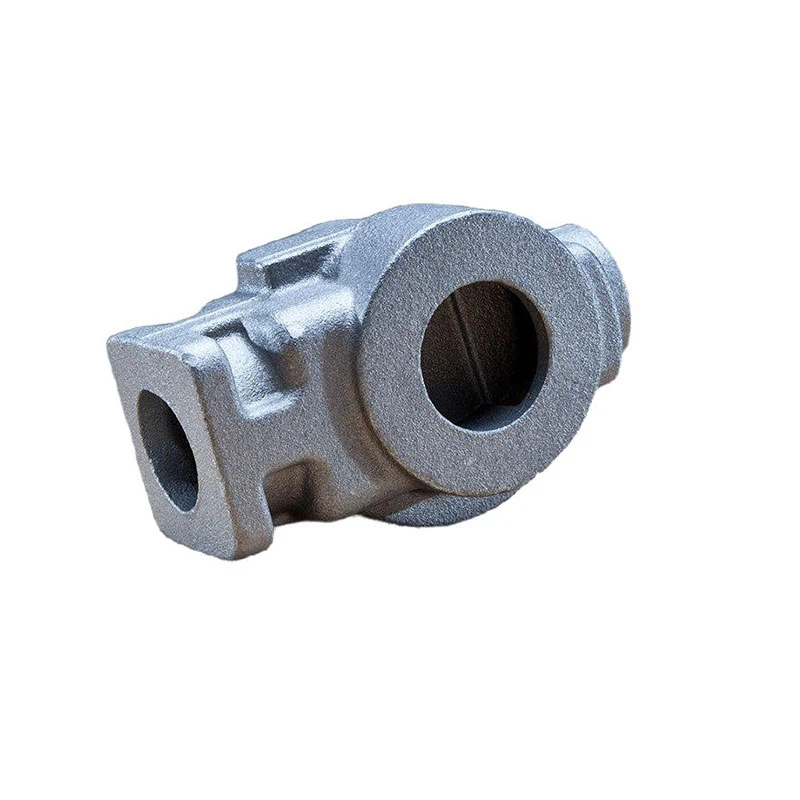
Understanding die casting cores begins with grasping their purpose. Essentially, a core is a piece that is inserted into the mold to shape the internal cavities of a die casting. This crucial element allows manufacturers to produce complex shapes that would otherwise be impossible or prohibitively expensive with traditional machining techniques. The core can be made from the same metal as the casting, or from another material entirely, depending on the requirements of thermal conductivity and structural soundness.
Expertise in die casting core design is indispensable for ensuring product excellence. The design and material selection for these cores directly impact the cooling rate and the ultimate structural integrity of the final product. Professionals with years of experience understand that the balance between material choice and design intricacies must be maintained to prevent common casting defects such as porosity or misruns. For example, in intricate aluminum die castings, the use of ceramic cores might be preferred due to their superior resistance to thermal expansion, ensuring dimensional stability during the casting process.
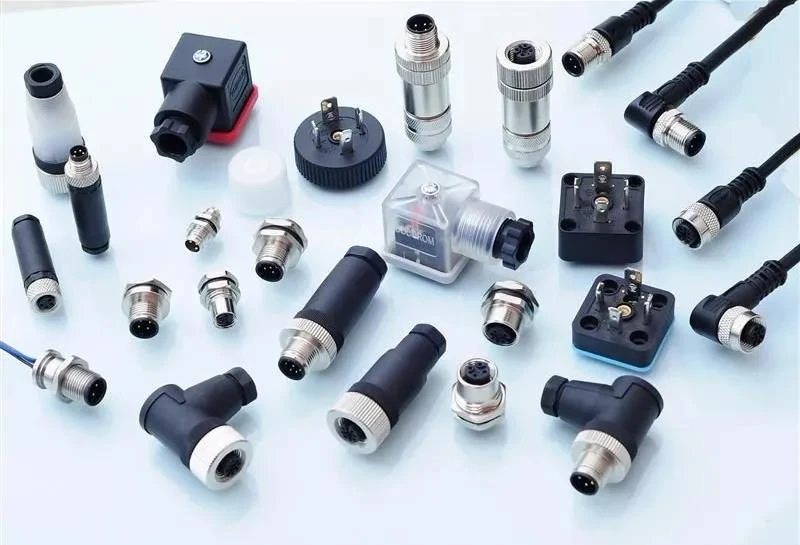
Authoritative sources in the industry repeatedly emphasize the role of technological advancements in refining core design and production. Innovations such as 3D printing for core manufacturing have revolutionized how quickly and precisely these components can be made. The ability to produce complex geometrical forms with a high degree of accuracy allows manufacturers to experiment with new designs and bring products to market faster than ever before. From automotive to aerospace applications, the integration of AI and machine learning in design processes is helping experts predict performance outcomes and enhance core reliability.
die casting core
Trustworthiness in the manufacture and application of die casting cores is ensured through adherence to stringent industry standards and quality checks. Reputable manufacturers implement rigorous testing and quality assurance processes to ensure that each core meets specific thermal and structural requirements. Certifications such as ISO 9001 and adherence to international die casting standards reflect a commitment to maintaining high-quality manufacturing processes.
From an experiential perspective, professionals in the field acknowledge that die casting cores are not without their challenges. Real-world application frequently involves troubleshooting issues such as core breakage during ejection or difficulty in maintaining core alignment during the casting process. Through hands-on experience, experts have devised best practices to mitigate these issues, such as optimizing ejection force parameters or improving alignment fixtures in molds.
In conclusion, die casting cores are fundamental to the success and advancement of die casting methods.
Their design and material composition are critical to product integrity and performance. The continued evolution of core production technologies promises to further enhance the efficiency and capabilities of the die casting industry. Manufacturers who master the intricacies of die casting core design will continue to pave the way in delivering high-quality, innovative products across various sectors, maintaining a competitive edge in the burgeoning industrial landscape.