Automotive metal stamping parts play a crucial role in the manufacturing of various vehicle components, ensuring precision, durability, and cost-effectiveness. With decades of engineering evolution, metal stamping has become unparalleled in producing intricate designs precisely required in the modern automotive industry.
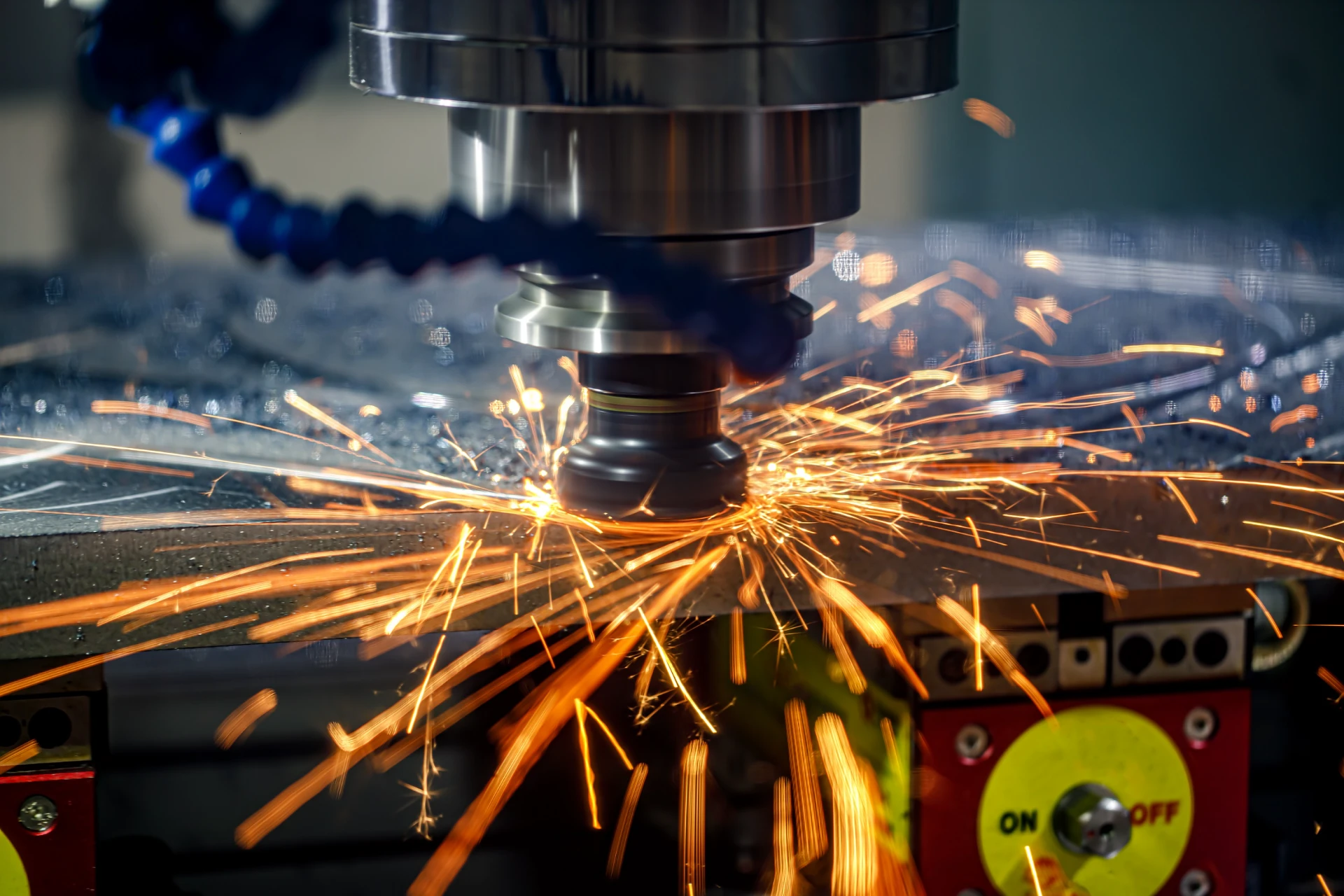
Central to the process is the utilization of advanced presses and dies, which shape metal sheets into desired forms. These components, such as brackets, panels, trims, and structural frames, are vital for constructing cars, trucks, and even electric vehicles, impacting performance and safety. Automotive metal stamping encompasses a wide variety of metals, although steel, aluminum, and various alloys dominate the landscape due to their robustness and adaptability.
Expertise in automotive stamping begins with an understanding of the extensive tooling involved. Companies invest heavily in developing custom dies tailored to specific production needs, enabling large-scale manufacturing with minimal waste. This level of expertise ensures repeatability and adherence to strict tolerances, critical in an industry that demands perfection in every part—to not only meet regulatory requirements but to exceed consumer expectations.
