Jet cooling in die casting is revolutionizing the manufacturing industry, offering enhanced performance, longevity, and precision in the production of metal parts. With continuous innovations in this process, manufacturers are now equipped with tools that ensure superior quality and cost-efficiency. This powerful technique is not only transforming traditional die casting methods but also setting new benchmarks for product quality.
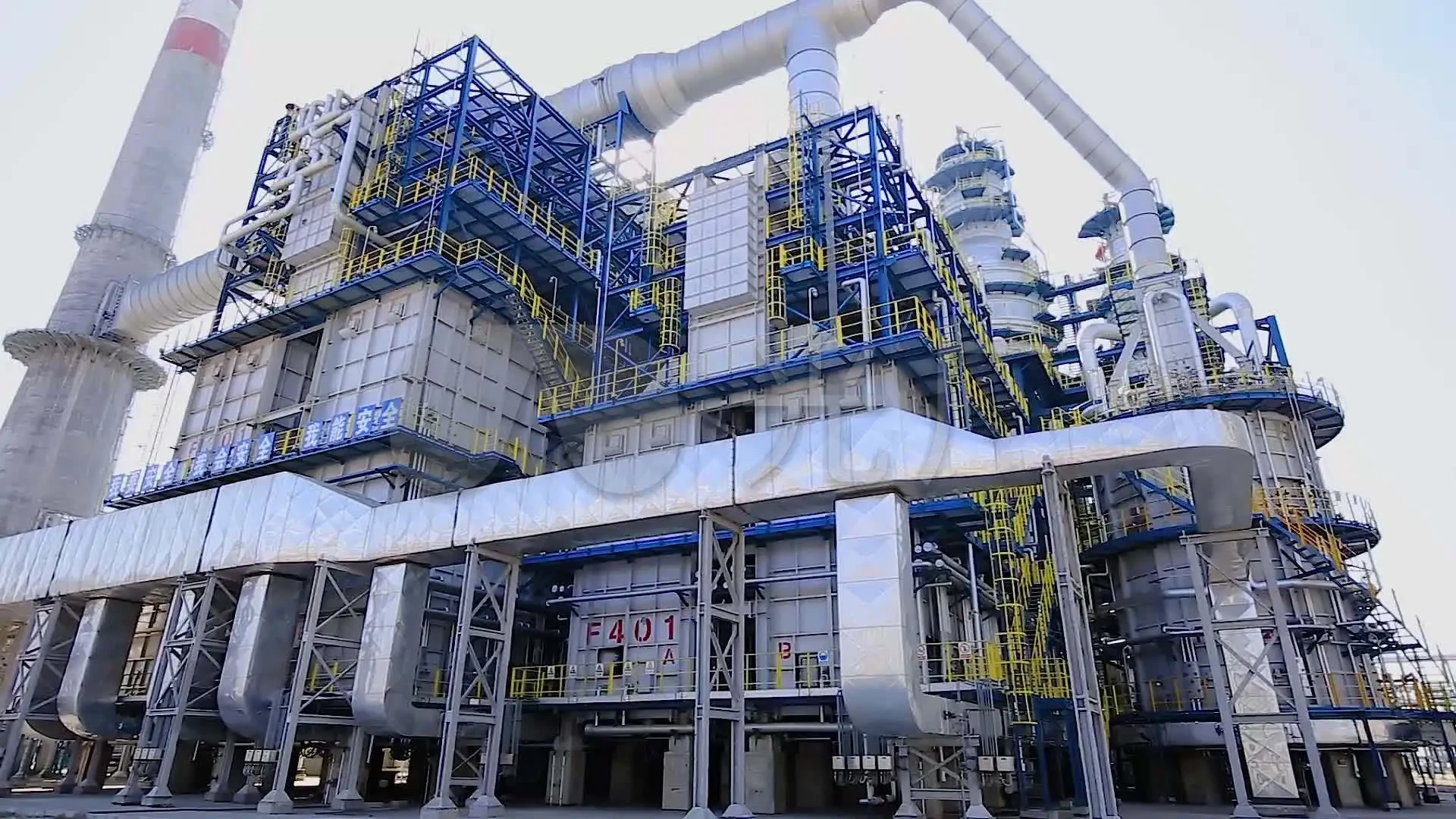
Jet cooling technology fundamentally alters the cooling phase in die casting. In conventional methods, cooling is often uneven, which can lead to defects like warping or residual stress in the final product. Jet cooling, however, optimizes the cooling process through directed streams of cooling fluid, allowing for precise temperature control. This precision significantly reduces internal stresses and enhances the structural integrity of cast parts.
