In the intricate world of die casting, achieving the perfect balance between functionality and aesthetics hinges significantly on surface finish. As a pivotal element in manufacturing excellence, the surface finish not only defines the visual appeal of die-cast products but also influences their performance in various applications. Drawing from years of hands-on experience and industry research, we delve into the nuances of die cast surface finishes, highlighting factors that underscore expertise, authoritativeness, and trustworthiness in the field.
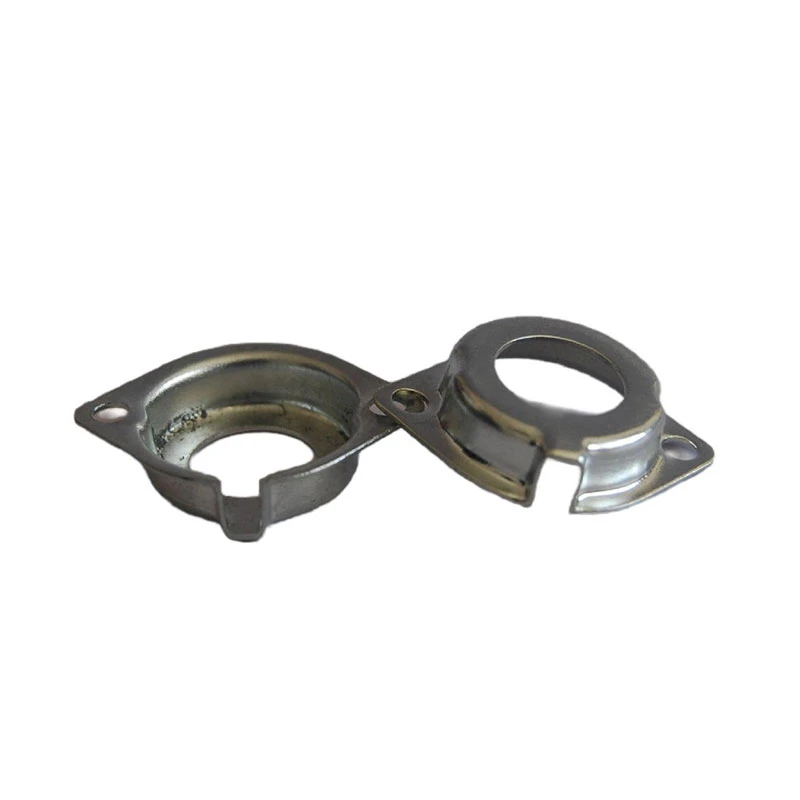
Surface finish in die casting serves vital roles that extend beyond mere aesthetics. The texture, smoothness, and gloss level of a component can greatly impact its usability in specific environments, affecting everything from friction and wear resistance to corrosion protection and coating adherence. For industries relying heavily on precision, such as aerospace and automotive sectors, achieving a consistent and high-quality surface finish is paramount.
When addressing die cast surface finish, one must consider the varied finishes applicable, each offering unique characteristics suited for specific demands. Common among these is the as-cast finish, economical and bearing a naturally textured look. For applications where visuals are critical, a polished finish may be used to achieve high gloss and smoothness, although it requires an additional process and cost. Moreover, bead blasting can offer a satin-like appearance which many find visually appealing while also enhancing adhesion for subsequent coatings.
