Die casting design is a critical focus in manufacturing, playing a pivotal role in determining the quality, functionality, and durability of the final product. As an authority in this domain, leveraging my extensive experience, I offer a detailed exploration of the principles, challenges, and strategies that underpin successful die casting design.
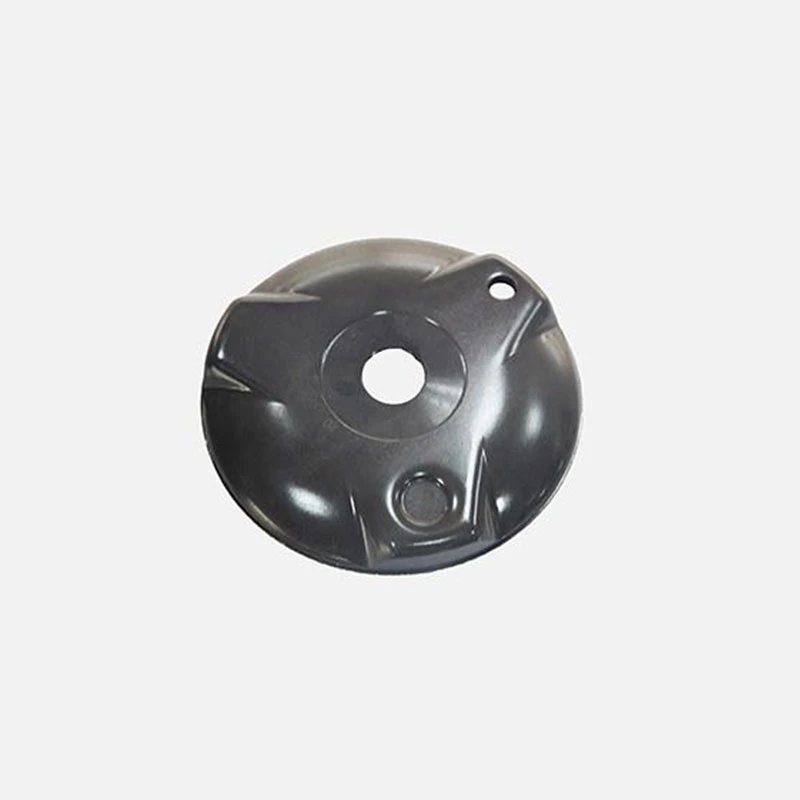
Die casting involves injecting molten metal into a mold cavity under high pressure. The precision of this process is fundamentally rooted in meticulous design, as it directly impacts the product's structural integrity and aesthetic appeal. A comprehensive understanding of material properties and flow dynamics is essential when designing for die casting to ensure optimal performance and minimal defects.
The selection of materials is a cornerstone of effective die casting design. Aluminum, magnesium, and zinc are the most commonly used alloys, each offering distinct benefits. Aluminum is prized for its lightweight nature and excellent corrosion resistance, making it suitable for automotive and aerospace applications. Magnesium, being the lightest structural metal, provides a remarkable strength-to-weight ratio, ideal for electronics and portable devices. Zinc, meanwhile, offers high ductility and impact strength, making it perfect for intricate, high-precision components.
