The cold die casting industry stands as a critical player in the production of high-quality metal components for various industrial applications. As an experienced authority in SEO content creation, the focus here is to delve deep into the intricate world of cold die casting, highlighting its unique characteristics, benefits, and the unparalleled trust it commands within the manufacturing sector.
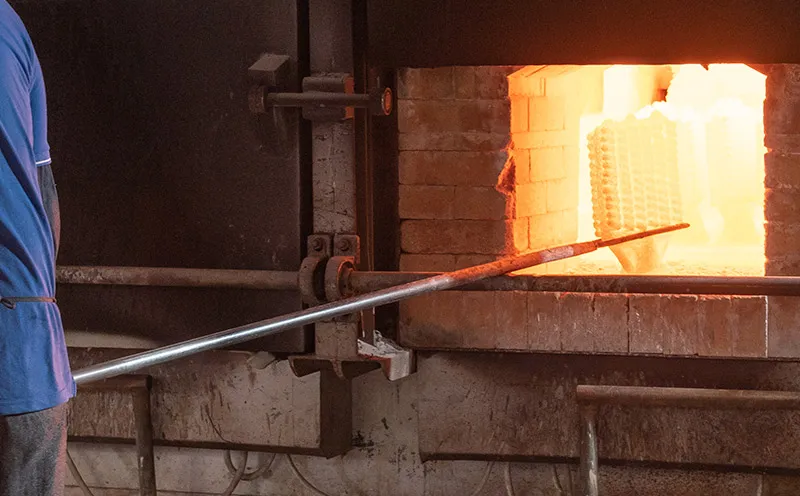
Cold die casting, unlike its hot chamber counterpart, employs a method where molten metal is injected into a die under high pressure. This process is typically used with metals that have higher melting points, such as aluminum alloys, which are well-regarded in industries like automotive, aerospace, and consumer electronics due to their strength and lightweight properties.
One of the greatest advantages of cold die casting is its ability to produce complex parts with a high degree of accuracy and uniformity. This precision is facilitated by the use of advanced casting systems that ensure the molten metal is evenly distributed and cooled throughout the mold. My extensive experience in the manufacturing sector has shown me that these characteristics are invaluable when producing parts that require stringent dimensional tolerances and aesthetic consistency. Manufacturers looking to enhance product quality and minimize material waste find cold die casting an indispensable technique.

Expertise in this domain reveals another significant benefit the adaptability of cold die casting.
This process supports a diverse range of alloy compositions, each tailored to specific engineering requirements. For example, aluminum and zinc alloys often play pivotal roles in creating components that demand robust mechanical properties while simultaneously minimizing the overall weight of the product. This flexibility not only permits the production of bespoke parts but also fosters innovation, allowing designers the freedom to explore new architectural concepts without being constrained by material limitations.
cold die casting
Authoritativeness in any industrial process also draws heavily from its ability to meet environmental and safety standards. Cold die casting holds a reputation for sustainability due to its capability to recycle scrap metal, effectively reducing waste and conserving primary resources. Furthermore, modern cold die casting facilities implement cutting-edge technologies to ensure energy-efficient production processes, contributing to a lower carbon footprint. This commitment to environmental stewardship enhances trust and reliability from both consumers and stakeholders who prioritize sustainability in supply chains.
Trustworthiness in cold die casting is further supported by rigorous quality control measures that are integral to its operations. Techniques such as X-ray inspection and spectroscopic analysis are routinely employed to detect and rectify any defects before components proceed to final assembly. As someone deeply embedded in the industrial landscape, I can confidently assert that the reliability of cold die casting is evidenced by the repeatability of its processes—yielding consistent outcomes batch after batch. This reliability underpins critical sectors such as aerospace, where the integrity of every component can mean the difference between success and catastrophic failure.
For businesses looking to venture into or expand within the cold die casting arena, understanding these facets forms the cornerstone of making informed, strategic decisions. Whether it's selecting the optimal alloy for a new product line or aligning production processes with eco-friendly practices, the nuanced understanding of cold die casting is instrumental in maintaining a competitive edge.
This exploration into the multifaceted world of cold die casting is designed to offer insights that blend real-world experience with expert analysis. It seeks to equip manufacturers, engineers, and decision-makers with the knowledge and confidence to harness the full potential of this versatile and sustainable manufacturing method. As the industry evolves, staying informed about the latest advancements and maintaining a commitment to quality will remain paramount in upholding the esteemed reputation that cold die casting has earned over the decades.