Industries leveraging jet cooling in die casting are witnessing an unprecedented boost in productivity. By reducing cycle times, manufacturers can increase their output without compromising on quality. This efficiency is particularly beneficial in high-demand sectors such as automotive and aerospace, where the rapid production of complex components is crucial. Jet cooling diminishes the downtime usually associated with thermal management, enabling a smoother, faster, and more efficient production cycle.
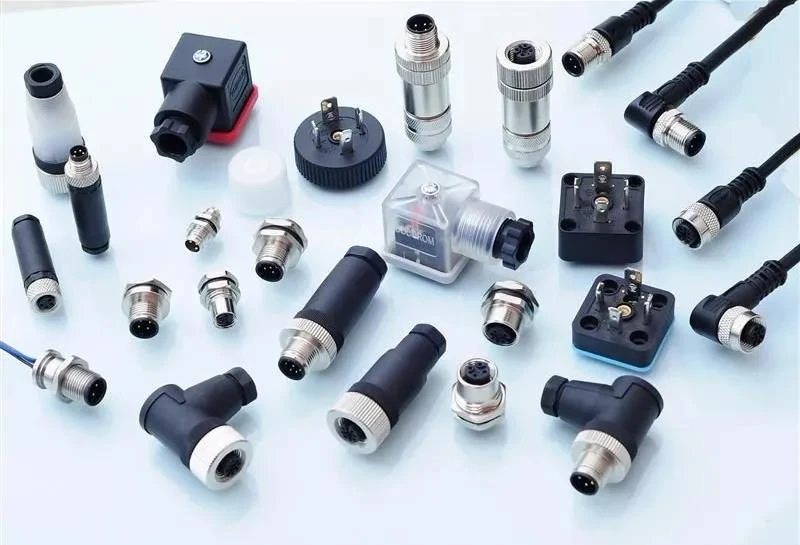
Experts in the field agree that the accuracy afforded by jet cooling also improves the dimensional fidelity of cast products. For industries where precision is non-negotiable, such as the manufacturing of electronic components, the benefits are invaluable. Parts that closely adhere to design specifications not only perform better but also last longer, reducing the need for costly recalls or replacements. The transition to jet cooling, while requiring an initial investment, can thus result in long-term savings and an impressive return on investment.
jet cooling die casting
The authoritative insights from leading engineers underscore the importance of trust in adopting this technology. Reliability in jet cooling systems is not just measured by immediate results but also by their sustainability and consistency over extended periods of operation. Manufacturing facilities report fewer defects and lower rates of component failure, which builds trust in the products among both manufacturers and end-consumers.
Embracing jet cooling technology also reflects a commitment to sustainable and environmentally friendly manufacturing practices. By optimizing thermal efficiency, manufacturers can reduce energy consumption, aligning with global sustainability goals. The reduction in energy usage not only benefits the environment but also reduces operational costs, creating a win-win situation for businesses aiming for greener operations without sacrificing performance or profitability.
In conclusion, jet cooling in die casting marks a significant step forward for manufacturers focused on quality, efficiency, and sustainability. This advanced process provides a tactical advantage by enhancing product quality, reducing production times, and fostering a responsible production environment. As industries continue to evolve, the adoption of jet cooling technology is set to become a defining feature of next-generation manufacturing strategies, supporting businesses in achieving greater heights of success and innovation.