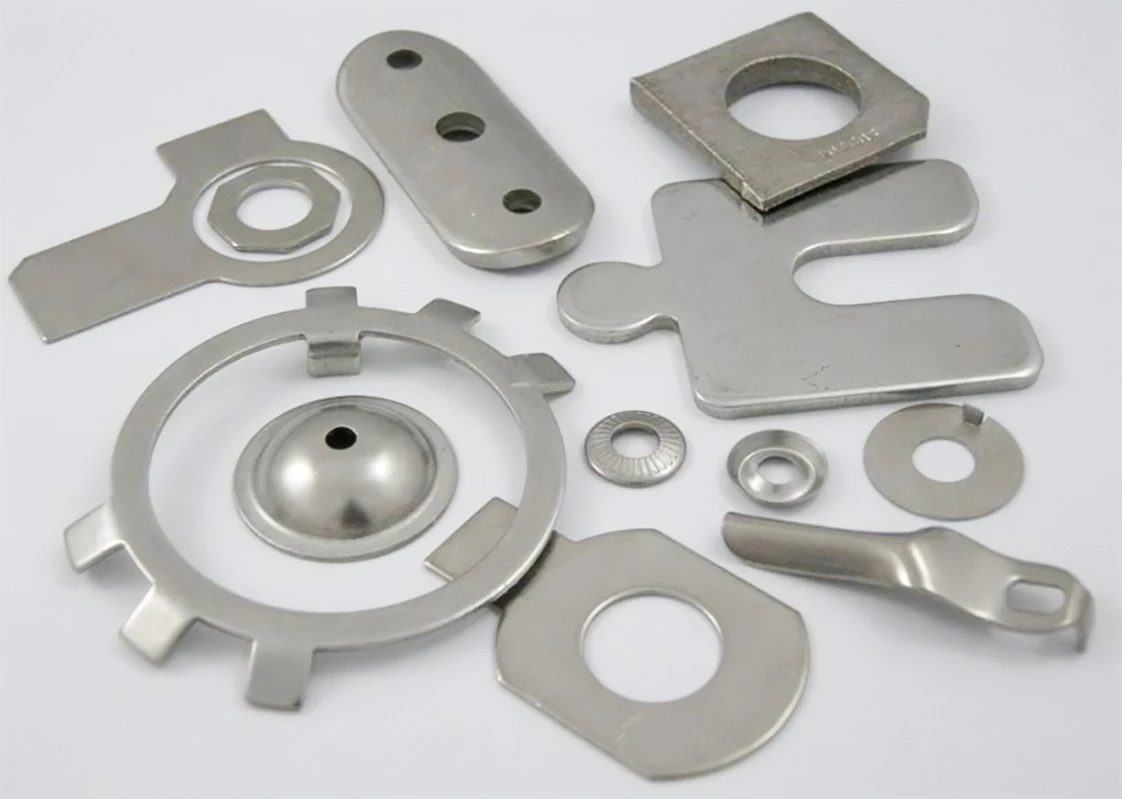
A crucial element in die casting design is the development of draft angles. These slight slopes facilitate the easy removal of the cast part from the mold, reducing the likelihood of damage. Too steep a draft can increase material usage unnecessarily, whereas too shallow a draft may result in the part sticking in the mold, thereby compromising production efficiency.
Gate and runner system design is another area requiring meticulous attention. These pathways guide the molten metal into the mold cavity and must be configured to ensure a smooth, turbulence-free flow. An improperly designed gate can lead to air entrapment, cold shuts, or even incomplete fill, all of which critically impact the quality of the final product.
die casting design
Vent and overflow design are integral in preventing defects. Vents allow trapped air and gases to escape during the injection process, averting unwanted porosity. Overflows, meanwhile, serve to collect the first metal to enter the cavity—typically cooler and less homogeneous—ensuring that only the hottest, most uniform metal fills the critical areas.
Post-casting processes also inform die casting design strategies. Considering aspects such as machining, plating, and painting during the design phase can significantly enhance efficiency and reduce costs. Incorporating features that accommodate these processes, such as extra material for machining or smooth surfaces for plating, can preemptively eliminate challenges downstream.
Simulation software has become an invaluable tool in the design phase, enabling virtual testing of mold designs before physical prototypes are created. By simulating the flow of molten metal, potential problems such as hotspots, air pockets, and thermal imbalances can be identified and corrected early, reducing the time and cost associated with trial-and-error methods.
Die casting design necessitates a balance between theoretical knowledge and practical application. Close collaboration between designers, engineers, and toolmakers is essential to refine designs and address potential manufacturing challenges. This collaborative approach not only enhances the technical aspects of design but also aligns the team with the strategic objectives of production, ensuring that the final product meets all specified requirements.
To conclude, die casting design is a nuanced and complex discipline, demanding expertise, precision, and foresight. By understanding and integrating fundamental principles with advanced technologies and collaborative practices, manufacturers can optimize product quality, enhance production efficiency, and maintain a competitive edge in the marketplace.