Lost wax precision casting, a centuries-old technique, continues to be a cornerstone in modern manufacturing, combining both artistry and engineering precision to produce intricately detailed metal components. This versatile method, known for its ability to achieve near-net-shape results, plays a vital role in various industries, providing engineers and designers unparalleled freedom in component design and material choice.

One of the remarkable advantages of lost wax precision casting is its capability to create complex geometries with meticulous detail. By using wax patterns which are made in the exact shape of the desired component, manufacturers are able to achieve exceptional detail and surface finish. This is a game changer for sectors such as aerospace and automotive, where the precision and intricacy of each part directly affect the overall performance and safety of the machinery. For instance, turbine blades in high-performance engines are often cast using this method, ensuring each blade meets exacting aerodynamic and structural requirements.
The expertise required in lost wax precision casting extends from pattern making to the final casting process.
Skilled artisans in pattern-making meticulously create wax models that serve as the blueprint for casting. These models are then coated with a refractory ceramic material that is hardened and heated, causing the wax to melt away, or be lost, hence the name of the process. The void left by the melted wax is then filled with molten metal. The expertise needed to handle these processes is crucial, as any slight deviation can lead to defects in the final product. This necessity for precision has spurred the development of specialized training programs and certifications, ensuring that craftsmen and engineers have the skills required to meet the high demands of industries reliant on these components.
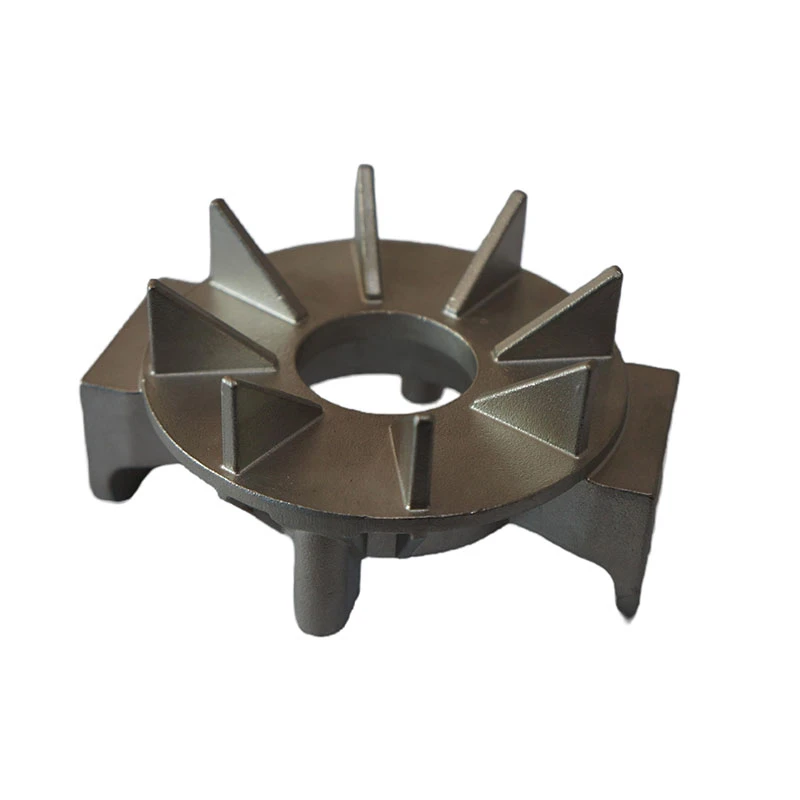
Furthermore, the authority of lost wax precision casting in the manufacturing domain is bolstered by its adaptability across a wide range of materials. Meticulous control of the casting process allows for the use of various metals, including but not limited to steel, aluminum, titanium, and superalloys. Each material offers distinct advantages based on its application. For example, titanium is often used when a combination of light weight and high strength is required, a common need within the medical and aerospace sectors. This adaptability underscores the versatility of the process and its relevance in cutting-edge technological applications.
lost wax precision casting
Trustworthiness in the process is enhanced by rigorous quality control measures that ensure reliability and consistency in the final products. Each stage of the casting process is monitored and tested, from the inspection of the raw materials to in-depth evaluations of the final components. Non-destructive testing methods, such as X-ray and ultrasonic inspection, are routinely employed to detect internal defects that might compromise integrity. These stringent quality assurance protocols are vital for maintaining the trust of sectors that depend on components manufactured to exacting specifications, such as in nuclear power and defense industries.
In addition to precision and quality control, sustainability is becoming an important consideration in lost wax precision casting. The industry is increasingly integrating environmentally friendly practices, such as the recycling of wax and the use of less energy-intensive furnaces. These advances not only reduce the environmental footprint of the casting process but also adhere to emerging regulatory standards geared towards sustainable manufacturing.
For manufacturers and industries that require precision and reliability, lost wax precision casting offers a tried-and-true method supported by years of refinement and technical advancement. The process exemplifies how traditional manufacturing techniques can evolve and adapt to meet modern challenges, providing a reliable pipeline of components vital for innovative and advanced applications. From improving aerodynamics in automobiles to advancing medical implant technologies, lost wax precision casting continues to be an indispensable tool for engineers and designers striving for excellence in complex component fabrication. This confluence of tradition and technology ensures the continued relevance and authority of the process in the ever-evolving landscape of global manufacturing.