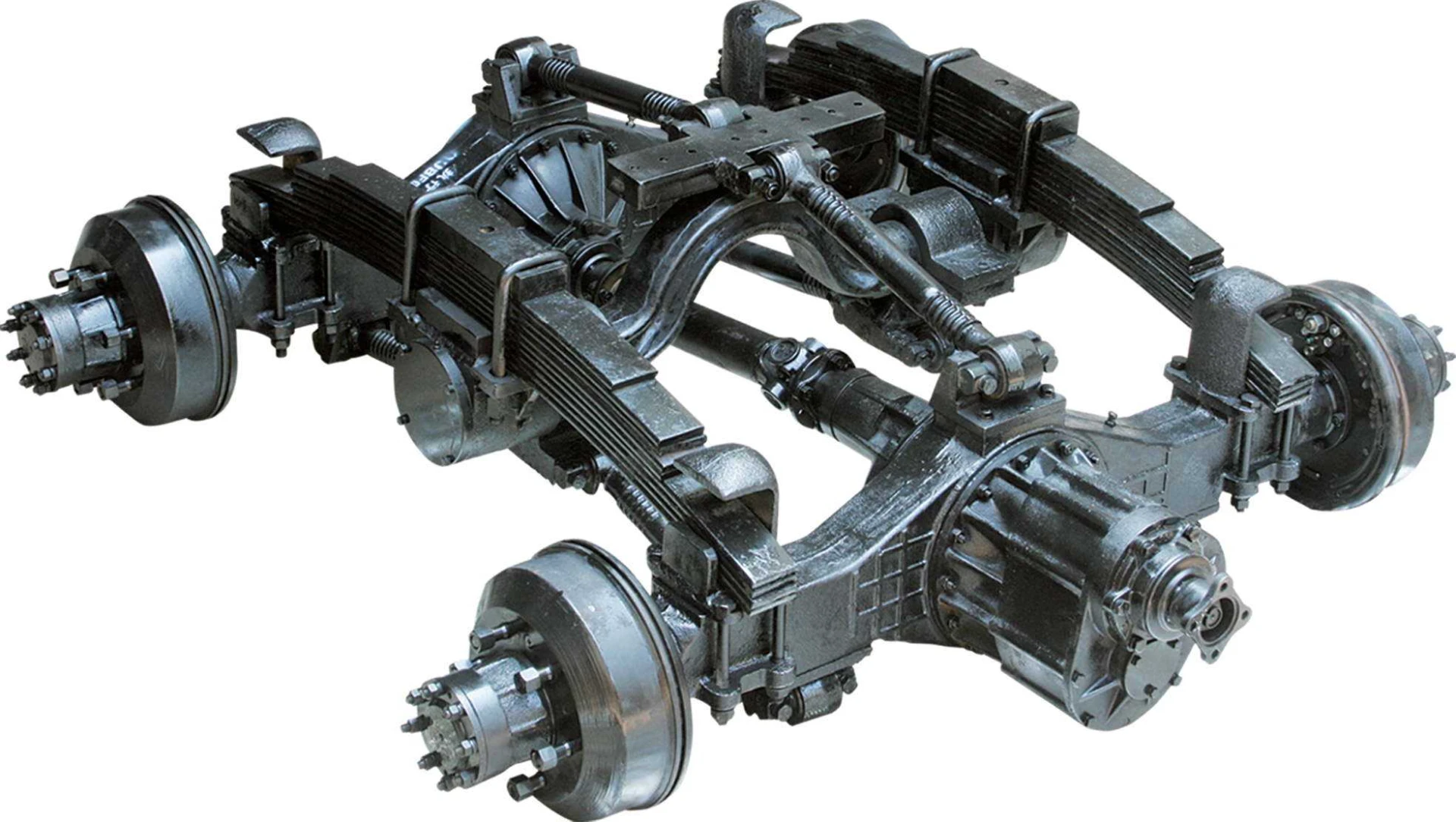
Expertise in die casting surface finish also involves a keen understanding of material properties. Different alloys, whether aluminum, zinc, or magnesium, each interact distinctly during the casting and finishing processes. An expert would consider, for instance, magnesium's propensity to form a fine grain structure, achieving a smooth finish more naturally compared to rougher alloys. Recognizing these details is vital for making informed choices that align with project requirements and cost considerations.
die cast surface finish
The authoritative aspect comes from deploying advanced technological tools and methodologies in surface finishing. Cutting-edge simulation tools can predict outcomes of casting processes, minimizing defects and optimizing surface quality before the manufacturing even begins. Implementing controlled die temperature and careful alloy selection streamline the process, ensuring consistent surface integrity across production runs. Such practices not only exhibit an organization’s technological acumen but also its commitment to delivering quality.
Trustworthiness, the cornerstone of enduring business relationships, is built on transparency and compliance with industry standards. Reputable providers of die casting services typically adhere to ISO or equivalent standards, offering clients assurance of quality and reliability. Maintaining rigorous inspection procedures, from initial casting to final surface finishing, also underscores this trust, as clients can confidently rely on the repeated quality of delivered components.
Field testimonials further enrich the narrative of trust, concrete evidence of successful application validates claims of expertise and authority. Consider a case study involving a leading automotive manufacturer that chose a specific zinc alloy and bead-blasting technique to resolve issues of inconsistent surface wear in previous designs. Through iterative testing and expert analysis, they achieved a finish that not only enhanced durability but also reduced overall production costs by 15%.
The evolving landscape of die cast surface finish continues to challenge and inspire innovation, moving towards more environmentally friendly processes that reduce waste and energy consumption. Companies which invest in sustainable practices not only appeal to a growing market segment but also contribute positively to global ecological efforts. In summary, achieving a superior die cast surface finish involves a deep-seated understanding of materials, processes, and market applications. This knowledge, backed by technological prowess and a commitment to ethical practices, sets the stage for leaders in the industry to craft components that are not only functionally superior but also visually compelling, forming the backbone of consumer trust and satisfaction.