Aluminium casting parts have become an integral component in various industries due to their exceptional qualities and versatility. When it comes to manufacturing processes and material selection, industry professionals often turn their attention to aluminium. This metal's unique properties make it an ideal choice for casting parts that demand precision, durability, and cost-effectiveness.
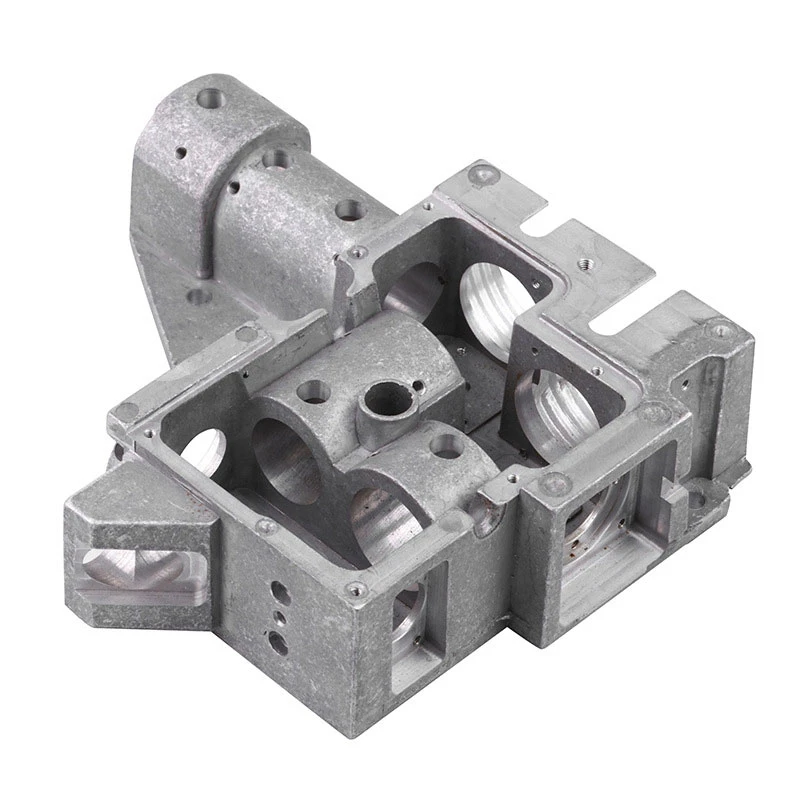
One of the primary advantages of aluminium casting parts is their remarkable strength-to-weight ratio. In industries such as automotive, aerospace, and consumer electronics, reducing weight while maintaining structural integrity is crucial. Aluminium provides the ideal solution. It is significantly lighter than other metals, such as steel, making it the preferred material for components where weight reduction contributes to fuel efficiency, improved performance, and enhanced user experience.
Moreover, aluminium casting parts boast excellent corrosion resistance. This characteristic ensures that components remain durable and perform reliably in harsh environments, including marine applications and outdoor settings. Manufacturers trust aluminium for its longevity and ability to withstand the rigors of various conditions, without compromising on functionality.
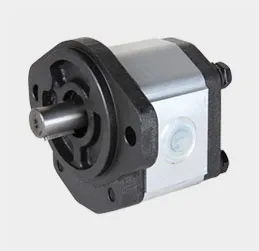
Flexibility in design is another factor that sets aluminium casting parts apart from alternatives. The malleability of aluminium allows manufacturers to create intricate shapes and complex geometries that might be difficult or costly to achieve with other materials. This flexibility not only aids in optimizing product design but also streamlines the manufacturing process, resulting in reduced lead times and overall cost savings.
aluminium casting parts
The expertise involved in aluminium casting cannot be overstated. Reputable producers often employ advanced techniques such as pressure die casting, sand casting, and investment casting to meet specific requirements. These methods are chosen based on the application, desired finish, and complexity of the part. Skilled engineers and metallurgists evaluate each project meticulously to ensure the highest standards of quality and precision are met.
Authoritativeness in the field of aluminium casting parts stems from the continued research and development efforts by leading manufacturers and industry associations. Their commitment to innovation drives the enhancement of casting technologies and the development of new alloys. Trust in aluminium casting parts is fortified by rigorous testing and certification processes, ensuring compliance with international standards and regulations.
End-users can rely on the credibility of producers with a proven track record of delivering high-quality casting solutions. Manufacturers equipped with state-of-the-art facilities and a deep understanding of the metallurgy behind aluminium casting are better positioned to offer products that meet the evolving demands of the modern market.
In summary, aluminium casting parts represent a blend of strength, durability, and design flexibility that appeals to a wide range of industries. Backed by expertise, authoritativeness, and trustworthiness, these components continue to play a vital role in advancing technology and engineering solutions across the globe. By choosing aluminium, manufacturers not only benefit from its inherent qualities but also align themselves with a material that supports innovation and long-term sustainability.