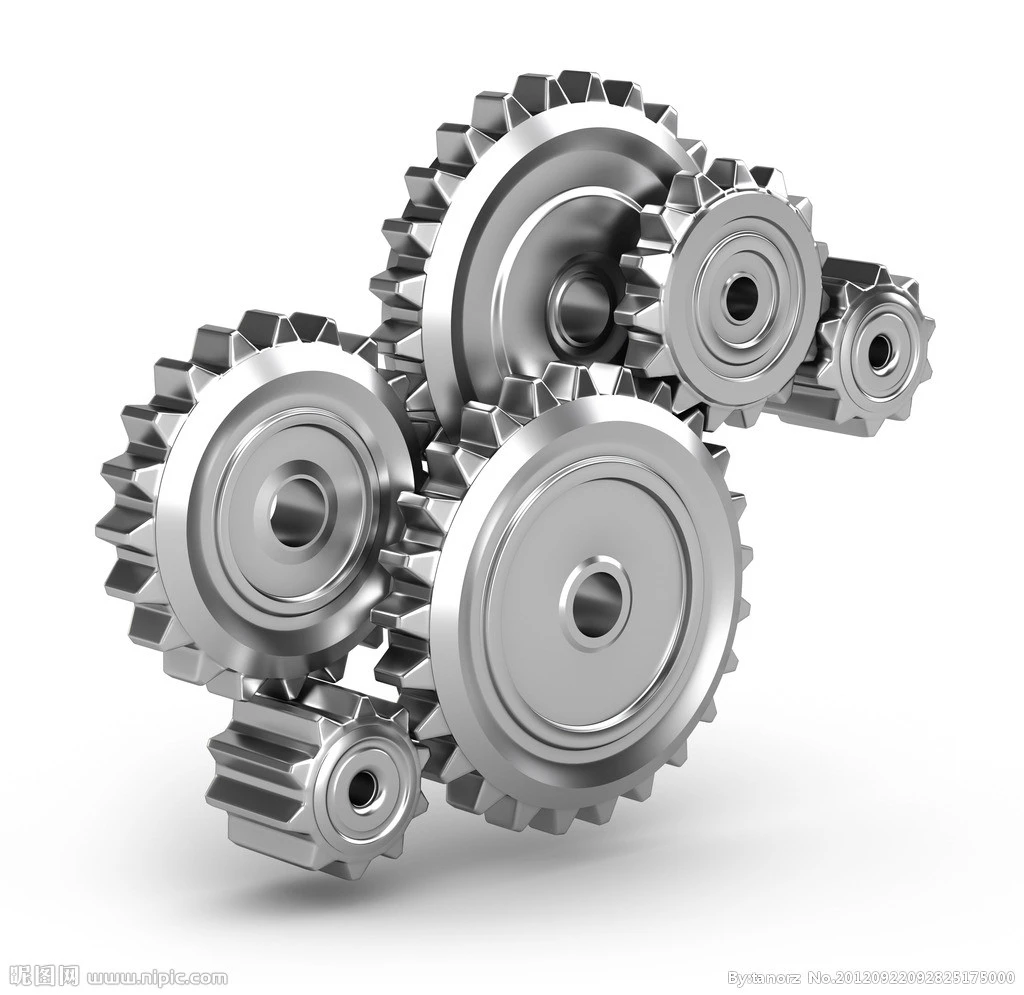
Technological advancements have revolutionized stamping processes, incorporating computer-aided design (CAD) and computer-aided manufacturing (CAM) systems. These innovations allow precision engineers to predict outcomes with astonishing accuracy, providing a tangible pathway from design to production. Real-time adjustments through software minimize errors and reduce downtime, offering significant cost savings and improved output efficiency.
A key component of trustworthiness in the production of automotive metal stamping parts is material quality and sourcing. Reputable manufacturers maintain rigorous standards when selecting raw materials. They adhere to stringent industry benchmarks, such as ISO certifications, ensuring that each batch of metal is capable of withstanding the pressures and strains it will face once implemented. Such meticulous attention to material choice boosts the end product's longevity and performance.
automotive metal stamping parts
The expertise to execute effective stamping operations also extends to workforce skill. Engineers and technicians undergo ongoing training to stay abreast of the latest trends and technologies, ensuring consistent delivery of top-quality components. This blend of experienced labor and cutting-edge technology forms the backbone of successful operations in automotive metal stamping, providing clients with assurance of quality and dependability.
Authoritativeness is further established through continuous innovation. Leading manufacturers relentlessly pursue research and development to refine processes and expand capabilities. Engaging in partnerships with automotive giants and participating in global forums reflects a commitment to being at the forefront of metal stamping technology. Through shared knowledge and collaborative efforts, these companies assert themselves as significant contributors to the industry.
The future of automotive metal stamping promises even greater strides, driven by the rise of electric vehicles and sustainability concerns. Lightweight alloys are becoming the norm, and engineers are tasked with balancing reduced weight with enhanced strength. This shift is set to transform the landscape substantially, demanding adaptive strategies and forward-thinking solutions from industry leaders.
In conclusion, expertise, authoritativeness, and trustworthiness intertwined with rich experience form the foundation of the automotive metal stamping industry. They perpetuate a culture of excellence and inspire confidence among stakeholders, from manufacturers to end consumers, ensuring that this pivotal sector remains innovative and reliable in meeting the ever-evolving needs of the modern automotive world.